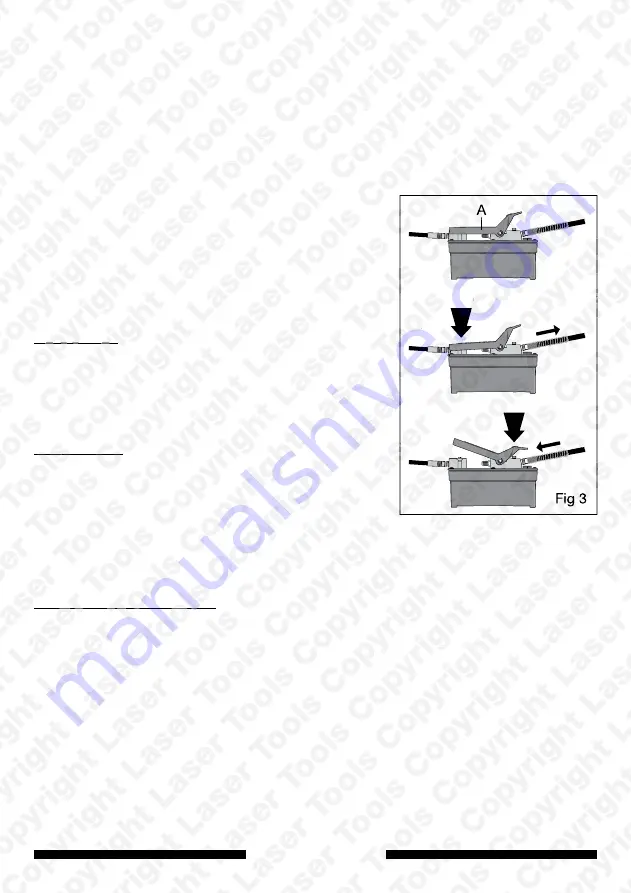
3
www.lasertools.co.uk
Specifications:
Usable oil capacity:
1500cc
Maximum hydraulic pressure:
700 bar
Output Flow Rate (no load):
0 bar:
1.3 litres/min
700 bar:
0.24 litres/min
Hydraulic hose length:
1.8m
Air pressure range:
7-11kg/cm² (100-156psi)
an automatic air line oiler as close to the hydraulic pump as possible. Set the oiler to feed
approximately one drop of oil per minute into the system. Use a high quality air line oil or SAE
10 oil. Otherwise add a few drops of the recommended oil to the air inlet port
(B)
weekly,
then operate the pump.
Connect the workshop air supply to the hydraulic pump. Minimum air pressure should be
100psi; the air supply should be filtered, regulated and lubricated.
Refer to Figure 1:
Connect the hydraulic coupling
(D)
to the corresponding coupling on the
cylinder/attachment. Ensure that both couplings are completely clean so that no dirt can
enter the system.
Refer to Figure 3:
depressing the foot pedal
(A)
at the
air inlet end (marked PUMP) activates the ram on the
cylinder/attachment. To activate the ram a small distance,
tap the foot pedal until the ram reaches the desired
distance. Retracting the ram (releasing the hydraulic
pressure) is carried out by depressing the foot pedal
(A)
at the opposite end (marked RELEASE).
Maintenance:
The greatest single cause of failure in hydraulic pumps is
dirt ingress. Keep the pump, hydraulic oil lines, cylinder,
attachments and accessories clean and free from oil and
dirt. Ensure that any unused couplers or adaptors are
sealed with thread protectors, and dust covers.
Filling with oil:
Check the fluid level after every 10 hours of use.
Drain and replenish the recommended hydraulic fluid
after approximately 300 hours of use.
Ensure cylinder on cylinder/attachment is fully retracted. Place pump in an upright position
with cylinder/attachment lower. Remove oil reservoir filler cap
(G)
. Top up with hydraulic oil
only - do not use engine oil or brake fluid. The oil level is correct at 12.7mm (1/2") below the
vented cap with all cylinders retracted.
Bleeding air from the system:
After filling, or after prolonged use, air may have accumulated within the hydraulic system.
To remove the air, connect to a cylinder/attachment and run the system through several
cycles (extending and retracting the cylinder) free of any load. The cylinder/attachment must
be at a lower level that the pump to allow air to be released through the pump oil reservoir.
an automatic air line oiler as close to the hydraulic pump as possible. Set the oiler to feed
10 oil. Otherwise add a few drops of the recommended oil to the air inlet port
then operate the pump.
10 oil. Otherwise add a few drops of the recommended oil to the air inlet port
approximately one drop of oil per minute into the system. Use a high quality air line oil or SAE
10 oil. Otherwise add a few drops of the recommended oil to the air inlet port
an automatic air line oiler as close to the hydraulic pump as possible. Set the oiler to feed
an automatic air line oiler as close to the hydraulic pump as possible. Set the oiler to feed
Refer to Figure 1:
Connect the workshop air supply to the hydraulic pump. Minimum air pressure should be
100psi; the air supply should be filtered, regulated and lubricated.
Connect the workshop air supply to the hydraulic pump. Minimum air pressure should be
100psi; the air supply should be filtered, regulated and lubricated.
then operate the pump.
