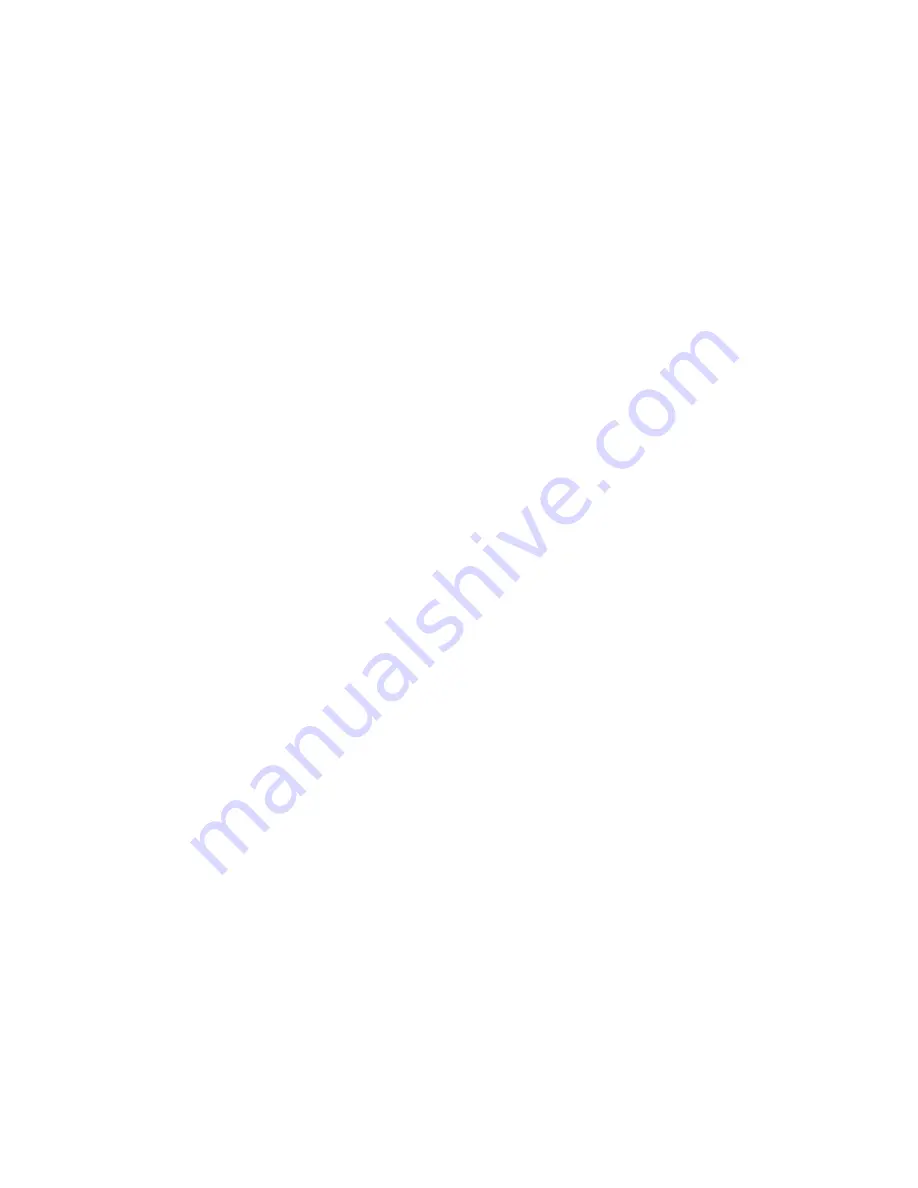
Page 17
Electronic Ignition
At the beginning of the heat cycle the SureLight
®
integrated
control monitors the low fire combustion air inducer pres-
sure switch. The control will not begin the heating cycle if
the low fire pressure switch is closed (by−passed). Likewise
the control will not begin the high fire heating cycle if the
high fire pressure switch is closed, and will remain in low
fire heat. However, if the high fire pressure switch closes
during the low fire heat pre−purge, the control will allow high
fire heat. Once the low fire pressure switch is determined to
be open, the combustion air inducer is energized on igni-
tion speed. When the differential in the pressure switch is
great enough, the pressure switch closes and a 15−second
pre−purge begins. If the switch is not proven within 2−1/2
minutes, the inducer is de−energized and the control will ini-
tiate vent calibration. If the vent calibration is unsuccessful
the control goes into a 5 minute delay. The control will at-
tempt vent calibration 3 more times before going into a 1
hour soft lockout.
After the 15 second pre−purge period the SureLight ignitor
warms up for 20 seconds after which the gas valve opens
for a 4−second trial for ignition. The ignitor stays energized
during this trial until flame is sensed. If ignition is not proven
during the 4−second trial for ignition, the control will try four
more times with an inter purge and warm−up time between
trials of 35 seconds. After a total of five trials for ignition (in-
cluding the initial trial), the control goes into Watchguard−
Flame Failure mode. After a 60−minute reset period, the
control will begin the ignition sequence again.
Thermostat Selection Modes
See table 14 for DIP switch settings
The control can be made to operate in three modes: vari-
able capacity, three−stage timed or two−stage. The variable
capacity and two−stage modes are only operational with a
two−stage thermostat. The thermostat selection is made
using dip switches one and / or two (figure 4) and must be
positioned for the particular application.
Variable Capacity
Using a two−stage thermostat the system will operate in a
variable capacity sequence mode. In this mode, the control
will vary the firing rate anywhere between 40% and 100%
of full capacity. The indoor blower will be automatically ad-
justed accordingly to provide the appropriate airflow at any
rate. On the initial call for low fire, the furnace will operate at
40% and will remain there until the heat call is satisfied or a
call for high fire is initiated. If there is a call for high fire the
rate will increase
by
10% if the current rate is above 60%.
However if the current rate is below 60% the rate will in-
crease
to
70%. After this initial rate increase to 70% capac-
ity, the furnace will increase rate by 10% every 5 minutes
while a high fire heat call is present. If the high fire heat call
is satisfied but the low fire heat call is still present, the fur-
nace will remain at the current firing rate until the demand is
satisfied or another call for high fire is initiated.
Three Stage Timed
Using a single−stage thermostat the system will operate in
a three stage timed mode. Upon a call for heat and a suc-
cessful ignition, the combustion air inducer will operate at
40% and the indoor blower will adjust to the appropriate
cfm. After a field selectable 7 or 12 minute delay period, the
inducer RPM will increase and the unit will operate at 70%.
The indoor blower will adjust to the appropriate cfm. After a
factory set non−adjustable 10 minute delay expires the fur-
nace will increase rate to 100%. The indoor blower will ad-
just to the appropriate cfm.
Two−Stage
The system will also operate in conventional two−stage
mode. While in two−stage mode, the furnace will fire on low
fire (70% rate). The combustion air inducer will operate at
70% and the indoor blower will adjust to the appropriate
cfm. The unit will switch to high fire on a W2 call from the
thermostat. After a 30 second recognition period (during
which the integrated control will recieve a continuous W2
call) expires the furnace will increase to 100% rate. The in-
ducer will increase to 100% speed and the indoor blower
will adjust to appropriate cfm. If there is a simultaneous call
for first and second stage heat, the unit will fire on first stage
heat and switch to second stage heat after 30 seconds of
operation.