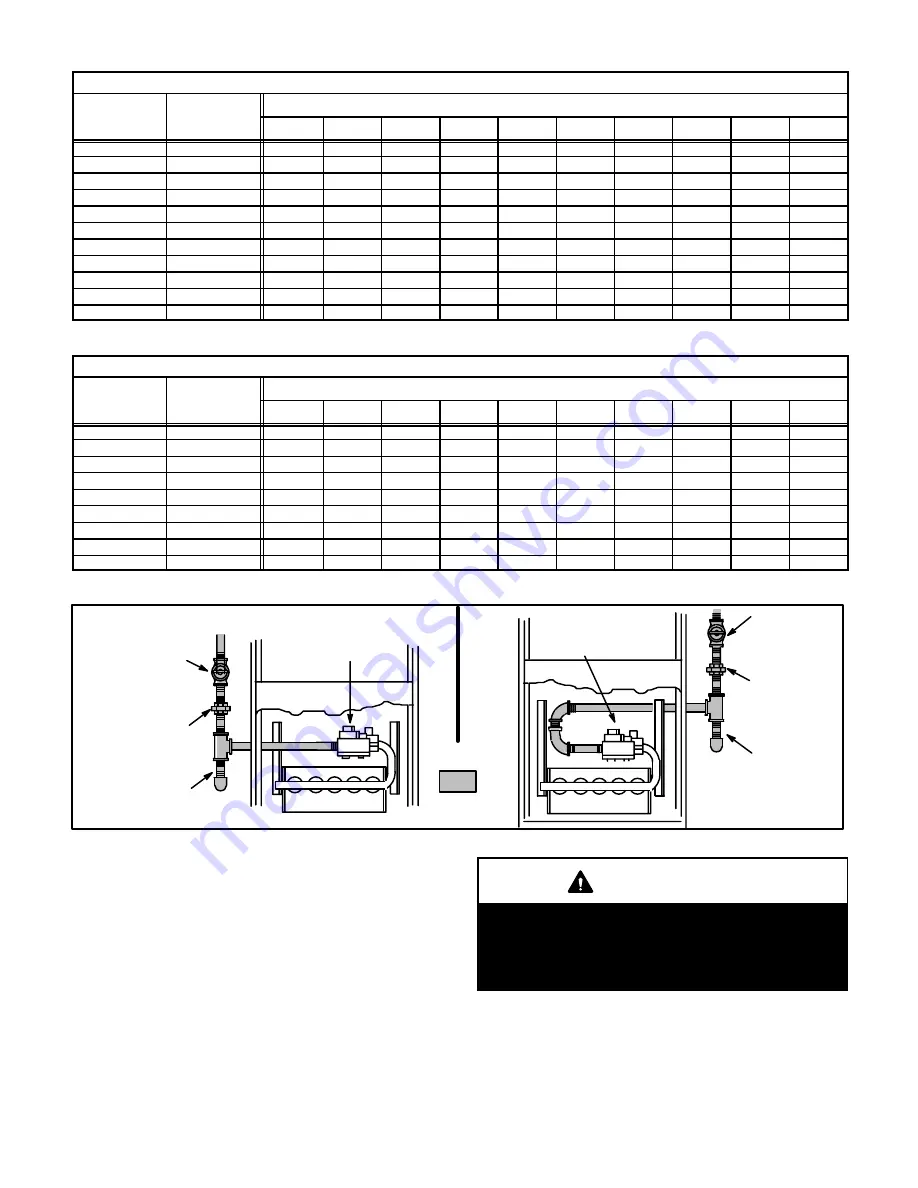
Page 14
TABLE 4 - GAS PIPE CAPACITY (FT
3
/HR)
Nominal
Iron Pipe Size
Internal
Diameter
Length of Pipe - feet
Iron Pipe Size
inches
Diameter
inches
10
20
30
40
50
60
70
80
90
100
1/4
.364
43
29
24
20
18
16
15
14
13
12
3/8
.493
95
65
52
45
40
36
33
31
29
27
1/2
.622
175
120
97
82
73
66
61
57
53
50
3/4
.824
360
250
200
170
151
138
125
118
110
103
1
1.049
680
465
375
320
285
260
240
220
205
195
1-1/4
1.380
1,400
950
770
660
580
530
490
460
430
400
1-1/2
1.610
2,100
460
1,180
990
900
810
750
690
650
620
2
2.067
3,950
2,750
2,200
1,900
1,680
1,520
1,400
1,300
1,220
1,150
2-1/2
2.469
6,300
4,350
3,520
3,000
2,650
2,400
2,250
2,050
1,950
1,850
3
3.068
11,000
7,700
6,250
5,300
4,750
4,300
3,900
3,700
3,450
3,250
4
4.026
23,000
15,800
12,800
10,900
9,700
8,800
8,100
7,500
7,200
6,700
NOTE-Capacity given in cubic feet of gas per hour and based on 0.60 specific gravity gas.
