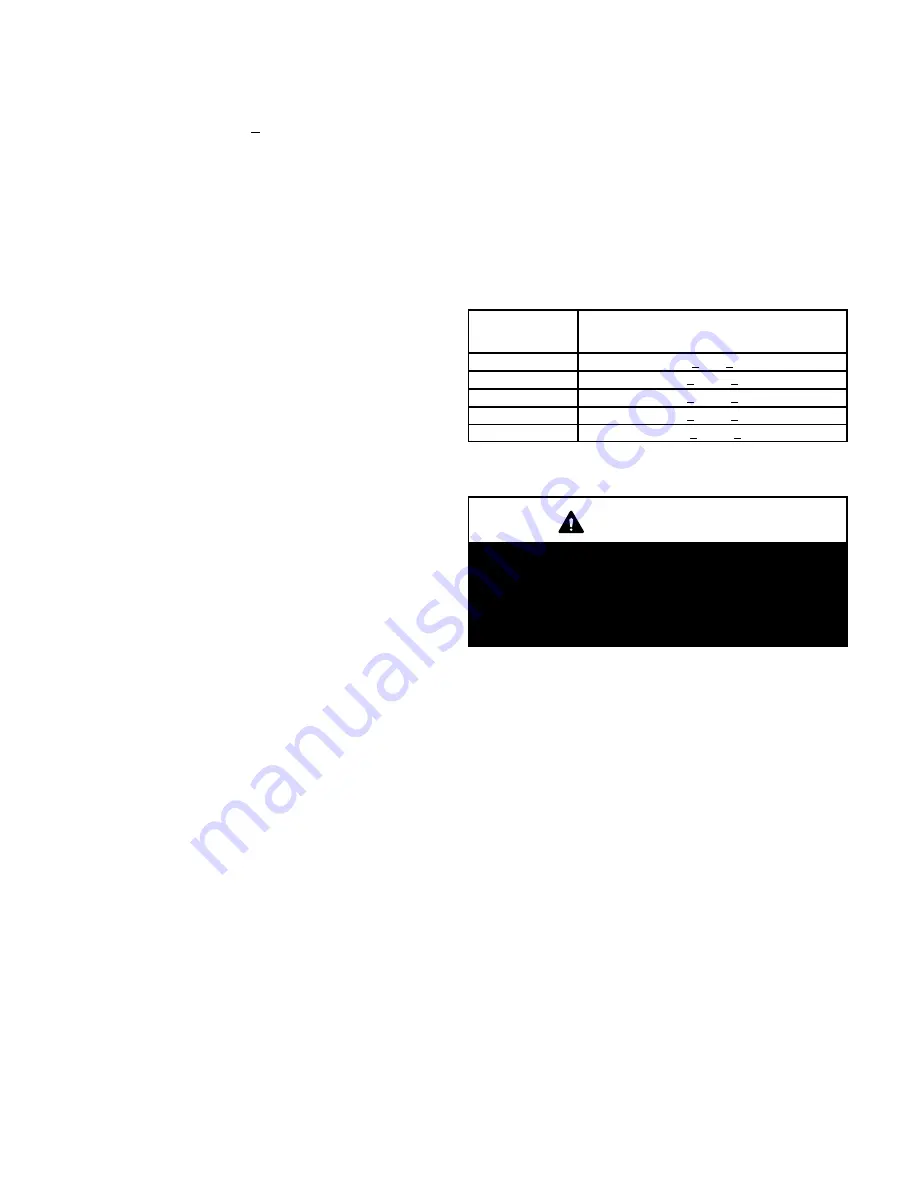
Page 18
Charging Using Normal Operating Pressures
and the Approach Method
Outdoor Temp. > 65
F (18
C)
The following procedure is intended as a general guide and
is for use on expansion valve systems only. For best results,
indoor temperature should be 70°F (21°C) to 80°F (26°C).
Monitor system pressures while charging.
1 − Record outdoor ambient temperature using a digital
thermometer.
2 − Attach high pressure gauge set and operate unit for
several minutes to allow system pressures to stabilize.
3 − Compare stabilized pressures with those provided in
table 6, Normal Operating Pressures." Minor varia-
tions in these pressures may be expected due to differ-
ences in installations. Significant differences could
mean that the system is not properly charged or that a
problem exists with some component in the system.
Pressures higher than those listed indicate that the
system is overcharged. Pressures lower than those
listed indicate that the system is undercharged. A tem-
perature/pressure chart for R410A refrigerant is pro-
vided in table 5 for your convenience. Verify adjusted
charge using the approach method.
Approach Method
4 − Use the same digital thermometer you used to check
the outdoor ambient temperature to check the liquid
line temperature.
5 − The difference between the ambient and liquid temper-
atures should match values given in table 5. If the val-
ues don’t agree with the those in table 5, add refriger-
ant to lower the approach temperature, or recover re-
frigerant from the system to increase the approach
temperature. Be aware of the R410A refrigerant cylin-
der. It will be light maroon−colored. Refrigerant should
be added through the vapor valve in the liquid state.
Some R410A cylinders are equipped with a dip
tube which allows you to draw liquid refrigerant
from the bottom of the cylinder without turning the
cylinder upside−down. The cylinder will be marked
if it is equipped with a dip tube.
Table 5
Model Number
Second Stage (High Capacity)
Approach Temperature
Liquid Line Temp. − Outdoor Ambient °F (°C)
HSXA19−024
1.9 + 1 (1 + .5)
HSXA19−036
6.2 + 1 (3.5 + .5)
HSXA19−038
7.5 + 1 (4.3 + .5)
HSXA19−048
6.0 + 1 (3.3 + .5)
HSXA19−060
10.0 + 1 (5.6 + .5)
NOTE − For best results, the same electronic thermometer
should be used to check both outdoor ambient and liquid line
temperatures.
IMPORTANT
Use table 6 to perform maintenance checks. Table 6
is not a procedure for charging the system. Minor
variations in these pressures may be due to differ-
ences in installations. Significant deviations could
mean that the system is not properly charged or that
a problem exists with some component in the system.