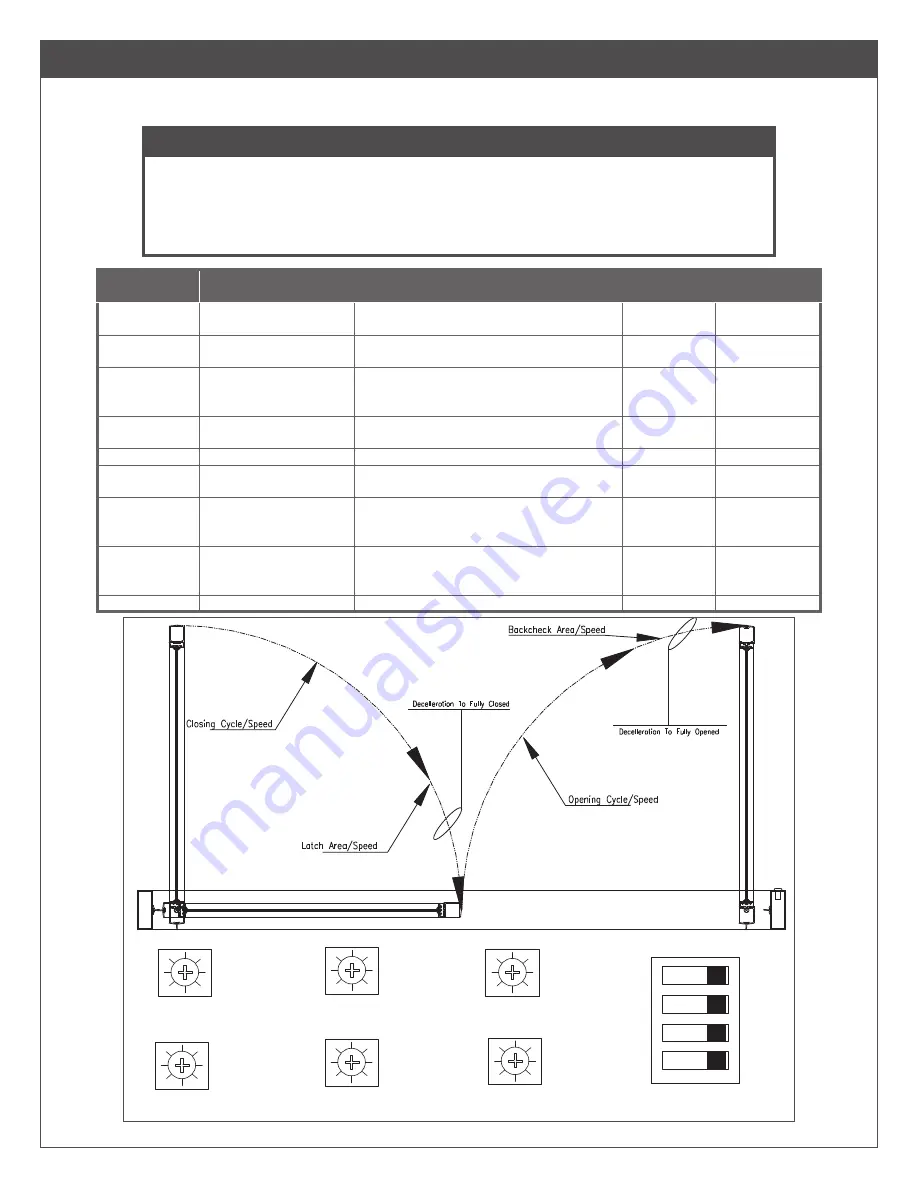
10
6
Operator Adjustment
See table below and diagrams (page 16) for operator feature adjustment.
After adjusting, cycle the door several times to check for proper operation. Then continue with step 4k on page 9.
notE
adjust operator for the SLoWESt operation practical, in accordance with the latest revisions of
the americans with Disabilities act (aDa); anSi/BHMa a156.19 Standards for Power-assisted
and Low Energy Power-operated Doors; and local codes.
opening Speed: 5 seconds or more
Closing Speed: 3 seconds or more
Latch Location: 10 degrees or more
Latch Speed: 1.5 seconds or more
Features
Control
Description
Counter
Clockwise
Clockwise
Opening
Speed
Opening Speed
Controls opening speed of door
Slower
Faster
Back Check
Speed
Back Check Speed
Controls the speed of the door near the full
open position to prevent door slamming
Slower
Faster
Hold Open
Time Delay
Hold Open Time Delay
Controls the length of time the door
remains in the full open position: 1 sec to
15 sec
Less Time
Down to 1
sec
More Time Up
to 15 sec
Back Check
Position
Back Check Position
Door position where back check speed
engages
Less Latch
More Latch
Closing Speed Closing Speed
Controls closing speed of door
Slower
Faster
Delayed
Activation
DLY (SW1)
Delays opening of door for strike
applications (1 second delay)
Push and Go
PNG (SW2)
ON: Pushing the door open 5° causes
operator to open door for remainder of
open cycle
Power Boost
On or Off
PB (SW3)
ON: 3-second power boost enabled:
applies additional force to close door—
used for high wind situations
SW4
Not used
- +
Less More
Backcheck
Position
Latch
Position
More
Less
+
-
- +
Less More
Open
Speed
Time Delay
More
Less
+
-
Backcheck
Speed
More
Less
+
-
- +
Less More
Close
Speed
OFF
ON
4
PB
PNG
DLY