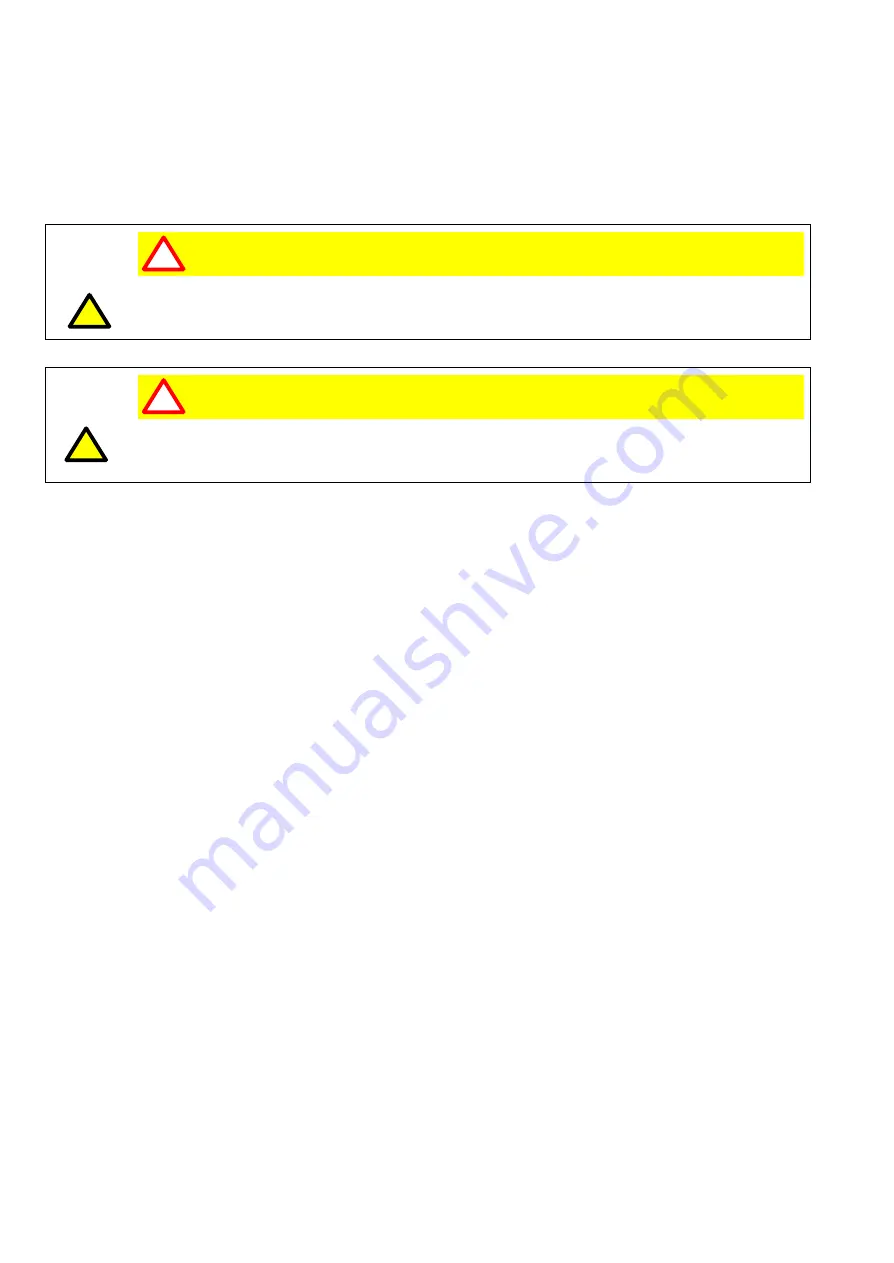
16
300544660_002_C1
11/2016
- © Leybold
5
Operations
5.1 Pressure Output
The transmitter can provide pressure measurement output as an analog voltage value or RS232 digital value. For
details about the digital interface please refer to RS232 Interface Manual 300544665 for additional information.
Resolution
The analog pressure output can provide resolution of pressure changes as low as 0.003% of the full-scale
measurement range under ideal conditions. However, in most industrial and non-metrology installations, the lowest
measurable pressure will be approximately 0.01% of the full-scale range, or 1 mV. This resolution is determined
by the transmitter’s resident noise level, the noise and ripple occurring on the input power supply to the transmitter,
shifts in ambient temperature around the transmitter, and several other factors.
Measuring Noise
External sources can interfere with the sensor signal and cause noise on the signal. The lowest measurement
ranges (below 1 Torr) are most sensitive to measuring noise due to low signal levels.
Closed-Loop Pressure Control
The transmitter’s output s
ignal can be used as a reference for a closed-loop pressure control system. In such a
system, the analog or digital output of the transmitter is sent to a dedicated controller or control element, which
then compares the actual chamber pressure as read by the transmitter to an established set point. The controller
then decides based on its internal programming to either open or close the pressure-controlling element(s) to raise
or lower the chamber pressure to meet the set point.
Leybold recommends that the minimum control pressure using this transmitter should be 0.5% of the full-scale
measurement range or 50 mV if the analog output signal is used for this control circuit. Attempting to control
pressure below this minimum may result in less stable pressure control.
When designing external pressure control loops, make sure that external equipment like pumping
system is not damaged in case of power failure.
When designing pressure data collecting software and control loop using data from RS232
communications, make sure that the host software does not interpret a communication error as a
valid pressure value.
Caution
Caution
!
!
!
!