Connect the workshop air supply to the hydraulic pump. Minimum air pressure should be
10 oil. Otherwise add a few drops of the recommended oil to the air inlet port
then operate the pump.
approximately one drop of oil per minute into the system. Use a high quality air line oil or SAE
10 oil. Otherwise add a few drops of the recommended oil to the air inlet port
approximately one drop of oil per minute into the system. Use a high quality air line oil or SAE
10 oil. Otherwise add a few drops of the recommended oil to the air inlet port
an automatic air line oiler as close to the hydraulic pump as possible. Set the oiler to feed
approximately one drop of oil per minute into the system. Use a high quality air line oil or SAE
an automatic air line oiler as close to the hydraulic pump as possible. Set the oiler to feed
enter the system.
Refer to Figure 3:
cylinder/attachment. Ensure that both couplings are completely clean so that no dirt can
enter the system.
Refer to Figure 1:
cylinder/attachment. Ensure that both couplings are completely clean so that no dirt can
Refer to Figure 1:
cylinder/attachment. Ensure that both couplings are completely clean so that no dirt can
100psi; the air supply should be filtered, regulated and lubricated.
Refer to Figure 1:
Connect the workshop air supply to the hydraulic pump. Minimum air pressure should be
100psi; the air supply should be filtered, regulated and lubricated.
Connect the workshop air supply to the hydraulic pump. Minimum air pressure should be
100psi; the air supply should be filtered, regulated and lubricated.
then operate the pump.
10 oil. Otherwise add a few drops of the recommended oil to the air inlet port
then operate the pump.
approximately one drop of oil per minute into the system. Use a high quality air line oil or SAE
10 oil. Otherwise add a few drops of the recommended oil to the air inlet port
approximately one drop of oil per minute into the system. Use a high quality air line oil or SAE
10 oil. Otherwise add a few drops of the recommended oil to the air inlet port
an automatic air line oiler as close to the hydraulic pump as possible. Set the oiler to feed
approximately one drop of oil per minute into the system. Use a high quality air line oil or SAE
an automatic air line oiler as close to the hydraulic pump as possible. Set the oiler to feed
cylinder/attachment. To activate the ram a small distance,
tap the foot pedal until the ram reaches the desired
air inlet end (marked PUMP) activates the ram on the
cylinder/attachment. To activate the ram a small distance,
tap the foot pedal until the ram reaches the desired
Refer to Figure 3:
air inlet end (marked PUMP) activates the ram on the
cylinder/attachment. To activate the ram a small distance,
Refer to Figure 3:
air inlet end (marked PUMP) activates the ram on the
enter the system.
Refer to Figure 3:
cylinder/attachment. Ensure that both couplings are completely clean so that no dirt can
enter the system.
Refer to Figure 1:
cylinder/attachment. Ensure that both couplings are completely clean so that no dirt can
Refer to Figure 1:
cylinder/attachment. Ensure that both couplings are completely clean so that no dirt can
100psi; the air supply should be filtered, regulated and lubricated.
Connect the hydraulic coupling
Connect the workshop air supply to the hydraulic pump. Minimum air pressure should be
100psi; the air supply should be filtered, regulated and lubricated.
Connect the workshop air supply to the hydraulic pump. Minimum air pressure should be
Connect the workshop air supply to the hydraulic pump. Minimum air pressure should be
10 oil. Otherwise add a few drops of the recommended oil to the air inlet port
10 oil. Otherwise add a few drops of the recommended oil to the air inlet port
an automatic air line oiler as close to the hydraulic pump as possible. Set the oiler to feed
approximately one drop of oil per minute into the system. Use a high quality air line oil or SAE
an automatic air line oiler as close to the hydraulic pump as possible. Set the oiler to feed
an automatic air line oiler as close to the hydraulic pump as possible. Set the oiler to feed
at the opposite end (marked RELEASE).
pressure) is carried out by depressing the foot pedal
at the opposite end (marked RELEASE).
distance. Retracting the ram (releasing the hydraulic
pressure) is carried out by depressing the foot pedal
distance. Retracting the ram (releasing the hydraulic
distance. Retracting the ram (releasing the hydraulic
pressure) is carried out by depressing the foot pedal
tap the foot pedal until the ram reaches the desired
distance. Retracting the ram (releasing the hydraulic
cylinder/attachment. To activate the ram a small distance,
tap the foot pedal until the ram reaches the desired
air inlet end (marked PUMP) activates the ram on the
cylinder/attachment. To activate the ram a small distance,
Refer to Figure 3:
air inlet end (marked PUMP) activates the ram on the
Refer to Figure 3:
depressing the foot pedal
depressing the foot pedal
cylinder/attachment. Ensure that both couplings are completely clean so that no dirt can
Connect the hydraulic coupling
cylinder/attachment. Ensure that both couplings are completely clean so that no dirt can
100psi; the air supply should be filtered, regulated and lubricated.
Connect the hydraulic coupling
100psi; the air supply should be filtered, regulated and lubricated.
Connect the hydraulic coupling
Connect the workshop air supply to the hydraulic pump. Minimum air pressure should be
100psi; the air supply should be filtered, regulated and lubricated.
