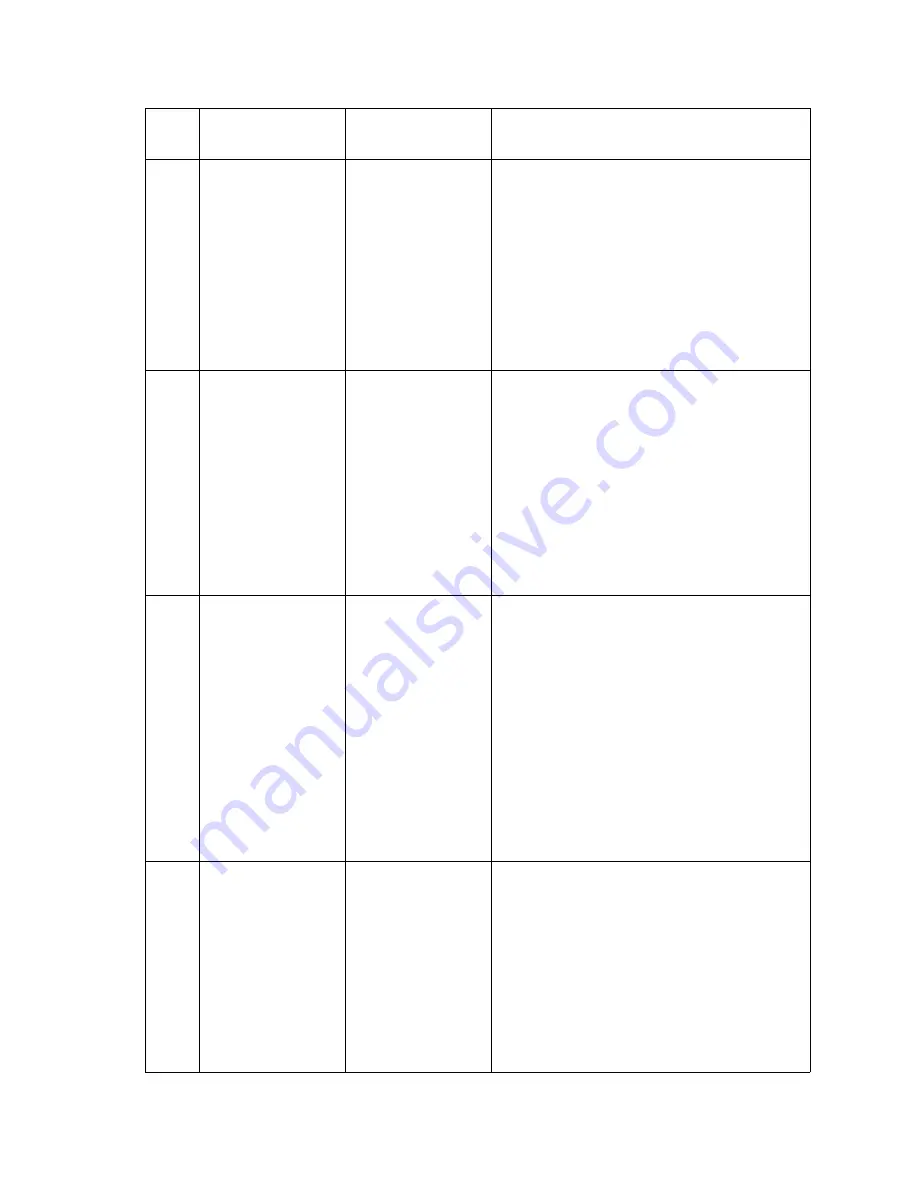
2-26
Service Manual
5060-00
x
203
Paper Jam
Clear paper Path
Leave job in Finisher
Primary: The media is jammed due to a
transparency sensor mismatch. Open the printer
left door to access the jammed media. If sheets
have been accumulated to be stapled or offset
when the jam is detected, the printer alternately
flashes the primary and secondary messages to
indicate that all accumulated sheets should not be
removed during the jam clearing procedure.
