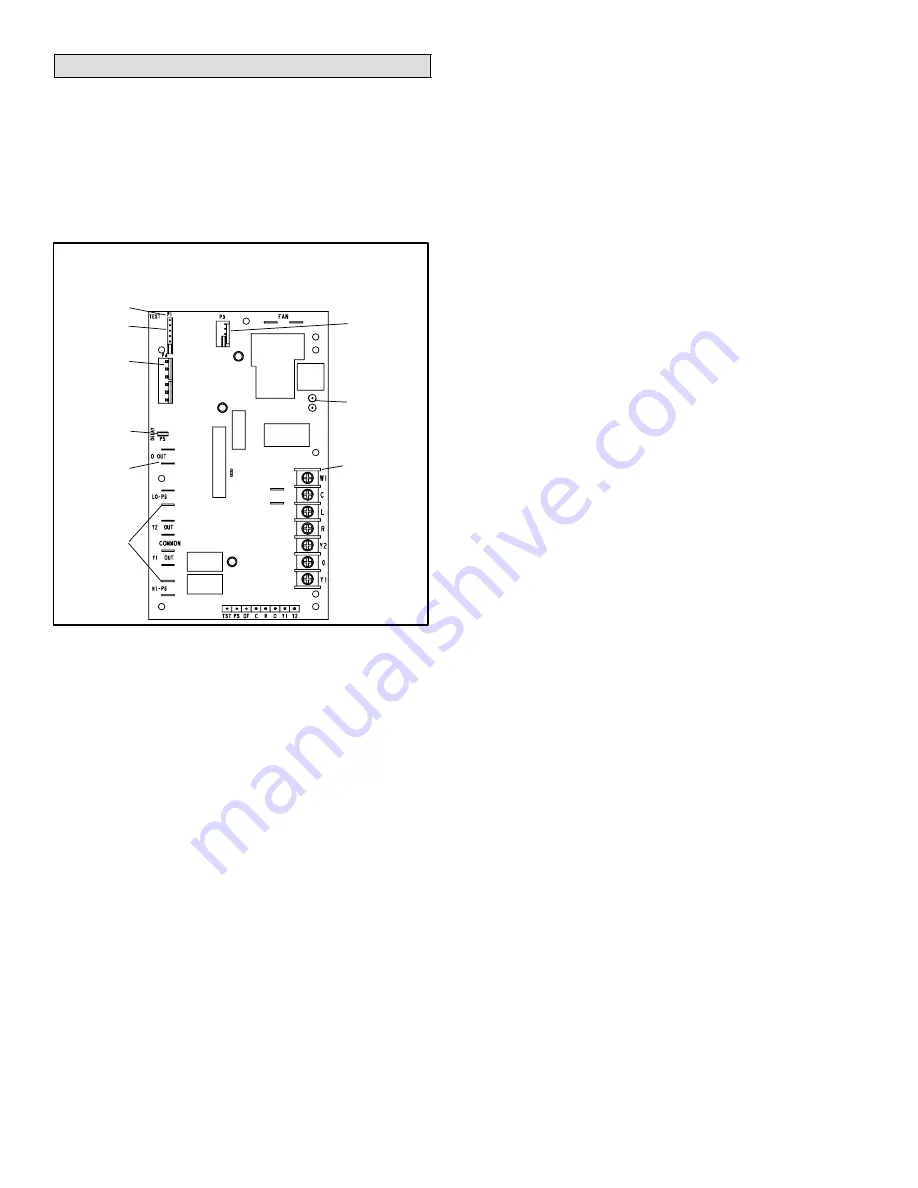
Page 16
504954M 08/06
Defrost System
Defrost System Description
The demand defrost controller measures differential tem-
peratures to detect when the system is performing poorly
because of ice build−up on the outdoor coil. The controller
self−calibrates" when the defrost system starts and after
each system defrost cycle. The defrost control board com-
ponents are shown in figure 19.
Defrost Control Board
24V TERMINAL
STRIP
CONNECTIONS
DIAGNOSTIC
LEDS
PRESSURE
SWITCH CIR-
CUIT CONNEC-
TIONS
TEST PINS
Note − Component Locations Vary by Board Manufacture
r.
SENSOR
PLUG IN
(COIL & AM-
BIENT
SENSORS)
Figure 19
REVERSING
VALVE
DELAY
PINS
LOW
AMBIENT
THERMOSTAT
PINS
DEFROST
TERMINATION
PIN SETTINGS
The control monitors ambient temperature, outdoor coil
temperature, and total run time to determine when a de-
frost cycle is required. The coil temperature probe is de-
signed with a spring clip to allow mounting to the outside
coil tubing. The location of the coil sensor is important for
proper defrost operation.
NOTE − The demand defrost board accurately measures
the performance of the system as frost accumulates on the
outdoor coil. This typically will translate into longer running
time between defrost cycles as more frost accumulates on
the outdoor coil before the board initiates defrost cycles.
Defrost Board Diagnostic LEDs
The state (Off, On, Flashing) of two LEDs on the defrost
board (DS1 [Red] and DS2 [Green]) indicate diagnostics
conditions that are described in table 10 (on page 20).
Defrost Board Pressure Switch Connections
The unit’s automatic reset pressure switches (LO PS − S87
and HI PS − S4) are factory−wired into the defrost board on
the LO−PS and HI−PS terminals, respectively.
Low Pressure Switch (LO−PS)
When the low pressure
switch trips, the defrost board will cycle off the compressor,
and the strike counter in the board will count one strike.
The low pressure switch is ignored under the following
conditions:
during the defrost cycle and 90 seconds after the ter-
mination of defrost
when the average ambient sensor temperature is be-
low 15° F (−9°C)
for 90 seconds following the start up of the compressor
during "test" mode
High Pressure Switch (HI−PS)
When the high pressure
switch trips, the defrost board will cycle off the compressor,
and the strike counter in the board will count one strike.
Defrost Board Pressure Switch Settings
High Pressure
(auto reset) − trip at 590 psig; reset at 418
psig.
Low Pressure
(auto reset) − trip at 25 psig; reset at 55
psig.
Pressure Switch 5−Strike Lockout
The internal control logic of the board counts the pressure
switch trips only while the Y1 (Input) line is active. If a pres-
sure switch opens and closes four times during a Y1 (In-
put), the control logic will reset the pressure switch trip
counter to zero at the end of the Y1 (Input). If the pressure
switch opens for a fifth time during the current Y1 (Input),
the control will enter a lockout condition.
The 5−strike pressure switch lockout condition can be reset
by cycling OFF the 24−volt power to the control board or by
shorting the TEST pins between 1 to 2 seconds. All timer
functions (run times) will also be reset.
If a pressure switch opens while the Y1 Out line is en-
gaged, a 5−minute short cycle will occur after the switch
closes.
Defrost System Sensors
Sensors connect to the defrost board through a field-re-
placeable harness assembly that plugs into the board (see
figure 21). Through the sensors, the board detects outdoor
ambient, coil, and discharge temperature fault conditions.
As the detected temperature changes, the resistance
across the sensor changes. Figure 20 shows how the re-
sistance varies as the temperature changes for both type
of sensors. Sensor resistance values can be checked by
ohming across pins shown shown in table 9.