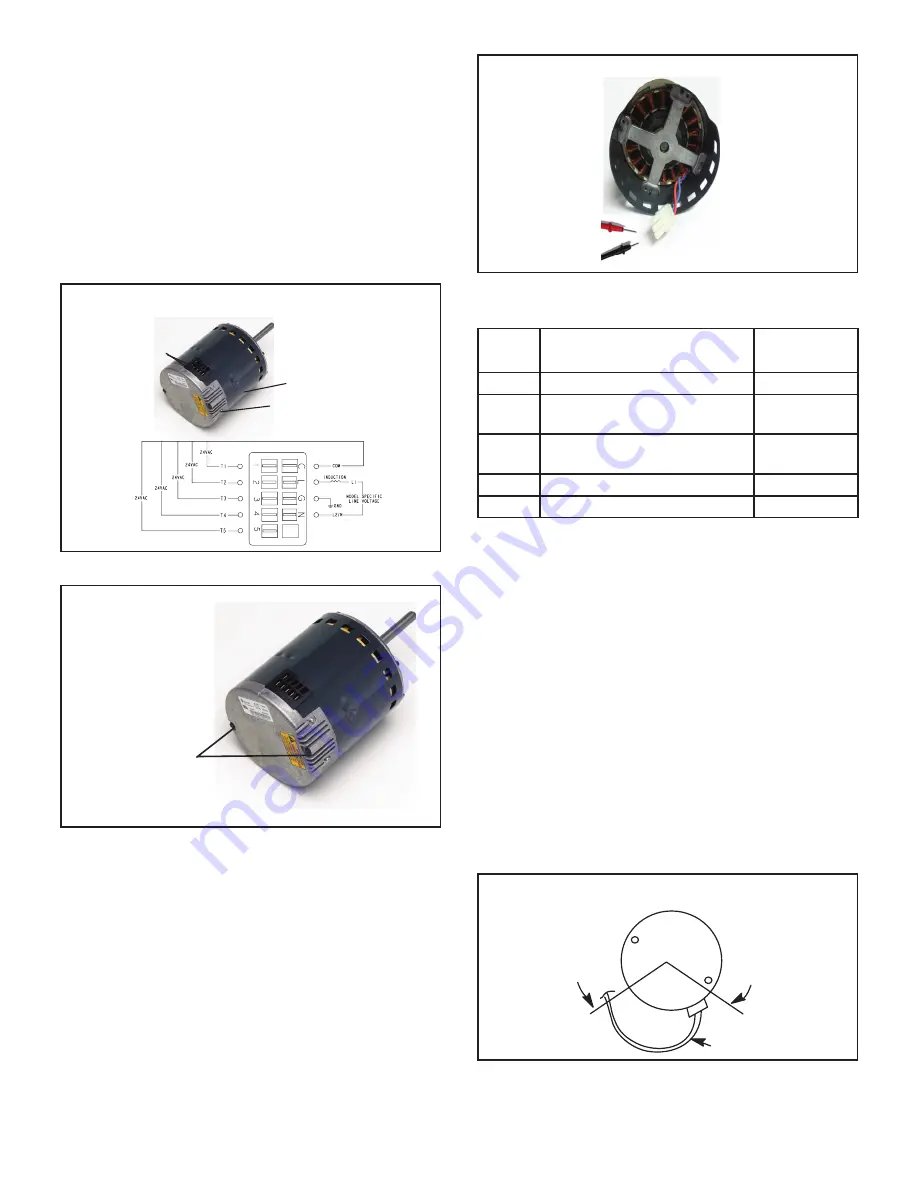
Page 20
Replacing the Motor Module
1 -
Disconnect electrical power to unit.
2 - Remove unit access panel.
3 - Unplug the two harnesses from the motor control
module. See FIGURE 18.
4 - Remove the two hex head bolts securing the motor
control module to the motor (see FIGURE 19).
5 - Slide the motor control module away from the motor
to access and disconnect the internal three wire
connector. It is not necessary to remove blower
motor itself. Set both hex head bolts aside.
TWO HARNESS
CONNECTIONS
MOTOR CONTROL MODULE
MOTOR
Unplug the Two Harness Connection
FIGURE 18
REMOVE BOTH HEX
HEAD BOLTS
Remove the Hex Head Bolts
FIGURE 19
Testing the Motor (FIGURE 20)
If any motor fails the below tests, do not install the new
control module. The motor is defective and it also must be
replaced. The new control can fail if placed on a defective
motor.
1 -
Using an ohmmeter check the resistance from any
one of the motor connector pins to the aluminum
end plate of the motor. This resistance should be
greater than 100k ohms.
2 - Check the resistances between each of the three
motor connector pins. These should all read
approximately the same resistance within an ohm.
3 - Check to see if the blower wheel spins freely.
Motor Test
FIGURE 20
TABLE 9
Scale
Measurement range in
words
ohms
2 M
two megohm-two million ohms
0 - 2,000,000
200 K
two hundred kilo-ohm-two hun
-
dred thousand ohms
0 - 200,000
20 K
twenty kilo-ohm-twenty thousand
ohms
0 - 20,000
2 K
two kilo-ohm two-thousand ohms 0 - 2,000
200
two hundred ohms
0 - 200
Motor Module Installation
All replacement motor control modules look similar; how
-
ever, each module is designed for a specific motor size.
It is very important to make sure that you are using the
correct replacement motor control module.
USE OF THE
WRONG MOTOR CONTROL MODULE MAY RESULT IN
UNEXPECTED UNIT OPERATION.
1 -
Verify electrical power to unit is disconnected.
2 - Connect three-wire harness from motor to control
module.
3 - Mount new motor control module to motor using
two hex head bolts removed in FIGURE 19. Torque
bolts to 22 inch pounds or 1/16th clock wise turn.
4 - Reconnect the two harnesses to the motor control
module.
5 - The electrical connectors of the motor should be
facing down to form a drip loop (FIGURE 21) This
will directs moisture away from the motor and its
electric connections on the motor.
CONNECTOR
ORIENTATION
BETWEEN 4 AND 8
O'CLOCK
BACK OF CONTROL
MODULE
DRIP LOOP
Drip Loop
FIGURE 21