Connect the workshop air supply to the hydraulic pump. Minimum air pressure should be
Connect the workshop air supply to the hydraulic pump. Minimum air pressure should be
10 oil. Otherwise add a few drops of the recommended oil to the air inlet port
approximately one drop of oil per minute into the system. Use a high quality air line oil or SAE
10 oil. Otherwise add a few drops of the recommended oil to the air inlet port
an automatic air line oiler as close to the hydraulic pump as possible. Set the oiler to feed
approximately one drop of oil per minute into the system. Use a high quality air line oil or SAE
10 oil. Otherwise add a few drops of the recommended oil to the air inlet port
an automatic air line oiler as close to the hydraulic pump as possible. Set the oiler to feed
approximately one drop of oil per minute into the system. Use a high quality air line oil or SAE
an automatic air line oiler as close to the hydraulic pump as possible. Set the oiler to feed
dirt ingress. Keep the pump, hydraulic oil lines, cylinder,
The greatest single cause of failure in hydraulic pumps is
Maintenance:
The greatest single cause of failure in hydraulic pumps is
at the opposite end (marked RELEASE).
Maintenance:
at the opposite end (marked RELEASE).
pressure) is carried out by depressing the foot pedal
pressure) is carried out by depressing the foot pedal
at the opposite end (marked RELEASE).
pressure) is carried out by depressing the foot pedal
at the opposite end (marked RELEASE).
distance. Retracting the ram (releasing the hydraulic
pressure) is carried out by depressing the foot pedal
tap the foot pedal until the ram reaches the desired
distance. Retracting the ram (releasing the hydraulic
cylinder/attachment. To activate the ram a small distance,
tap the foot pedal until the ram reaches the desired
air inlet end (marked PUMP) activates the ram on the
cylinder/attachment. To activate the ram a small distance,
depressing the foot pedal
air inlet end (marked PUMP) activates the ram on the
depressing the foot pedal
depressing the foot pedal
cylinder/attachment. Ensure that both couplings are completely clean so that no dirt can
Connect the hydraulic coupling
cylinder/attachment. Ensure that both couplings are completely clean so that no dirt can
Connect the hydraulic coupling
100psi; the air supply should be filtered, regulated and lubricated.
Connect the hydraulic coupling
100psi; the air supply should be filtered, regulated and lubricated.
Connect the workshop air supply to the hydraulic pump. Minimum air pressure should be
10 oil. Otherwise add a few drops of the recommended oil to the air inlet port
approximately one drop of oil per minute into the system. Use a high quality air line oil or SAE
10 oil. Otherwise add a few drops of the recommended oil to the air inlet port
an automatic air line oiler as close to the hydraulic pump as possible. Set the oiler to feed
approximately one drop of oil per minute into the system. Use a high quality air line oil or SAE
an automatic air line oiler as close to the hydraulic pump as possible. Set the oiler to feed
an automatic air line oiler as close to the hydraulic pump as possible. Set the oiler to feed
approximately one drop of oil per minute into the system. Use a high quality air line oil or SAE
an automatic air line oiler as close to the hydraulic pump as possible. Set the oiler to feed
approximately one drop of oil per minute into the system. Use a high quality air line oil or SAE
an automatic air line oiler as close to the hydraulic pump as possible. Set the oiler to feed
sealed with thread protectors, and dust covers.
attachments and accessories clean and free from oil and
dirt. Ensure that any unused couplers or adaptors are
dirt ingress. Keep the pump, hydraulic oil lines, cylinder,
attachments and accessories clean and free from oil and
The greatest single cause of failure in hydraulic pumps is
dirt ingress. Keep the pump, hydraulic oil lines, cylinder,
attachments and accessories clean and free from oil and
The greatest single cause of failure in hydraulic pumps is
dirt ingress. Keep the pump, hydraulic oil lines, cylinder,
Maintenance:
The greatest single cause of failure in hydraulic pumps is
Maintenance:
Maintenance:
at the opposite end (marked RELEASE).
at the opposite end (marked RELEASE).
pressure) is carried out by depressing the foot pedal
at the opposite end (marked RELEASE).
distance. Retracting the ram (releasing the hydraulic
pressure) is carried out by depressing the foot pedal
tap the foot pedal until the ram reaches the desired
distance. Retracting the ram (releasing the hydraulic
cylinder/attachment. To activate the ram a small distance,
tap the foot pedal until the ram reaches the desired
air inlet end (marked PUMP) activates the ram on the
cylinder/attachment. To activate the ram a small distance,
depressing the foot pedal
air inlet end (marked PUMP) activates the ram on the
depressing the foot pedal
cylinder/attachment. Ensure that both couplings are completely clean so that no dirt can
Connect the hydraulic coupling
cylinder/attachment. Ensure that both couplings are completely clean so that no dirt can
Connect the hydraulic coupling
cylinder/attachment. Ensure that both couplings are completely clean so that no dirt can
100psi; the air supply should be filtered, regulated and lubricated.
Connect the workshop air supply to the hydraulic pump. Minimum air pressure should be
100psi; the air supply should be filtered, regulated and lubricated.
Connect the workshop air supply to the hydraulic pump. Minimum air pressure should be
100psi; the air supply should be filtered, regulated and lubricated.
Connect the workshop air supply to the hydraulic pump. Minimum air pressure should be
10 oil. Otherwise add a few drops of the recommended oil to the air inlet port
10 oil. Otherwise add a few drops of the recommended oil to the air inlet port
10 oil. Otherwise add a few drops of the recommended oil to the air inlet port
approximately one drop of oil per minute into the system. Use a high quality air line oil or SAE
10 oil. Otherwise add a few drops of the recommended oil to the air inlet port
an automatic air line oiler as close to the hydraulic pump as possible. Set the oiler to feed
approximately one drop of oil per minute into the system. Use a high quality air line oil or SAE
an automatic air line oiler as close to the hydraulic pump as possible. Set the oiler to feed
Check the fluid level after every 10 hours of use.
