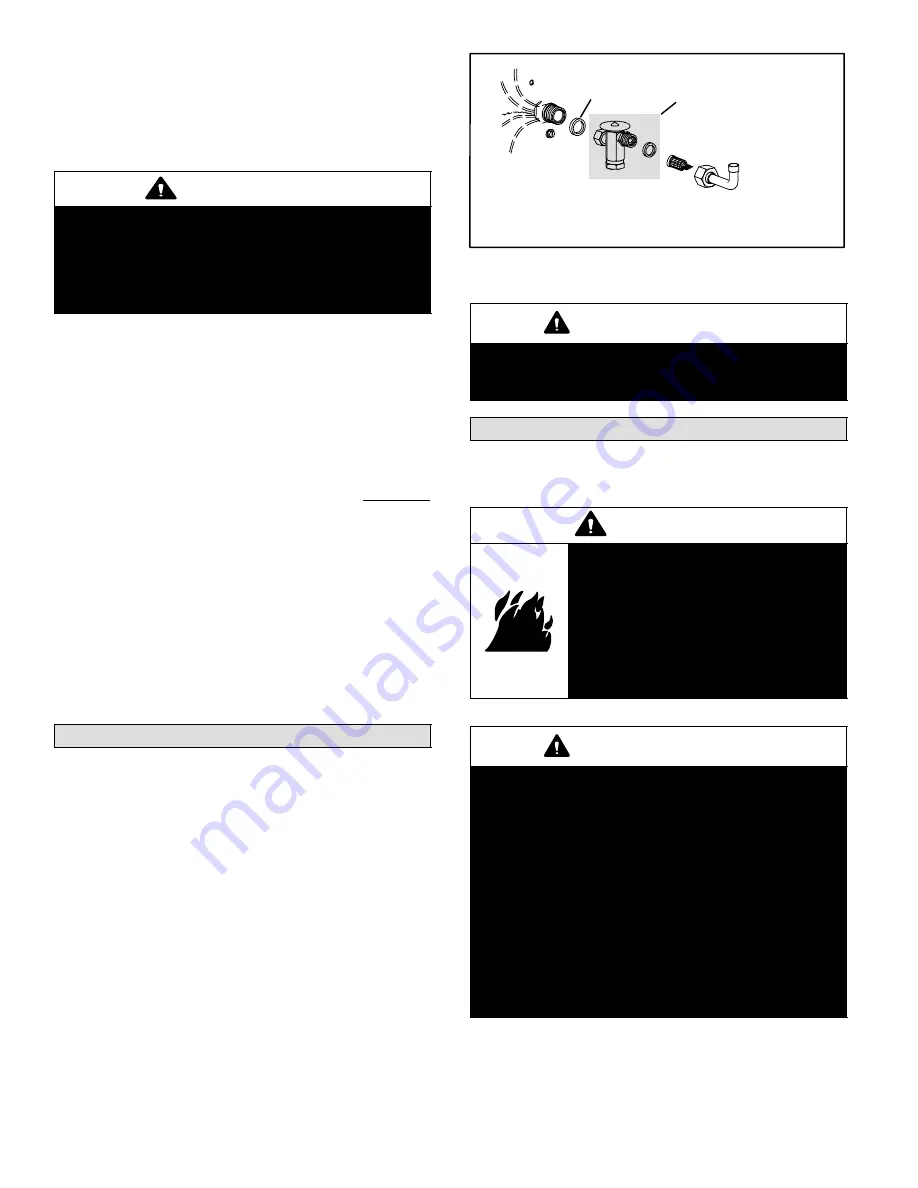
Page 8
504954M 08/06
Isolation Grommets
Locate the provided isolation grommets. Use a knife to slit
the webbing on each grommet. Slide larger grommet onto
vapor line and smaller grommet onto liquid line. Insert
grommets into mullion to isolate refrigerant lines from
sheet metal edges.
WARNING
Polyol ester (POE) oils used with HFC−410A refrig-
erant absorb moisture very quickly. It is very im-
portant that the refrigerant system be kept closed
as much as possible. DO NOT remove line set caps
or service valve stub caps until you are ready to
make connections.
Brazing Connection Procedure
1. The end of the refrigerant line must be cut square and
its internal shape must remain round. The line must be
free of nicks or dents and must be deburred (I.D. and
O.D.)
2. Before making line set connections, use dry nitrogen
to purge the refrigerant piping. This will help to prevent
oxidation and the introduction of moisture into the sys-
tem.
3. Use silver alloy brazing rods (5 or 6 percent
minimum
silver alloy for copper−to−copper brazing or 45 percent
silver alloy for copper−to−brass or copper−to−steel
brazing). Wrap a wet cloth around the valve body and
the copper tube stub. Remove light maroon washers
from service valves and shield light maroon stickers in
order to protect them during brazing. Braze the line set
to the service valve.
4. Quench the joint with water or a wet cloth to prevent
heat damage to the valve core and opening port.
NOTE − The tube end must stay bottomed in the fitting
during final assembly to ensure proper seating, seal-
ing and rigidity.
Refrigerant Metering Device
HPXA16 units may be used in check expansion valve
(CTXV) systems only. See indoor coil installation instruc-
tions and the Lennox engineering handbook for approved
HFC−410A TXV match−ups and application information.
NOTE − HFC−410A systems will not operate properly with
an HCFC−22 valve.
Check Expansion Valve Systems
Check expansion valves equipped with either Chatleff or
flare−type fittings are available from Lennox. Refer to the
Engineering Handbook for applicable expansion valves for
use with specific match-ups.
If you install a check expansion valve with an indoor coil
that includes a fixed orifice, remove the orifice before the
check expansion valve is installed. See figure 13 for instal-
lation of the check expansion valve.
EXPANSION VALVE &
O−RING (See NOTE)
Metering Device Installation
STRAINER
LIQUID LINE
STUB
DISTRIBUTOR
Figure 13
O−RING
NOTE − If necessary, remove HCFC−22 flow control device (fixed
orifice/check expansion valve) from existing line set before installing
HFC−410A approved expansion valve and o−ring.
IMPORTANT
Failure to remove a fixed orifice when installing an
expansion valve on the indoor coil will result in im-
proper operation and damage to the system.
Flushing Existing Line Set & Indoor Coil
NOTE − If the indoor unit line and set are new, skip this sec-
tion and go on to the Manifold Gauge Set section.
WARNING
Danger of fire. Bleeding the refriger-
ant charge from only the high side
may result in the low side shell and
suction tubing being pressurized. Ap-
plication of a brazing torch while
pressurized may result in ignition of
the refrigerant and oil mixture − check
the high and low pressures before un-
brazing.
IMPORTANT
If this unit is being matched with an approved line
set or indoor coil which was previously charged
with HCFC−22 refrigerant, or if it is being matched
with a coil which was manufactured before Janu-
ary of 1999, the coil and line set must be flushed
prior to installation. Take care to empty all existing
traps.
Polyol ester (POE) oils are used in Lennox units
charged with HFC−410A refrigerant. Residual min-
eral oil can act as an insulator, preventing proper
heat transfer. It can also clog the check expansion
valve, reducing system performance and capacity.
Failure to properly flush the system per the in-
structions below will void the warranty.