Secondary: When this message is displayed, do
not remove accumulated sheets during the jam
clearing procedure. The printer will not reprint the
removed sheets. Also, if the accumulated sheets
are removed, the portion of the job printed after the
jam will not be stapled.
230
Paper Jam
Clear Paper Path
Leave Job in Finisher
Primary: The media is most likely jammed in the
duplex option, remove the duplex tray to access the
jam area. If sheets have been accumulated to be
stapled or offset when the jam occurred, the printer
alternately flashes the primary and secondary
messages to indicate that all accumulated sheets
not be removed during the jam clearing procedure.
If the problem persists, go to
“230 Paper jam” on
page 2-76
.
Secondary: When this message is displayed, do
not remove accumulated sheets during the jam
clearing procedure as the printer will not reprint the
removed sheets. Also, if the accumulated sheets
are removed, the portion of the job printed after the
jam will not be stapled.
24
x
Paper Jam
Clear Paper Path
Leave Job in Finisher
Primary: Media is jammed around Tray
x
(Tray
x
=2
through 4) and applies to both a 500 Tray and HCIT
tray. Try opening Tray
x
. If the tray is difficult to
remove then you may need to remove the tray
above or below Tray
x
to remove the jam. If sheets
have been accumulated to be stapled or offset
when the jam occurred, the printer alternately
flashes the primary and secondary messages to
indicate that all accumulated sheets not be
removed during the jam clearing procedure. If the
problem persists, go to
“24x Paper jam” on
page 2-77
.
Secondary: When this message is displayed, do
not remove accumulated sheets during the jam
clearing procedure as the printer will not reprint the
removed sheets. Also, if the accumulated sheets
are removed, the portion of the job printed after the
jam will not be stapled.
250
Paper Jam
Clear Paper Path
Leave Job in Finisher
Primary: Media is jammed in the MP Feeder. If
sheets have been accumulated to be stapled or
offset when the jam occurred, the printer
alternately flashes the primary and secondary
messages to indicate that all accumulated sheets
not be removed during the jam clearing procedure.
If the problem persists, go to
“250 Paper jam” on
page 2-82
.
Secondary: When this message is displayed, do
not remove accumulated sheets during the jam
clearing procedure as the printer will not reprint the
removed sheets. Also, if the accumulated sheets
are removed, the portion of the job printed after the
jam will not be stapled.
2
xx
code
Primary message
Secondary message
Description
Содержание 13P0195 - C 750dn Color Laser Printer
Страница 14: ...xiv Service Manual 5060 00x ...
Страница 15: ...Laser notice xv 5060 00x ...
Страница 16: ...xvi Service Manual 5060 00x ...
Страница 34: ...1 14 Service Manual 5060 00x ...
Страница 115: ...Diagnostic information 2 81 5060 00x Printer configuration diagrams for 24x paper jams ...
Страница 237: ...Repair information 4 19 5060 00x 9 Remove the MPF swing arm assembly E E ...
Страница 312: ...4 94 Service Manual 5060 00x ...
Страница 313: ...Connector locations 5 1 5060 00x 5 Connector locations Locations Printer boards ...
Страница 315: ...Connector locations 5 3 5060 00x Printer sensors ...
Страница 316: ...5 4 Service Manual 5060 00x Cartridge contact assembly pin locations ...
Страница 317: ...Connector locations 5 5 5060 00x Engine board cabling ...
Страница 318: ...5 6 Service Manual 5060 00x RIP board cabling ...
Страница 344: ...5 32 Service Manual 5060 00x HCOF system board ...
Страница 350: ...7 2 Service Manual 5060 00x Assembly 1 Covers ...
Страница 352: ...7 4 Service Manual 5060 00x Assembly 1 1 Covers ...
Страница 354: ...7 6 Service Manual 5060 00x Assembly 2 Cartridge mounting ...
Страница 356: ...7 8 Service Manual 5060 00x Assembly 3 Fuser 3 2 1 ...
Страница 358: ...7 10 Service Manual 5060 00x Assembly 3 1 Fuser web oiler 1 2 3 ...