Drain and replenish the recommended hydraulic fluid
Filling with oil:
Filling with oil:
Check the fluid level after every 10 hours of use.
Filling with oil:
Filling with oil:
sealed with thread protectors, and dust covers.
dirt. Ensure that any unused couplers or adaptors are
sealed with thread protectors, and dust covers.
attachments and accessories clean and free from oil and
dirt. Ensure that any unused couplers or adaptors are
dirt ingress. Keep the pump, hydraulic oil lines, cylinder,
attachments and accessories clean and free from oil and
The greatest single cause of failure in hydraulic pumps is
dirt ingress. Keep the pump, hydraulic oil lines, cylinder,
The greatest single cause of failure in hydraulic pumps is
The greatest single cause of failure in hydraulic pumps is
dirt ingress. Keep the pump, hydraulic oil lines, cylinder,
The greatest single cause of failure in hydraulic pumps is
dirt ingress. Keep the pump, hydraulic oil lines, cylinder,
The greatest single cause of failure in hydraulic pumps is
at the opposite end (marked RELEASE).
pressure) is carried out by depressing the foot pedal
at the opposite end (marked RELEASE).
pressure) is carried out by depressing the foot pedal
at the opposite end (marked RELEASE).
distance. Retracting the ram (releasing the hydraulic
pressure) is carried out by depressing the foot pedal
tap the foot pedal until the ram reaches the desired
distance. Retracting the ram (releasing the hydraulic
cylinder/attachment. To activate the ram a small distance,
tap the foot pedal until the ram reaches the desired
depressing the foot pedal
air inlet end (marked PUMP) activates the ram on the
cylinder/attachment. To activate the ram a small distance,
depressing the foot pedal
air inlet end (marked PUMP) activates the ram on the
depressing the foot pedal
(A)
(A)
Connect the hydraulic coupling
(D)
cylinder/attachment. Ensure that both couplings are completely clean so that no dirt can
(D)
to the corresponding coupling on the
100psi; the air supply should be filtered, regulated and lubricated.
to the corresponding coupling on the
Connect the workshop air supply to the hydraulic pump. Minimum air pressure should be
100psi; the air supply should be filtered, regulated and lubricated.
Connect the workshop air supply to the hydraulic pump. Minimum air pressure should be
Connect the workshop air supply to the hydraulic pump. Minimum air pressure should be
10 oil. Otherwise add a few drops of the recommended oil to the air inlet port
approximately one drop of oil per minute into the system. Use a high quality air line oil or SAE
10 oil. Otherwise add a few drops of the recommended oil to the air inlet port
an automatic air line oiler as close to the hydraulic pump as possible. Set the oiler to feed
approximately one drop of oil per minute into the system. Use a high quality air line oil or SAE
an automatic air line oiler as close to the hydraulic pump as possible. Set the oiler to feed
Ensure cylinder on cylinder/attachment is fully retracted. Place pump in an upright position
after approximately 300 hours of use.
Ensure cylinder on cylinder/attachment is fully retracted. Place pump in an upright position
Drain and replenish the recommended hydraulic fluid
after approximately 300 hours of use.
Drain and replenish the recommended hydraulic fluid
after approximately 300 hours of use.
Check the fluid level after every 10 hours of use.
Drain and replenish the recommended hydraulic fluid
Filling with oil:
Filling with oil:
Check the fluid level after every 10 hours of use.
Filling with oil:
sealed with thread protectors, and dust covers.
dirt. Ensure that any unused couplers or adaptors are
sealed with thread protectors, and dust covers.
attachments and accessories clean and free from oil and
dirt. Ensure that any unused couplers or adaptors are
attachments and accessories clean and free from oil and
attachments and accessories clean and free from oil and
dirt. Ensure that any unused couplers or adaptors are
dirt ingress. Keep the pump, hydraulic oil lines, cylinder,
attachments and accessories clean and free from oil and
The greatest single cause of failure in hydraulic pumps is
dirt ingress. Keep the pump, hydraulic oil lines, cylinder,
The greatest single cause of failure in hydraulic pumps is
at the opposite end (marked RELEASE).
pressure) is carried out by depressing the foot pedal
at the opposite end (marked RELEASE).
pressure) is carried out by depressing the foot pedal
at the opposite end (marked RELEASE).
distance. Retracting the ram (releasing the hydraulic
pressure) is carried out by depressing the foot pedal
cylinder/attachment. To activate the ram a small distance,
tap the foot pedal until the ram reaches the desired
distance. Retracting the ram (releasing the hydraulic
cylinder/attachment. To activate the ram a small distance,
tap the foot pedal until the ram reaches the desired
air inlet end (marked PUMP) activates the ram on the
cylinder/attachment. To activate the ram a small distance,
at the
air inlet end (marked PUMP) activates the ram on the
at the
air inlet end (marked PUMP) activates the ram on the
cylinder/attachment. Ensure that both couplings are completely clean so that no dirt can
to the corresponding coupling on the
cylinder/attachment. Ensure that both couplings are completely clean so that no dirt can
to the corresponding coupling on the
cylinder/attachment. Ensure that both couplings are completely clean so that no dirt can
100psi; the air supply should be filtered, regulated and lubricated.
to the corresponding coupling on the
Connect the workshop air supply to the hydraulic pump. Minimum air pressure should be
100psi; the air supply should be filtered, regulated and lubricated.
