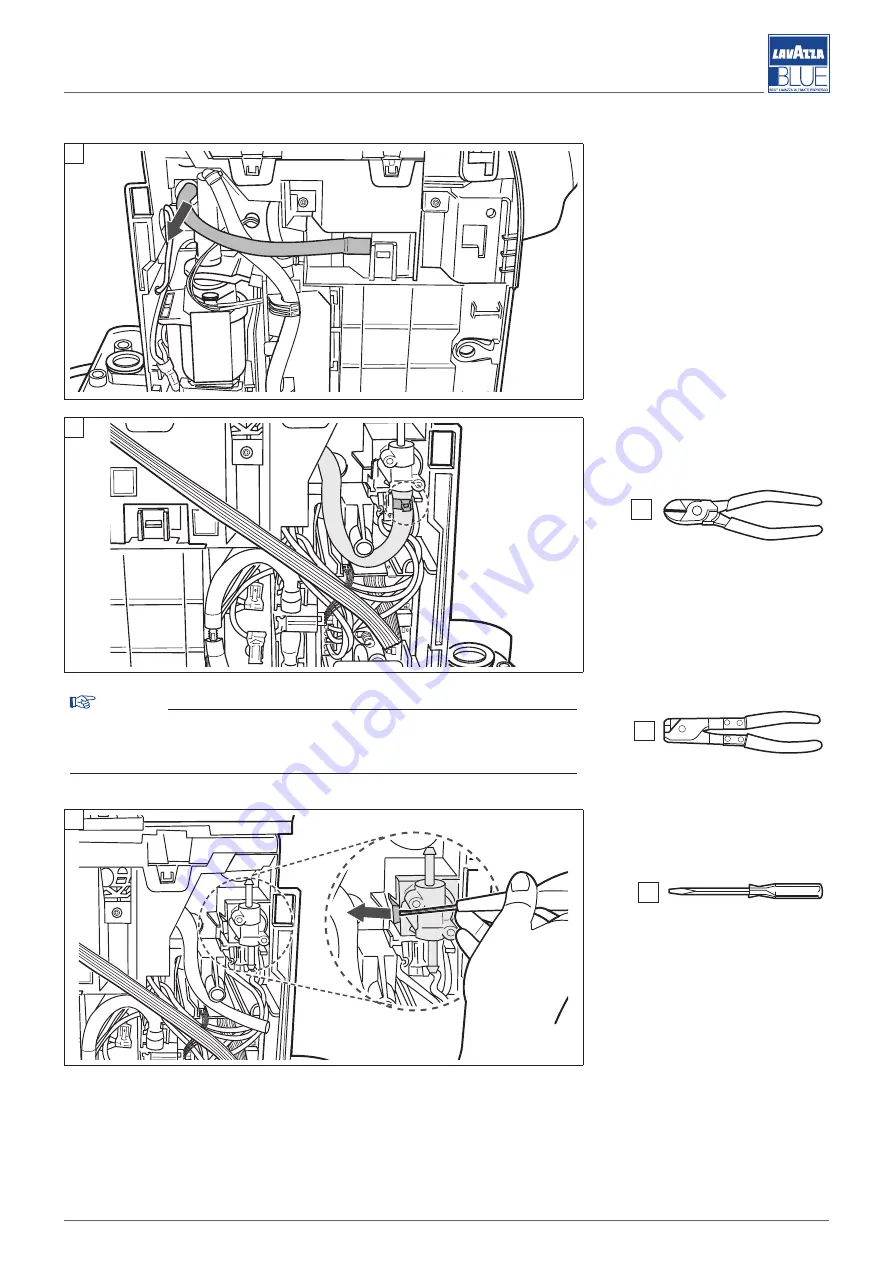
Technical support maintenance manual
Rel. 0.00 / June 2018
21
13.2. REMOVING THE 2-WAY SOLENOID VALVE
Figura A
: disconnect the dis-
charge hose on the other side of
the machine.
Figura B
: cut the high pressure
SILICON HOSE clamp and re-
move the hose.
Warning
Take care not to tear the hose.
During reassembly, the clamp must be replaced and tightened with the
OETIKER pliers.
Figure C
: pry on the locking lever
and push the solenoid valve out-
ward.
D
A
B
G
G
H
C