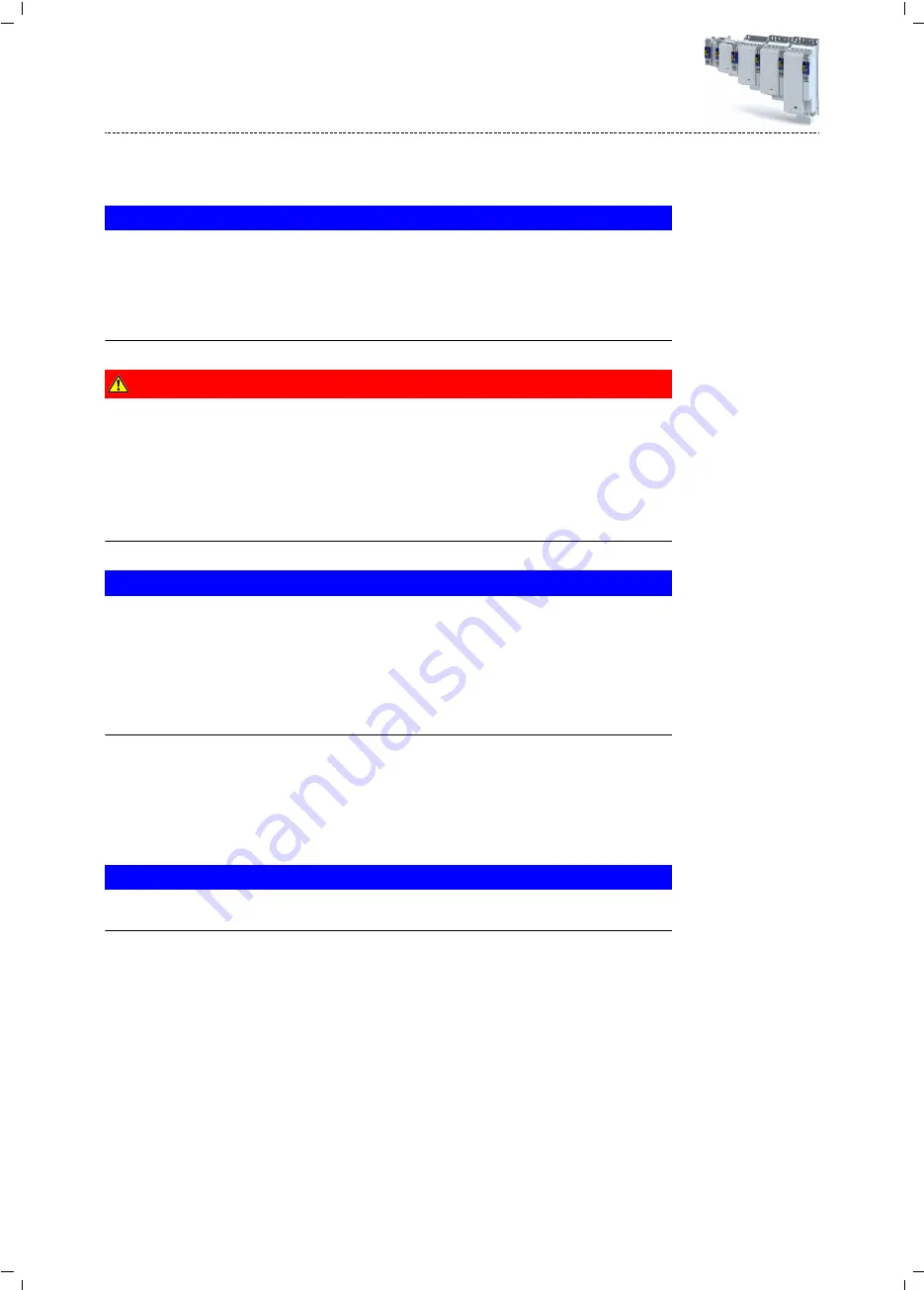
12.4.4
Pole position identification (PPI) without movement
The PLI function can also be used if no motor revolution is possible (holding brake active).
NOTICE
With an incorrect parameter setting and dimensioning of the inverter, the maximum permissi-
ble motor current may be exceeded during the pole position identification.
Possible consequence: irreversible damage of the motor.
▶
Set the motor data correctly.
▶
Only use an inverter that is performance-matched to the motor.
DANGER!
Uncontrolled acceleration of the motor!
Undefined state of the feedback system, caused by wire breakage!
▶
Each pole position identification causes an update of the pole position set in the device!
Therefore, ensure that the response to open circuit in the feedback system is set to Lenze
setting "1: Fault" in
! Otherwise, the status of the feedback system in case of open
circuit is undefined and the pole position can assume any value. There is a danger that the
machine accelerates in an uncontrolled way after pole position identification!
NOTICE
Device state "switched-on"/"operation"
▶
The process of the pole position identification only lasts some milliseconds. During the pole
position identification, the device status does not change. Only after the pole position iden-
tification, the
device status changes to the
device
status.
▶
If pole position identification is started via parameter
, the inverter is automatically
disabled at the end of the pole position identification process.
Preconditions
•
The wiring of the three motor phases and the motor encoder must be carried out accord-
ing to the specifications from the mounting instructions.
•
The inverter is ready for operation (no fault active).
•
For pole position identification (PPI) without movement, the motor must be at standstill.
NOTICE
▶
During the pole position identification, the error 0xFF13 ("identification cancelled") may
occur. This may be an indication that the motor features are not suitable for this PLI process.
Functional description
After inverter enable, a defined pulse pattern is output that provides currents up to approx.
maximum motor current. The respective currents are measured. Based on these currents, the
field distribution can be detected so that the pole position can be calculated. Then, the inver-
ter is automatically disabled.
The pole position identification PLI (without movement) does not need any parameterisation.
Configuring the feedback system
Synchronous motor: Pole position identification (PPI)
Pole position identification (PPI) without movement
234
Содержание i950 Series
Страница 1: ...Inverters i950 servo inverters Commissioning EN ...
Страница 2: ......
Страница 312: ...15 Configure engineering port The given path leads you to the engineering port Configure engineering port 312 ...
Страница 397: ...19 Safety functions Supported safety functions for Basic Safety STO 4Safe Torque Off STO 398 Safety functions 397 ...
Страница 497: ......
Страница 498: ......
Страница 499: ......