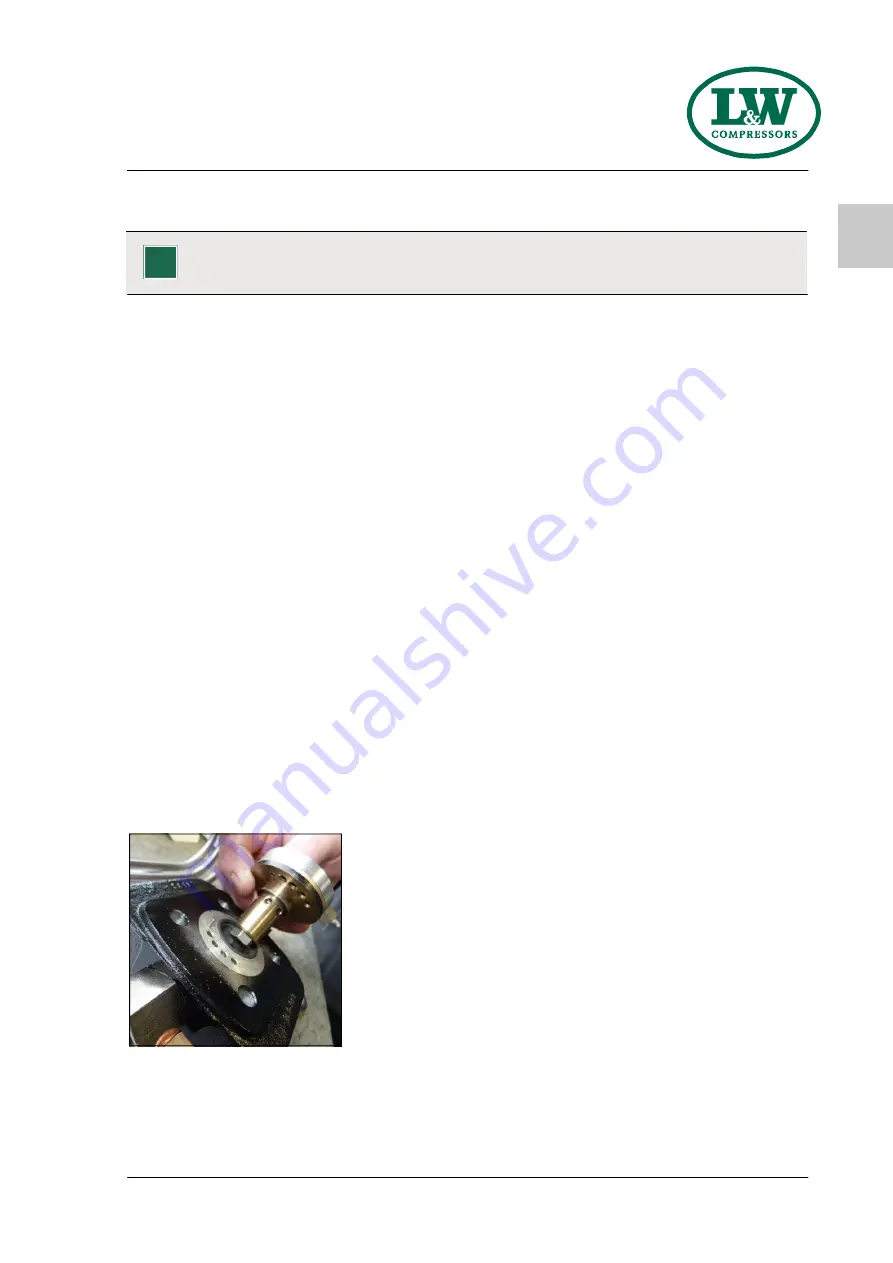
Seite A - 57
A
LW SC-180 ES / LW SC-250 ES
Version: 09.12.2022
M A I N T E N A N C E A N D S E R V I C E
Note
The figures of the parts can differ due to the different stages.
i
Replace inlet and outlet valve 2nd stage / 3rd stage
Replace the inlet and outlet valve 2nd stage as follows:
• Loosen pipe connections.
• Loosen valve head screws.
• Remove valve head Observe that the lower valve gasket is also pulled out. It can still stick inside
the cylinder head.
• Remove inlet / outlet valve.
• Check valve head if defective (check locating pin).
• Change upper valve gasket.
• Change lower valve gasket (aluminium gasket).
• Insert new inlet and outlet valve into the valve head (Fig. 1). CAUTION: Observe correct position
between valve centre hole and valve head locating pin.
• Place the valve head with the new inlet and outlet valve.
• Place pipe connections.
• Tighten valve head screws crosswise.
• Tighten pipe connections.
Inlet and outlet valves change 2nd stage / 3rd stage is now completed.
Fig. 1 - Ensure correct valve position
(centre pin)
Содержание SC-180 ES
Страница 3: ...A Operating Instructions Breathing Air Compressor LW SC 180 ES LW SC 250 ES Version 12 2022...
Страница 12: ...A S I C H E R H E I T S H I N W E I S E...
Страница 19: ...A I N S TA L L AT I O N...
Страница 21: ...Seite A 19 A LW SC 180 ES LW SC 250 ES Version 09 12 2022 I N S T A L L A T I O N Dimensions Fig Dimensions...
Страница 26: ...A O P E R AT I O N...
Страница 34: ...A R E M E D Y I N G FA U LT S...
Страница 39: ...A M A I N T E N A N C E A N D S E R V I C E...
Страница 65: ...A M A I N T E N A N C E R E C O R D S...
Страница 73: ...E A T T A C H M E N T Version 11 12 E...
Страница 77: ...INFORMATIONON THE SERVICE LIFE OF L W HIGH PRESSURE HOSES...
Страница 85: ...ANNEX...