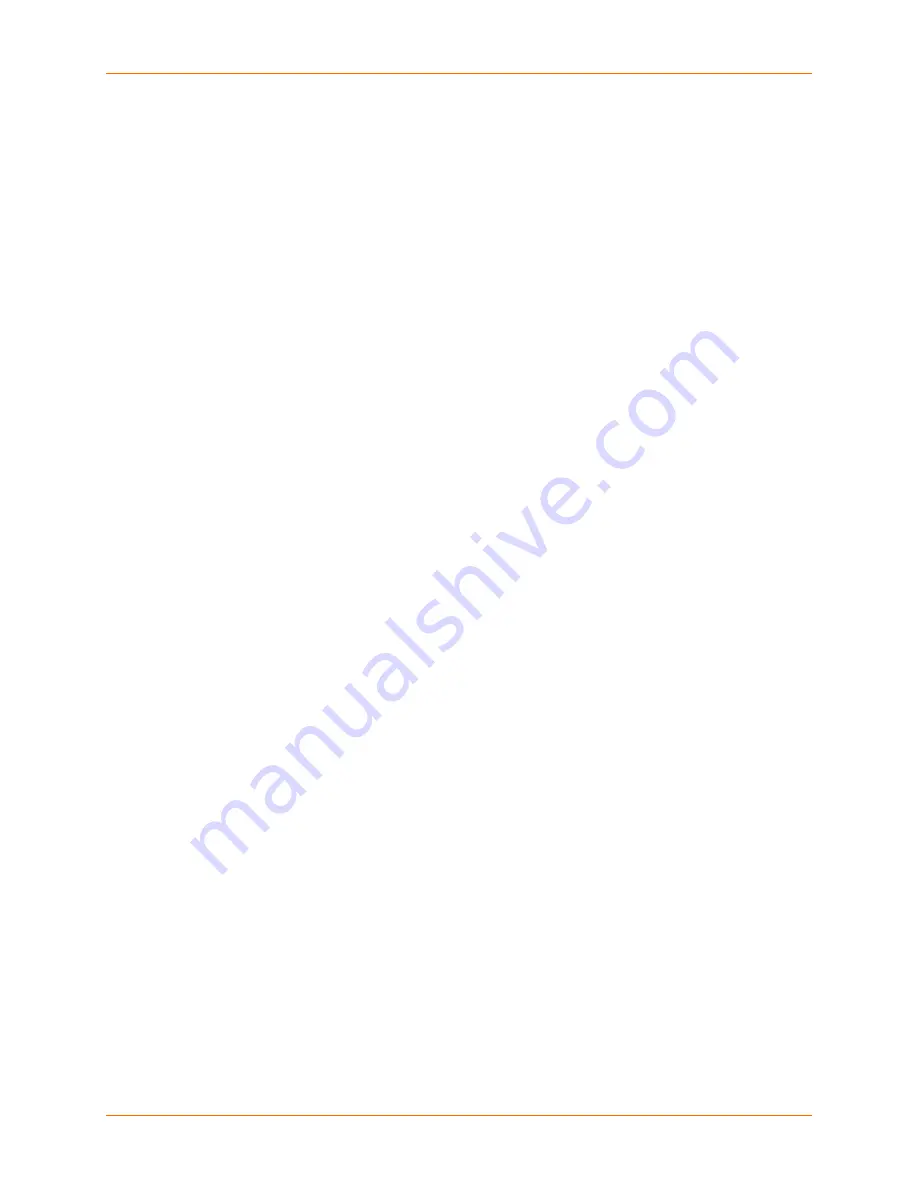
3: Mounting Instructions and PCB Footprint
xPico® 110 Embedded Device Server Integration Guide
26
(1) Solder paste alloy: SAC305(Sn96.5/Ag3.0/Cu0.5)(Lead free solder
paste is recommended by Lantronix.)
(2) A-B. Temp.(Pre-heat): 150~200 °C; soak time:60~120 seconds.
(3) C. Peak temp: <245 °C
(4) D. Time above 217 °C: 40~90 sec.
(5) Suggested optimal cooling rate is <1 °C /sec. from peak to 217 °C.
(6) Utilize a minimum of nine heater zones for Reflow equipment.
(7) Nitrogen usage is recommended when the oxygen concentration is
controlled at less than 1500 ppm.
Note:
Need to inspect solder joint by X-ray post reflow for voiding and
solder shorts.
MSD (Moisture Sensitive Device) Control for the Module
1. The xPico embedded device server is a moisture sensitive device; the MSL level is 3.
2. Modules to be subjected to reflow solder or other high temperature processes must be
mounted within 168 hours of opening the vacuum containment bag in factory conditions.
3. The module requires baking before mounting, if:
a. The Humidity Indicator Card reads >10% when read at 23± 5°C
b. The MSL3 are not met
4. If baking is required, optional condition as below (refer to IPC/JEDEC J-STD-033):
a. Bake 9 hours at 125°C (Tray base)
b. Bake 33 hours at 90°C/
≦
5%RH (Tray base)
c. Bake 13 days at 40°C/
≦
5%RH (Tape/Reel base)
Note:
After baking, the floor time of module should be recalculated. The xPico 110 device
server cannot be exposed to more than three reflow cycles.
The xPico 110 embedded device server is moisture sensitive and needs to be handled within
proper MSL 3 guidelines to avoid damage from moisture absorption. After the moisture barrier
bag (MBB) is opened, the part should go through reflow for board assembly within 48 hours at
factory conditions of <30°C/60% RH, or stored at <10% RH. If both of these conditions are not
met, baking is required before board mounting.
For removal from a customer PCB, the customer PCB must first be baked. Baking should be
done for a minimum of 8 hours at 125°C. It is recommended that during removal, localized
heating be used, and the maximum body temperature of device should not exceed 200°C.