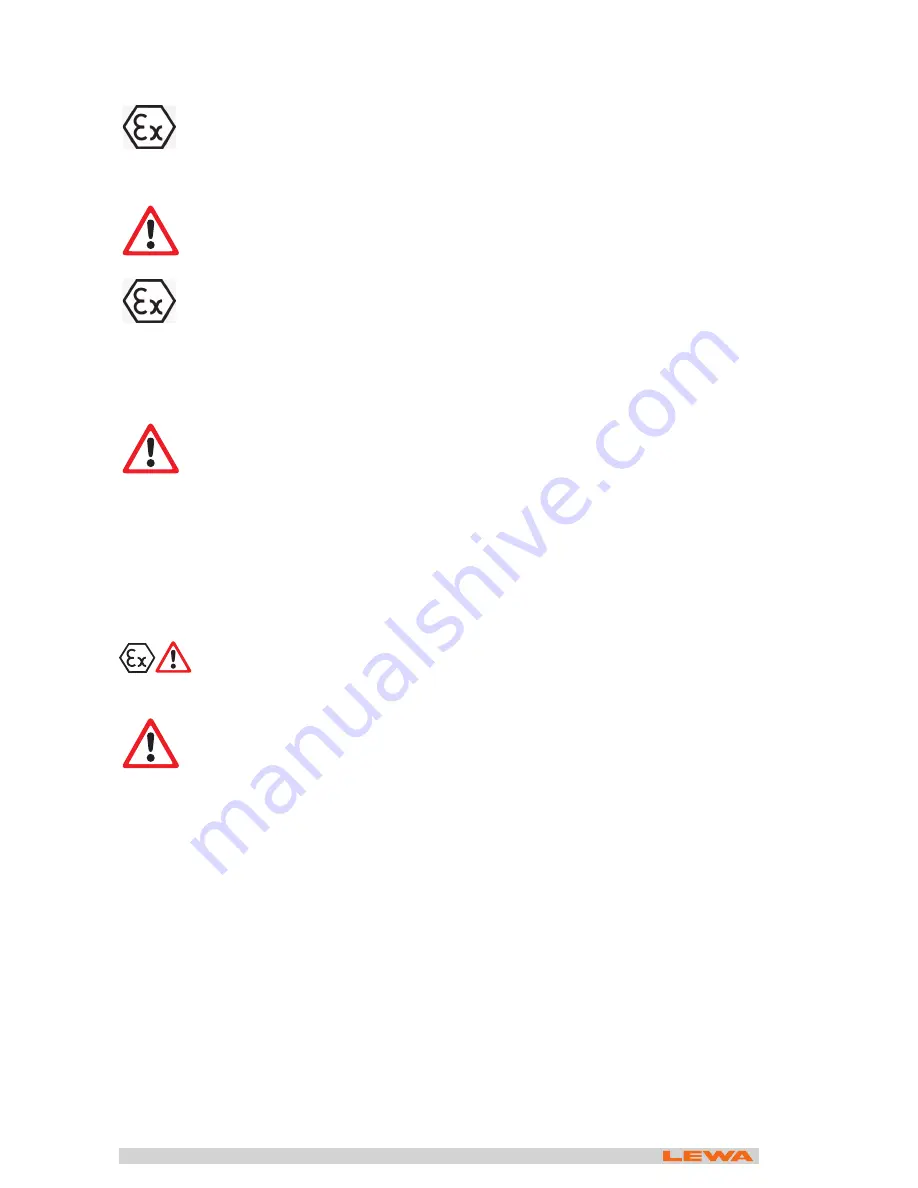
6.1.2 Inspection of coupling clearance
Read and observe enclosed separate operating instruction “Torsionally flexible
jaw coupling in the drive flange" B 1.950.
6.1.3 Grooved ball bearing (16) and grooved ball bearing from adjusting unit (7)
All roller bearings are theoretically designed for a service life of at least 30 000 h.
The effective service life strongly depends on the operating conditions (e.g. load,
quality of lubricant, temperature) and can be considerably longer or also shorter
depending on the individual case.
Break-down of a bearing can lead to unscheduled interruptions and very high heat
build-up locally.
Therefore it is recommended to check drive elements regularly with regard to the
roller bearings. One indication for damaged roller bearings is the development of
noise.
Damage at the bearings can be detected at an early stage with suitable diagnosis
systems.
• Switch off metering pump.
Safeguard drive element against unintentional start-up (disconnect electric
power supply, for this also refer to section “1.4 safety” in operating instruction
B 0.100.1).
Grooved ball bearing (16):
• Unscrew 4 hexagon screws at motor flange and remove motor.
• Dismantling of the grooved ball bearing (16) must be carried out as per section 6.3.1.
• Assembly of grooved ball bearing (16) is carried out as per section 6.3.2.
Grooved ball bearing (part of adjusting unit (7)):
The grooved ball bearing is available and can be installed as complete spare part (adjusting unit) only.
6.1.4 Change of lubricant
Change lubricating oil after 8800 hours of continuous operation or after two years
at the latest.
Changing the lubricant:
Danger of burns when draining hot lubricant!
Assure environmentally safe draining and disposal of spent lubricant.
1. Switch off metering pump.
2. Open screwed plug (40) and drain lubricant (at operating temperature).
3. Open screwed plug (560) and drain residual lubricant from diaphragm pump head with the
hydraulic snifting valve (529) removed.
4. Screw-in screwed plug (40 and 560) observing the torque given in the parts list.
5.
Unscrew air filter (39).
6. Fill correct volume of lubricant into drive element. The lubricant volume depends on the diaphragm
pump head size. For detailed information refer to the operating instruction for the diaphragm pump
head. Refer to section 5.2 for oil grade, and to section 6.1.1 for lubricant level.
7. Reinstall air filter (39) again.
6
B 1.660 en Drive element LEWA - ecosmart® type LCA manual stroke adjust., motor vertically