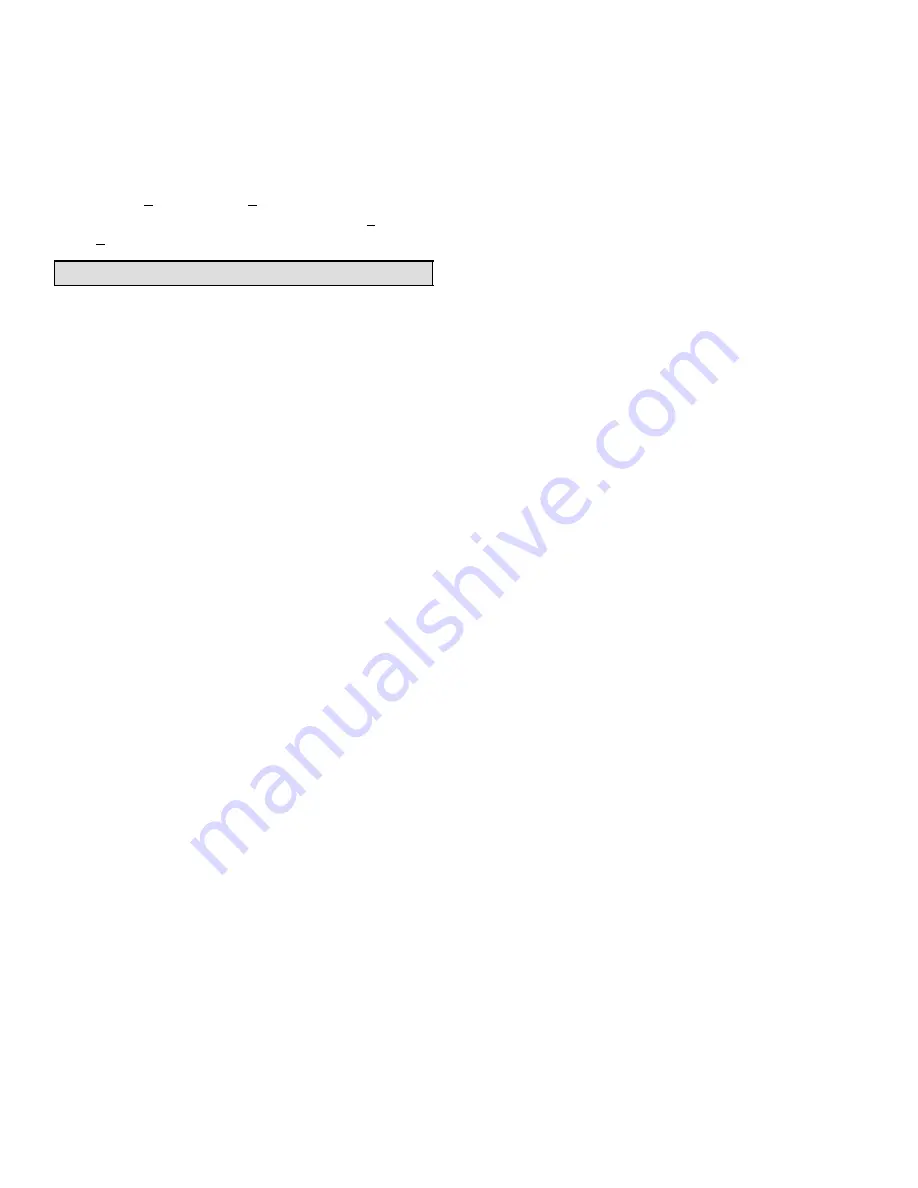
Page 16
High Pressure Switch
The HP27 is equipped with an auto-reset high pressure
switch (single-pole, single-throw) which is located on the
liquid line. The switch shuts off the compressor if the dis-
charge pressure rises above the factory setting. The switch
is normally closed and is permanently adjusted to trip
(open) at 410 + 10 psig (2827 + 69 kPa). The switch resets
(closes) when the pressure drops below 210 + 20 psig
(1448 + 138 kPa).