TABLE 5 - GAS PIPE CAPACITY (M
3
/HR)
Nominal
Iron Pipe Size
Internal
Diameter
Length of Pipe - metres
Iron Pipe Size
inches
Diameter
inches
3
6
9
12
15
18
21
24
27
30
1/2
.622
4.29
3.40
2.74
2.32
2.06
1.87
1.72
1.61
1.50
1.41
3/4
.824
10.20
7.08
5.66
4.81
4.27
3.91
3.54
3.34
3.11
2.91
1
1.049
19.27
13.17
10.62
9.06
8.07
7.36
6.80
6.23
5.80
5.52
1-1/4
1.380
39.67
26.92
21.82
18.70
16.43
15.02
13.88
13.03
12.18
11.33
1-1/2
1.610
59.51
41.37
33.43
28.05
25.50
22.95
21.25
19.55
18.42
17.56
2
2.067
111.93
79.93
62.34
53.84
47.60
43.07
39.67
36.84
34.57
32.58
2-1/2
2.469
178.53
123.27
99.75
85.01
75.09
68.01
63.76
58.09
55.26
52.62
3
3.068
311.72
218.20
117.11
150.19
134.60
121.85
110.52
104.85
97.76
92.10
4
4.026
651.78
447.74
308.89
274.88
249.37
249.37
229.54
212.53
204.03
189.86
NOTE-Capacity given in cubic metres of gas per hour and based on 0.60 specific gravity gas.
GROUND
JOINT
UNION
AUTOMATIC
GAS VALVE
FIELD
PROVIDED
AND INSTALLED
GROUND
JOINT
UNION
LEFT SIDE PIPING (STANDARD)
RIGHT SIDE PIPING
(ALTERNATE)
AUTOMATIC
GAS VALVE
DRIP LEG
(optional)
MANUAL
MAIN SHUT-OFF VALVE
(With 1/8" RC
Plugged Tap Shown)
MANUAL
MAIN SHUT-OFF
VALVE
(With 1/8" RC
Plugged Tap
Shown)
DRIP LEG
(optional)
FIGURE 18
SOUNDNESS CHECK
After gas piping is completed, carefully check all piping
connections (factory- and field-installed) for gas leaks.
Use a leak detecting solution or other preferred means.
NOTE - In case emergency shutdown is required, shut
down main manual gas valve and disconnect electrical
power to unit. These devices should be properly labeled
by the installer.
CAUTION
Some soaps used for leak detection are corrosive
to certain metals. Carefully rinse piping thoroughly
after leak test has been completed. Do not use
matches, candles, flame or other sources of igniĆ
tion to check for gas leaks.
The furnace must be isolated from the gas supply system
by closing its individual manual shut-off valve during any
pressure testing of the gas supply system at pressures
equal to or less than 20 in. w.c. (50 mBAR).