Страница 368: ...7 20 Service Manual 5060 00x Assembly 12 Multipurpose feeder MPF ...
Страница 370: ...7 22 Service Manual 5060 00x Assembly 13 500 sheet integrated tray ...
Страница 374: ...7 26 Service Manual 5060 00x Assembly 16 ITU drive assembly 2 4 1 5 3 5 ...
Страница 376: ...7 28 Service Manual 5060 00x Assembly 17 ITU loading ...
Страница 380: ...7 32 Service Manual 5060 00x Assembly 20 Cartridge drive assembly ...
Страница 382: ...7 34 Service Manual 5060 00x Assembly 21 Electronics ...
Страница 384: ...7 36 Service Manual 5060 00x Assembly 21 1 Electronics ...
Страница 388: ...7 40 Service Manual 5060 00x Assembly 21 4 Electronics ...
Страница 390: ...7 42 Service Manual 5060 00x Assembly 22 Electronic cabling engine board ...
Страница 392: ...7 44 Service Manual 5060 00x Assembly 23 Electronic cabling RIP board ...
Страница 396: ...7 48 Service Manual 5060 00x Assembly 26 Output expander ...
Страница 398: ...7 50 Service Manual 5060 00x Assembly 26 1 Output expander ...
Страница 400: ...7 52 Service Manual 5060 00x Assembly 27 5 bin mailbox ...
Страница 402: ...7 54 Service Manual 5060 00x Assembly 27 1 5 bin mailbox ...
Страница 404: ...7 56 Service Manual 5060 00x Assembly 28 500 sheet drawer option ...
Страница 406: ...7 58 Service Manual 5060 00x Assembly 28 1 500 sheet tray option ...
Страница 408: ...7 60 Service Manual 5060 00x Assembly 29 Duplex option ...
Страница 410: ...7 62 Service Manual 5060 00x Assembly 29 1 Duplex option ...
Страница 412: ...7 64 Service Manual 5060 00x Assembly 30 High capacity input tray HCIT ...
Страница 414: ...7 66 Service Manual 5060 00x Assembly 30 1 High capacity input tray HCIT ...
Страница 416: ...7 68 Service Manual 5060 00x Assembly 31 High capacity output finisher HCOF ...
Страница 418: ...7 70 Service Manual 5060 00x Assembly 31 1 High capacity output finisher ...
Страница 420: ...7 72 Service Manual 5060 00x Assembly 31 2 High capacity output finisher ...
Страница 422: ...Service Manual 5060 0xx Assembly 32 High capacity output finisher cables ...
Страница 426: ...7 78 Service Manual 5060 00x ...
Страница 456: ...A 30 Service Manual 5060 00x ...
Страница 458: ...B 2 Service Manual 5060 00x Print Menus Page two of two ...
Страница 459: ...Appendix B Print quality samples B 3 5060 00x Print tests Print Quality Pages Title page total of five ...
Страница 460: ...B 4 Service Manual 5060 00x Print Quality Pages Page 1 total of five ...
Страница 461: ...Appendix B Print quality samples B 5 5060 00x Print Quality Pages Page 2 total of five ...
Страница 462: ...B 6 Service Manual 5060 00x Print Quality Pages Page 3 total of five ...
Страница 463: ...Appendix B Print quality samples B 7 5060 00x Print Quality Pages Page 4 total of five ...
Страница 464: ...B 8 Service Manual 5060 00x Registration Quick Test ...
Страница 465: ...Appendix B Print quality samples B 9 5060 00x Alignment test pages Printhead alignment test pages magenta one of three ...
Страница 466: ...B 10 Service Manual 5060 00x Printhead alignment test page yellow two of three ...
Страница 467: ...Appendix B Print quality samples B 11 5060 00x Printhead alignment test page cyan three of three ...
Страница 468: ...B 12 Service Manual 5060 00x Print Line Len page ...
Страница 487: ......
Страница 488: ......
Страница 489: ......
Страница 490: ......