Connect the workshop air supply to the hydraulic pump. Minimum air pressure should be
Connect the workshop air supply to the hydraulic pump. Minimum air pressure should be
10 oil. Otherwise add a few drops of the recommended oil to the air inlet port
(B)
approximately one drop of oil per minute into the system. Use a high quality air line oil or SAE
(B)
an automatic air line oiler as close to the hydraulic pump as possible. Set the oiler to feed
approximately one drop of oil per minute into the system. Use a high quality air line oil or SAE
an automatic air line oiler as close to the hydraulic pump as possible. Set the oiler to feed
vented cap with all cylinders retracted.
Bleeding air from the system:
only - do not use engine oil or brake fluid. The oil level is correct at 12.7mm (1/2") below the
vented cap with all cylinders retracted.
with cylinder/attachment lower. Remove oil reservoir filler cap
only - do not use engine oil or brake fluid. The oil level is correct at 12.7mm (1/2") below the
Ensure cylinder on cylinder/attachment is fully retracted. Place pump in an upright position
with cylinder/attachment lower. Remove oil reservoir filler cap
Ensure cylinder on cylinder/attachment is fully retracted. Place pump in an upright position
with cylinder/attachment lower. Remove oil reservoir filler cap
after approximately 300 hours of use.
Ensure cylinder on cylinder/attachment is fully retracted. Place pump in an upright position
after approximately 300 hours of use.
Check the fluid level after every 10 hours of use.
Drain and replenish the recommended hydraulic fluid
Check the fluid level after every 10 hours of use.
Check the fluid level after every 10 hours of use.
sealed with thread protectors, and dust covers.
sealed with thread protectors, and dust covers.
dirt. Ensure that any unused couplers or adaptors are
sealed with thread protectors, and dust covers.
dirt. Ensure that any unused couplers or adaptors are
sealed with thread protectors, and dust covers.
attachments and accessories clean and free from oil and
dirt. Ensure that any unused couplers or adaptors are
dirt ingress. Keep the pump, hydraulic oil lines, cylinder,
attachments and accessories clean and free from oil and
The greatest single cause of failure in hydraulic pumps is
dirt ingress. Keep the pump, hydraulic oil lines, cylinder,
The greatest single cause of failure in hydraulic pumps is
pressure) is carried out by depressing the foot pedal
distance. Retracting the ram (releasing the hydraulic
pressure) is carried out by depressing the foot pedal
distance. Retracting the ram (releasing the hydraulic
pressure) is carried out by depressing the foot pedal
cylinder/attachment. To activate the ram a small distance,
cylinder/attachment. To activate the ram a small distance,
cylinder/attachment. Ensure that both couplings are completely clean so that no dirt can
to the corresponding coupling on the
cylinder/attachment. Ensure that both couplings are completely clean so that no dirt can
to the corresponding coupling on the
to the corresponding coupling on the
cylinder/attachment. Ensure that both couplings are completely clean so that no dirt can
to the corresponding coupling on the
Connect the workshop air supply to the hydraulic pump. Minimum air pressure should be
Connect the workshop air supply to the hydraulic pump. Minimum air pressure should be
weekly,
approximately one drop of oil per minute into the system. Use a high quality air line oil or SAE
weekly,
an automatic air line oiler as close to the hydraulic pump as possible. Set the oiler to feed
approximately one drop of oil per minute into the system. Use a high quality air line oil or SAE
cycles (extending and retracting the cylinder) free of any load. The cylinder/attachment must
To remove the air, connect to a cylinder/attachment and run the system through several
cycles (extending and retracting the cylinder) free of any load. The cylinder/attachment must
After filling, or after prolonged use, air may have accumulated within the hydraulic system.
To remove the air, connect to a cylinder/attachment and run the system through several
Bleeding air from the system:
Bleeding air from the system:
After filling, or after prolonged use, air may have accumulated within the hydraulic system.
Bleeding air from the system:
Bleeding air from the system:
only - do not use engine oil or brake fluid. The oil level is correct at 12.7mm (1/2") below the
vented cap with all cylinders retracted.
only - do not use engine oil or brake fluid. The oil level is correct at 12.7mm (1/2") below the
vented cap with all cylinders retracted.
with cylinder/attachment lower. Remove oil reservoir filler cap
only - do not use engine oil or brake fluid. The oil level is correct at 12.7mm (1/2") below the
Ensure cylinder on cylinder/attachment is fully retracted. Place pump in an upright position
with cylinder/attachment lower. Remove oil reservoir filler cap
Ensure cylinder on cylinder/attachment is fully retracted. Place pump in an upright position
with cylinder/attachment lower. Remove oil reservoir filler cap
after approximately 300 hours of use.
Ensure cylinder on cylinder/attachment is fully retracted. Place pump in an upright position
Drain and replenish the recommended hydraulic fluid
after approximately 300 hours of use.
Check the fluid level after every 10 hours of use.
Drain and replenish the recommended hydraulic fluid
after approximately 300 hours of use.
Check the fluid level after every 10 hours of use.