Defrost System
The defrost system includes two components:
a defrost thermostat
a defrost control
Defrost Thermostat
The defrost thermostat is located on the liquid line be-
tween the check/expansion valve and the distributor.
When the defrost thermostat senses 42°F (5.5°C) or cool-
er, its contacts close and send a signal to the defrost con-
trol board to start the defrost timing. It also terminates de-
frost when the liquid line warms up to 70°F (21°C).
Defrost Control
The defrost control board includes the combined func-
tions of a time/temperature defrost control, defrost
relay, time delay, diagnostic LEDs, and a terminal strip
for field wiring connections. See figure 17.
The control provides automatic switching from normal
heating operation to defrost mode and back. During com-
pressor cycle (call for defrost), the control accumulates
compressor run times at 30, 60, or 90 minute field adjust-
able intervals. If the defrost thermostat is closed when the
selected compressor run time interval ends, the defrost
relay is energized and defrost begins.
Defrost Control Timing Pins
Each timing pin selection provides a different accumu-
lated compressor run time period during one thermostat
run cycle. This time period must occur before a defrost
cycle is initiated. The defrost interval can be adjusted to
30 (T1), 60 (T2), or 90 (T3) minutes. See figure 17. The
defrost timing jumper is factory−installed to provide a
90−minute defrost interval. If the timing selector jumper is
not in place, the control defaults to a 90−minute defrost
interval. The maximum defrost period is 14 minutes and
cannot be adjusted.
A TEST option is provided for troubleshooting.
The TEST
mode may be started any time the unit is in the heating
mode and the defrost thermostat is closed or jump-
ered.
If the jumper is in the TEST position at power-up, the
control will ignore the test pins. When the jumper is placed
across the TEST pins for two seconds, the control will enter
the defrost mode. If the jumper is removed before an addi-
tional 5−second period has elapsed (7 seconds total), the
unit will remain in defrost mode until the defrost thermostat
opens or 14 minutes have passed. If the jumper is not re-
moved until after the additional 5−second period has
elapsed, the defrost will terminate and the test option will
not function again until the jumper is removed and re−ap-
plied.
Time Delay
The timed−off delay is five minutes long. The delay helps
protect the compressor from short−cycling in case the power
to the unit is interrupted or a pressure switch opens. The
delay is bypassed by placing the timer select jumper across
the TEST pins for 0.5 seconds.
Pressure Switch Circuits
The defrost control includes two pressure switch circuits.
The high pressure switch (S4) is factory−connected to the
board’s HI PS terminals. The board also includes LO PS ter-
minals to accommodate the addition of a field−provided low
pressure or loss of charge pressure switch. See figure 17.
This feature is available on all units.
During a single demand cycle, the defrost control will lock
out the unit after the third time that the circuit is interrupted
by any pressure switch that is wired to the control board. In
addition, the diagnostic LEDs will indicate a locked out
pressure switch after the third occurrence of an open pres-
sure switch. See table 7. The unit will remain locked out un-
til power is broken then remade to the control or until the
jumper is applied to the TEST pins for 0.5 seconds.
NOTE − The defrost control board ignores input from the
low pressure switch terminals during the TEST mode, dur-
ing the defrost cycle, during the 90−second start−up period,
and for the first 90 seconds each time the reversing valve
switches heat/cool modes.
If the TEST pins are jumpered
and the 5−minute delay is being bypassed, the LO PS
terminal signal is not ignored during the 90−second
start−up period.
Ambient Thermistor & Service Light Connection
The defrost control board provides terminal connections
for the ambient thermistor and a service light. The thermis-
tor compensates for changes in ambient temperature
which might cause thermostat droop. The service light
thermostat provides a signal which activates the room ther-
mostat service light during periods of inefficient operation.
Diagnostic LEDs
The defrost board uses two LEDs for diagnostics. The
LEDs flash a specific sequence according to the diagnosis.