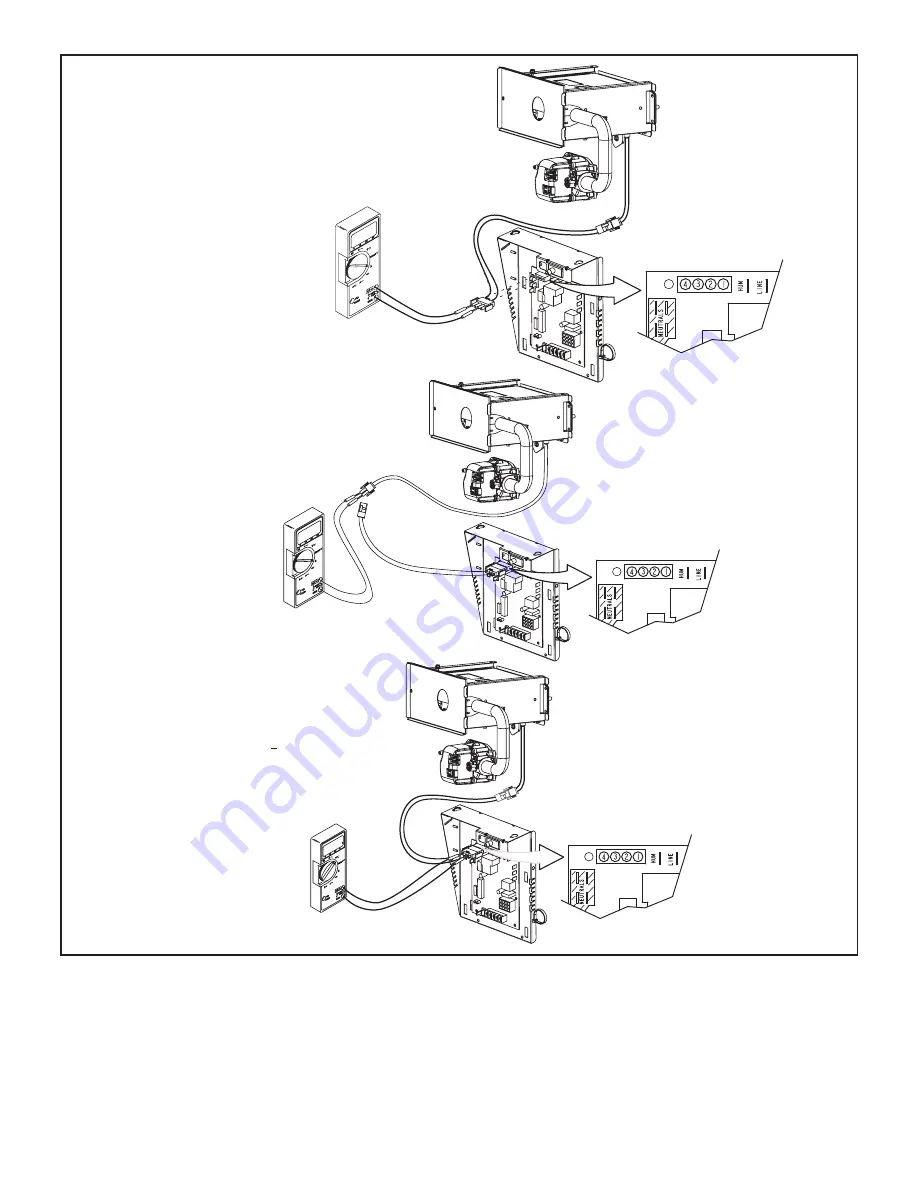
Page 14
Test 1
Check ignitor circuit for correct resistance
.
Remove 4-pin plug from control.
Check ohms reading across terminals 2 and 4.
Reading should be between 39 and 70 ohms. If
value is correct, this is the only test needed.
If the reading on the meter is not correct, (0 or
infinity) then a second test is needed.
Test 2
Check ignitor for correct resistance
.
Seperate the 2-pin jack-plug near the manifold and check
resistance of ignitor at the plug. Reading should be
between 39 and 70 ohms. If the reading is correct, then
the problem is with the wiring between the jack-plug and
the control. If reading is not correct, the issue is the ignitor.
Test 3
Check ignitor for correct voltage
Insert meter probes into terminals 2 and 4 (use small
diameter probes in order not to damage plug).
Check voltage during 20 second ignitor warm up period.
Voltage should read 120 volts + 10%. If voltage reads below
these values, check for correct supply voltage to furnace.
Multi−Meter
(set to ohms)
Multi−Meter
(set to ohms)
Multi−Meter
(set to VAC)
FIGURE 10