Drain and replenish the recommended hydraulic fluid
Check the fluid level after every 10 hours of use.
sealed with thread protectors, and dust covers.
sealed with thread protectors, and dust covers.
dirt. Ensure that any unused couplers or adaptors are
sealed with thread protectors, and dust covers.
attachments and accessories clean and free from oil and
dirt. Ensure that any unused couplers or adaptors are
dirt ingress. Keep the pump, hydraulic oil lines, cylinder,
attachments and accessories clean and free from oil and
The greatest single cause of failure in hydraulic pumps is
dirt ingress. Keep the pump, hydraulic oil lines, cylinder,
The greatest single cause of failure in hydraulic pumps is
(A)
cylinder/attachment. Ensure that both couplings are completely clean so that no dirt can
cylinder/attachment. Ensure that both couplings are completely clean so that no dirt can
to the corresponding coupling on the
cylinder/attachment. Ensure that both couplings are completely clean so that no dirt can
to the corresponding coupling on the
Connect the workshop air supply to the hydraulic pump. Minimum air pressure should be
Connect the workshop air supply to the hydraulic pump. Minimum air pressure should be
Specifications:
Specifications:
be at a lower level that the pump to allow air to be released through the pump oil reservoir.
cycles (extending and retracting the cylinder) free of any load. The cylinder/attachment must
be at a lower level that the pump to allow air to be released through the pump oil reservoir.
cycles (extending and retracting the cylinder) free of any load. The cylinder/attachment must
be at a lower level that the pump to allow air to be released through the pump oil reservoir.
To remove the air, connect to a cylinder/attachment and run the system through several
cycles (extending and retracting the cylinder) free of any load. The cylinder/attachment must
After filling, or after prolonged use, air may have accumulated within the hydraulic system.
To remove the air, connect to a cylinder/attachment and run the system through several
Bleeding air from the system:
Bleeding air from the system:
After filling, or after prolonged use, air may have accumulated within the hydraulic system.
Bleeding air from the system:
Bleeding air from the system:
vented cap with all cylinders retracted.
only - do not use engine oil or brake fluid. The oil level is correct at 12.7mm (1/2") below the
vented cap with all cylinders retracted.
only - do not use engine oil or brake fluid. The oil level is correct at 12.7mm (1/2") below the
vented cap with all cylinders retracted.
Ensure cylinder on cylinder/attachment is fully retracted. Place pump in an upright position
with cylinder/attachment lower. Remove oil reservoir filler cap
Ensure cylinder on cylinder/attachment is fully retracted. Place pump in an upright position
after approximately 300 hours of use.
Ensure cylinder on cylinder/attachment is fully retracted. Place pump in an upright position
Drain and replenish the recommended hydraulic fluid
after approximately 300 hours of use.
Check the fluid level after every 10 hours of use.
Drain and replenish the recommended hydraulic fluid
Check the fluid level after every 10 hours of use.
Check the fluid level after every 10 hours of use.
Drain and replenish the recommended hydraulic fluid
Check the fluid level after every 10 hours of use.
Drain and replenish the recommended hydraulic fluid
Check the fluid level after every 10 hours of use.
sealed with thread protectors, and dust covers.
dirt. Ensure that any unused couplers or adaptors are
sealed with thread protectors, and dust covers.
dirt. Ensure that any unused couplers or adaptors are
attachments and accessories clean and free from oil and
dirt. Ensure that any unused couplers or adaptors are
dirt ingress. Keep the pump, hydraulic oil lines, cylinder,
attachments and accessories clean and free from oil and
The greatest single cause of failure in hydraulic pumps is
dirt ingress. Keep the pump, hydraulic oil lines, cylinder,
cylinder/attachment. Ensure that both couplings are completely clean so that no dirt can
to the corresponding coupling on the
Output Flow Rate (no load):
0 bar:
Maximum hydraulic pressure:
Output Flow Rate (no load):
Usable oil capacity:
Maximum hydraulic pressure:
Specifications:
Usable oil capacity:
Specifications:
Specifications:
be at a lower level that the pump to allow air to be released through the pump oil reservoir.
cycles (extending and retracting the cylinder) free of any load. The cylinder/attachment must
be at a lower level that the pump to allow air to be released through the pump oil reservoir.
cycles (extending and retracting the cylinder) free of any load. The cylinder/attachment must
be at a lower level that the pump to allow air to be released through the pump oil reservoir.
After filling, or after prolonged use, air may have accumulated within the hydraulic system.
To remove the air, connect to a cylinder/attachment and run the system through several
After filling, or after prolonged use, air may have accumulated within the hydraulic system.
To remove the air, connect to a cylinder/attachment and run the system through several
Bleeding air from the system:
Bleeding air from the system:
After filling, or after prolonged use, air may have accumulated within the hydraulic system.
Bleeding air from the system:
Bleeding air from the system:
vented cap with all cylinders retracted.
Bleeding air from the system:
only - do not use engine oil or brake fluid. The oil level is correct at 12.7mm (1/2") below the
vented cap with all cylinders retracted.
with cylinder/attachment lower. Remove oil reservoir filler cap
only - do not use engine oil or brake fluid. The oil level is correct at 12.7mm (1/2") below the
Ensure cylinder on cylinder/attachment is fully retracted. Place pump in an upright position
with cylinder/attachment lower. Remove oil reservoir filler cap
only - do not use engine oil or brake fluid. The oil level is correct at 12.7mm (1/2") below the
Ensure cylinder on cylinder/attachment is fully retracted. Place pump in an upright position
with cylinder/attachment lower. Remove oil reservoir filler cap
Ensure cylinder on cylinder/attachment is fully retracted. Place pump in an upright position
Drain and replenish the recommended hydraulic fluid
Check the fluid level after every 10 hours of use.
