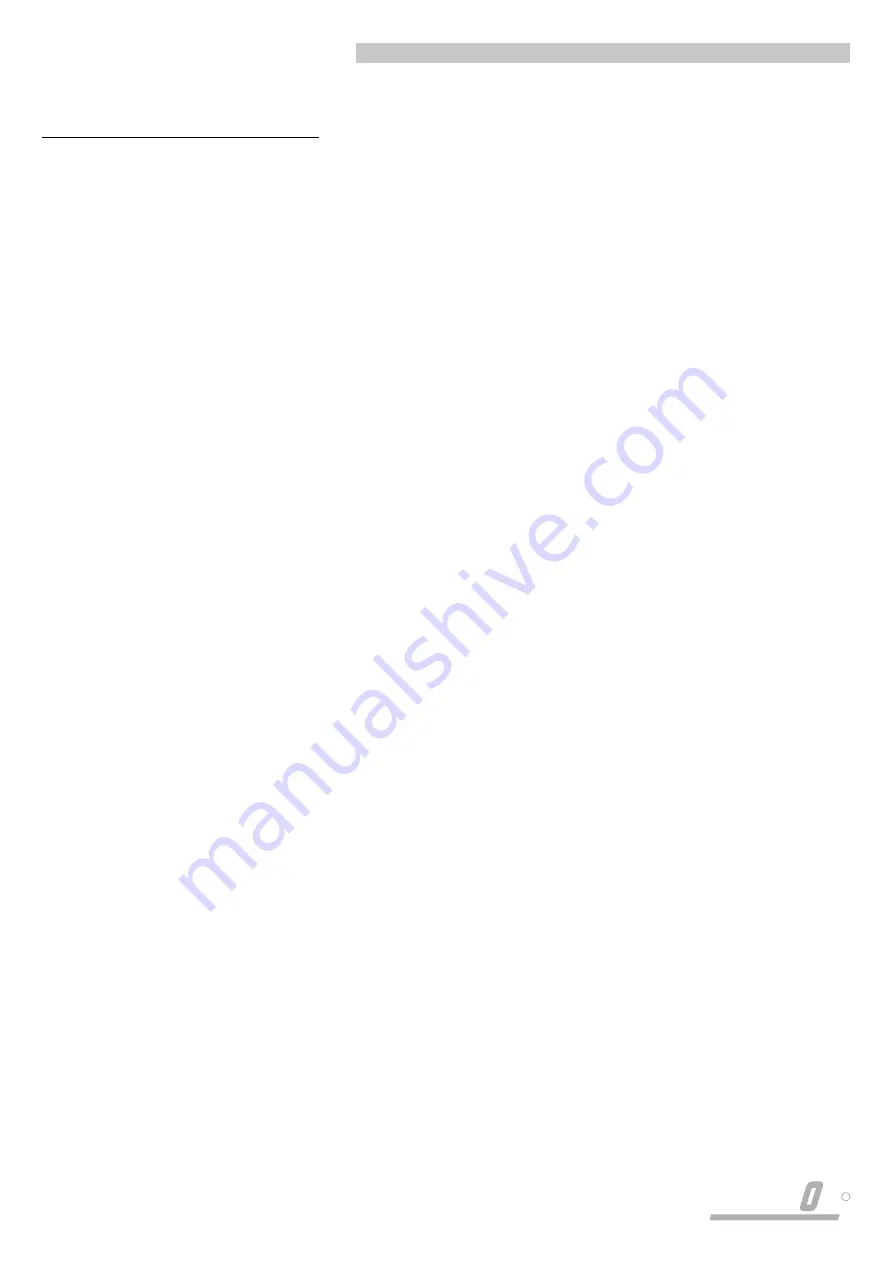
PERIODIC MAINTENANCE PROCEDURE
The following routine maintenance operations should be
carried out twice a year or at such shorter intervals as
may be dictated by climatic conditions or cleanliness of
conditioned space.
1. Routine Precautions
SWITCH OFF POWER SUPPLY AT THE MAINS OUTLET
BEFORE COMMENCING ANY WORK ON THE
EQUIPMENT.
DO NOT OPERATE FAN FOR LONG PERIODS (OVER 2
HOURS) UNDER FREE AIR CONDITIONS. I.E WITHOUT
DUCTWORK CONNECTED.
DO NOT USE STEAM JET OR HIGH PRESSURE HOT
WATER TO CLEAN COIL SURFACES.
2. General
!
Thoroughly clean chassis, baseplate, drain tray.
!
Clean casing. The unit exterior surfaces should be
inspected monthly and any signs of corrosion or
scratches should be treated immediately.
3. Routine Checks
!
Check voltage at supply point with unit running.
4. Condensate Trays
!
Check condensate drains are clean and free running.
!
Check condensate hose connections are secure
and leak free.
!
Clean the condensate tray thoroughly.
!
Check and clean condensate pump if fitted.
!
Check operation of tray, drains or pump by
introducing water into tray.
5. Controls
!
Check all connections for burning or wear. Replace if
necessary.
!
Ensure all electrical connections are secure.
!
Check functions of controls according to operating
procedures.
6. Fan Motor and Fan
A regular check on the fan/motor assembly is
advisable to ascertain if any overheating of the motor
is occurring and that the fan impeller is free running
and has not sustained any damage.
Check that fans and fan motor are properly
aligned.
Check all securing screws, bolts and nuts are tight.
7. Coil
The coil should be inspected every six months to
ascertain if any foreign matter has accumulated
between the fins and that the coil connections are
free from leaks.
Should the fins become contaminated too frequently,
it is advisable to check that the air filter is functioning
correctly.
Use a soft brush and vacuum cleaner to remove any
dust between fins. Comb fins if required.
DO NOT RUN UNIT WITHOUT FILTER FITTED.
8. Filter
Regular cleaning of return air filter is essential, every
three to six months depending on the working
environment of the unit. Dir ty filters will reduce the
air volume handled by the unit, thus adversely
affecting its performance.
Clean the filter using a vacuum cleaner OR remove
the filter from the unit and fully immerse in warm
water with a mild detergent. Rinse in clear water,
allow to dry before replacing.
PERIODIC MAINTENANCE
R
LENN X
6