Drain and replenish the recommended hydraulic fluid
Check the fluid level after every 10 hours of use.
Hydraulic hose length:
Air pressure range:
700 bar:
Hydraulic hose length:
700 bar:
700 bar:
Hydraulic hose length:
0 bar:
700 bar:
Output Flow Rate (no load):
0 bar:
Output Flow Rate (no load):
Maximum hydraulic pressure:
Output Flow Rate (no load):
Usable oil capacity:
Maximum hydraulic pressure:
Usable oil capacity:
be at a lower level that the pump to allow air to be released through the pump oil reservoir.
cycles (extending and retracting the cylinder) free of any load. The cylinder/attachment must
be at a lower level that the pump to allow air to be released through the pump oil reservoir.
cycles (extending and retracting the cylinder) free of any load. The cylinder/attachment must
To remove the air, connect to a cylinder/attachment and run the system through several
cycles (extending and retracting the cylinder) free of any load. The cylinder/attachment must
After filling, or after prolonged use, air may have accumulated within the hydraulic system.
To remove the air, connect to a cylinder/attachment and run the system through several
After filling, or after prolonged use, air may have accumulated within the hydraulic system.
vented cap with all cylinders retracted.
vented cap with all cylinders retracted.
only - do not use engine oil or brake fluid. The oil level is correct at 12.7mm (1/2") below the
with cylinder/attachment lower. Remove oil reservoir filler cap
only - do not use engine oil or brake fluid. The oil level is correct at 12.7mm (1/2") below the
Ensure cylinder on cylinder/attachment is fully retracted. Place pump in an upright position
with cylinder/attachment lower. Remove oil reservoir filler cap
Ensure cylinder on cylinder/attachment is fully retracted. Place pump in an upright position
Ensure cylinder on cylinder/attachment is fully retracted. Place pump in an upright position
with cylinder/attachment lower. Remove oil reservoir filler cap
Ensure cylinder on cylinder/attachment is fully retracted. Place pump in an upright position
Drain and replenish the recommended hydraulic fluid
Air pressure range:
Hydraulic hose length:
Air pressure range:
Air pressure range:
Hydraulic hose length:
Air pressure range:
Hydraulic hose length:
Output Flow Rate (no load):
Output Flow Rate (no load):
Maximum hydraulic pressure:
Maximum hydraulic pressure:
be at a lower level that the pump to allow air to be released through the pump oil reservoir.
be at a lower level that the pump to allow air to be released through the pump oil reservoir.
cycles (extending and retracting the cylinder) free of any load. The cylinder/attachment must
be at a lower level that the pump to allow air to be released through the pump oil reservoir.
To remove the air, connect to a cylinder/attachment and run the system through several
cycles (extending and retracting the cylinder) free of any load. The cylinder/attachment must
To remove the air, connect to a cylinder/attachment and run the system through several
cycles (extending and retracting the cylinder) free of any load. The cylinder/attachment must
After filling, or after prolonged use, air may have accumulated within the hydraulic system.
To remove the air, connect to a cylinder/attachment and run the system through several
After filling, or after prolonged use, air may have accumulated within the hydraulic system.
only - do not use engine oil or brake fluid. The oil level is correct at 12.7mm (1/2") below the
with cylinder/attachment lower. Remove oil reservoir filler cap
only - do not use engine oil or brake fluid. The oil level is correct at 12.7mm (1/2") below the
only - do not use engine oil or brake fluid. The oil level is correct at 12.7mm (1/2") below the
with cylinder/attachment lower. Remove oil reservoir filler cap
only - do not use engine oil or brake fluid. The oil level is correct at 12.7mm (1/2") below the
Ensure cylinder on cylinder/attachment is fully retracted. Place pump in an upright position
with cylinder/attachment lower. Remove oil reservoir filler cap
Ensure cylinder on cylinder/attachment is fully retracted. Place pump in an upright position
Air pressure range:
Air pressure range:
Hydraulic hose length:
Air pressure range:
Hydraulic hose length:
Output Flow Rate (no load):
Output Flow Rate (no load):
Maximum hydraulic pressure:
1500cc
be at a lower level that the pump to allow air to be released through the pump oil reservoir.
be at a lower level that the pump to allow air to be released through the pump oil reservoir.
To remove the air, connect to a cylinder/attachment and run the system through several
cycles (extending and retracting the cylinder) free of any load. The cylinder/attachment must
After filling, or after prolonged use, air may have accumulated within the hydraulic system.
To remove the air, connect to a cylinder/attachment and run the system through several
After filling, or after prolonged use, air may have accumulated within the hydraulic system.
To remove the air, connect to a cylinder/attachment and run the system through several
After filling, or after prolonged use, air may have accumulated within the hydraulic system.
only - do not use engine oil or brake fluid. The oil level is correct at 12.7mm (1/2") below the
with cylinder/attachment lower. Remove oil reservoir filler cap
only - do not use engine oil or brake fluid. The oil level is correct at 12.7mm (1/2") below the
Ensure cylinder on cylinder/attachment is fully retracted. Place pump in an upright position
(G)
. Top up with hydraulic oil
Ensure cylinder on cylinder/attachment is fully retracted. Place pump in an upright position
1.3 litres/min
700 bar
700 bar
1500cc
700 bar
be at a lower level that the pump to allow air to be released through the pump oil reservoir.
cycles (extending and retracting the cylinder) free of any load. The cylinder/attachment must
be at a lower level that the pump to allow air to be released through the pump oil reservoir.
To remove the air, connect to a cylinder/attachment and run the system through several
cycles (extending and retracting the cylinder) free of any load. The cylinder/attachment must
be at a lower level that the pump to allow air to be released through the pump oil reservoir.
After filling, or after prolonged use, air may have accumulated within the hydraulic system.
To remove the air, connect to a cylinder/attachment and run the system through several
cycles (extending and retracting the cylinder) free of any load. The cylinder/attachment must
After filling, or after prolonged use, air may have accumulated within the hydraulic system.
To remove the air, connect to a cylinder/attachment and run the system through several
After filling, or after prolonged use, air may have accumulated within the hydraulic system.
After filling, or after prolonged use, air may have accumulated within the hydraulic system.
only - do not use engine oil or brake fluid. The oil level is correct at 12.7mm (1/2") below the
. Top up with hydraulic oil
only - do not use engine oil or brake fluid. The oil level is correct at 12.7mm (1/2") below the
Ensure cylinder on cylinder/attachment is fully retracted. Place pump in an upright position
. Top up with hydraulic oil
Ensure cylinder on cylinder/attachment is fully retracted. Place pump in an upright position
7-11kg/cm² (100-156psi)
1.8m
7-11kg/cm² (100-156psi)
0.24 litres/min
1.8m
1.3 litres/min
0.24 litres/min
1.3 litres/min
be at a lower level that the pump to allow air to be released through the pump oil reservoir.
cycles (extending and retracting the cylinder) free of any load. The cylinder/attachment must
be at a lower level that the pump to allow air to be released through the pump oil reservoir.
To remove the air, connect to a cylinder/attachment and run the system through several
cycles (extending and retracting the cylinder) free of any load. The cylinder/attachment must
To remove the air, connect to a cylinder/attachment and run the system through several
To remove the air, connect to a cylinder/attachment and run the system through several
cycles (extending and retracting the cylinder) free of any load. The cylinder/attachment must
After filling, or after prolonged use, air may have accumulated within the hydraulic system.
To remove the air, connect to a cylinder/attachment and run the system through several
After filling, or after prolonged use, air may have accumulated within the hydraulic system.
only - do not use engine oil or brake fluid. The oil level is correct at 12.7mm (1/2") below the
only - do not use engine oil or brake fluid. The oil level is correct at 12.7mm (1/2") below the
. Top up with hydraulic oil
only - do not use engine oil or brake fluid. The oil level is correct at 12.7mm (1/2") below the
Ensure cylinder on cylinder/attachment is fully retracted. Place pump in an upright position
. Top up with hydraulic oil
Ensure cylinder on cylinder/attachment is fully retracted. Place pump in an upright position
www.lasertools.co.uk
www.lasertools.co.uk
www.lasertools.co.uk
www.lasertools.co.uk
7-11kg/cm² (100-156psi)
0.24 litres/min
0.24 litres/min
be at a lower level that the pump to allow air to be released through the pump oil reservoir.
cycles (extending and retracting the cylinder) free of any load. The cylinder/attachment must
be at a lower level that the pump to allow air to be released through the pump oil reservoir.
be at a lower level that the pump to allow air to be released through the pump oil reservoir.
cycles (extending and retracting the cylinder) free of any load. The cylinder/attachment must
be at a lower level that the pump to allow air to be released through the pump oil reservoir.
To remove the air, connect to a cylinder/attachment and run the system through several
cycles (extending and retracting the cylinder) free of any load. The cylinder/attachment must
After filling, or after prolonged use, air may have accumulated within the hydraulic system.
To remove the air, connect to a cylinder/attachment and run the system through several
After filling, or after prolonged use, air may have accumulated within the hydraulic system.
only - do not use engine oil or brake fluid. The oil level is correct at 12.7mm (1/2") below the
Ensure cylinder on cylinder/attachment is fully retracted. Place pump in an upright position
. Top up with hydraulic oil
www.lasertools.co.uk
www.lasertools.co.uk
www.lasertools.co.uk
www.lasertools.co.uk
7-11kg/cm² (100-156psi)
7-11kg/cm² (100-156psi)
7-11kg/cm² (100-156psi)
be at a lower level that the pump to allow air to be released through the pump oil reservoir.
cycles (extending and retracting the cylinder) free of any load. The cylinder/attachment must
be at a lower level that the pump to allow air to be released through the pump oil reservoir.
To remove the air, connect to a cylinder/attachment and run the system through several
cycles (extending and retracting the cylinder) free of any load. The cylinder/attachment must
After filling, or after prolonged use, air may have accumulated within the hydraulic system.
To remove the air, connect to a cylinder/attachment and run the system through several
After filling, or after prolonged use, air may have accumulated within the hydraulic system.
www.lasertools.co.uk
www.lasertools.co.uk
www.lasertools.co.uk
www.lasertools.co.uk
be at a lower level that the pump to allow air to be released through the pump oil reservoir.
cycles (extending and retracting the cylinder) free of any load. The cylinder/attachment must
be at a lower level that the pump to allow air to be released through the pump oil reservoir.
cycles (extending and retracting the cylinder) free of any load. The cylinder/attachment must
3