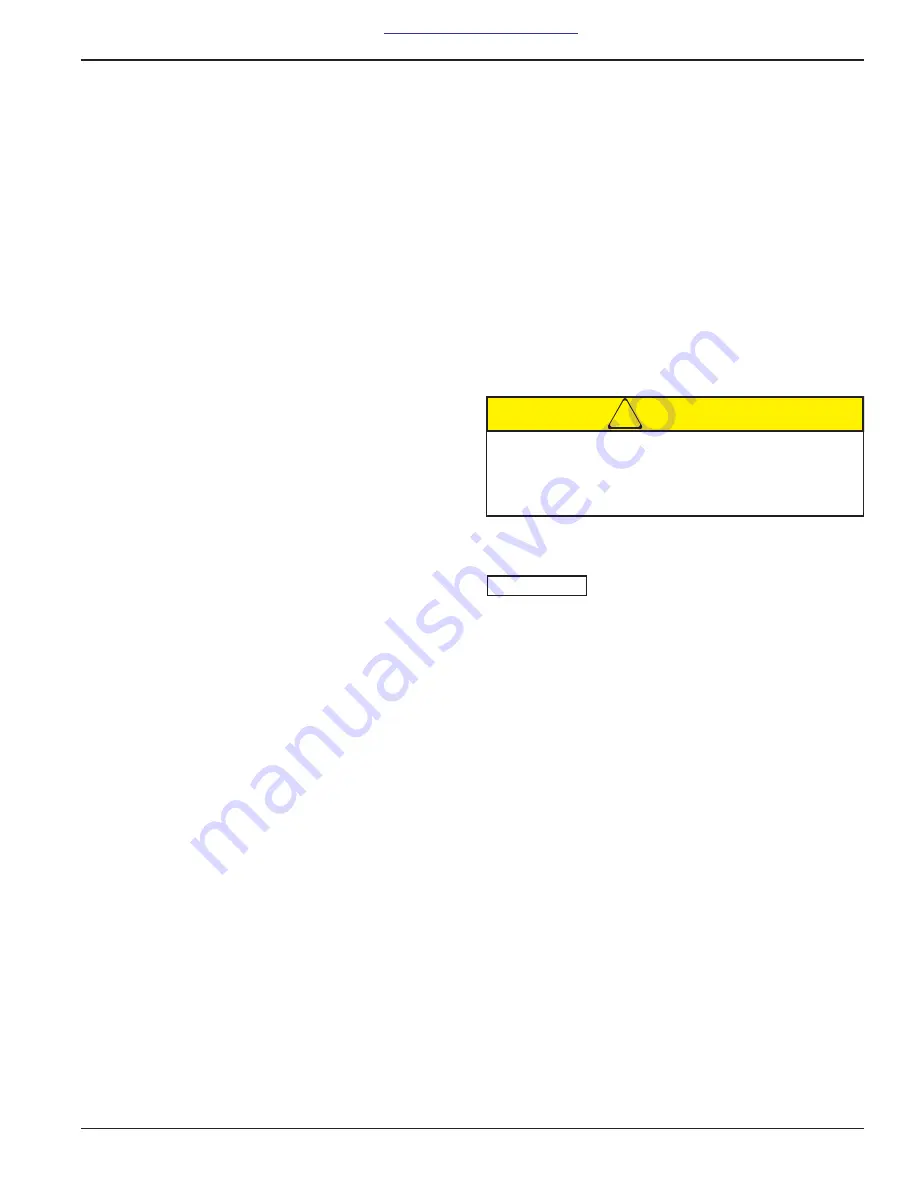
OPERATION AND MAINTENANCE
4-5
Field Operation - Three Point
Hitch Type
1.
Lower the In-Row Ripper to the ground and pull it a
few feet at the approximate desired depth.
2.
Check for front-to-rear levelness. Level the frame by
adjusting the three-point hitch top arm until the frame
is level relative to the ground.
3.
Set the depth by adjusting the gauge wheels. For
stability, it is important that the gauge wheels always
apply slight pressure against the soil. Adjust the
gauge wheels as follows:.
a.
Loosen the keeper nut on the adjustable top link.
b.
Shorten the top link to shallow up the ripper,
lengthen the link to allow the ripper to run
deeper.
c.
Snug up the top link keeper nut.
1.
Always lift the In- Row Ripper completely out of the
ground before turning or backing to prevent shank or
coulter damage or damage to their respective
mounting brackets.
2.
Reduce speed at field ends, raise the In-Row Ripper
out of the ground, and assist turning by using the
wheel brakes, if necessary.
3.
After a few hours of initial operation, check all cap
screws for tightness. Tighten any loose cap screws.
4.
Coulters should be adjusted to operate only deep
enough to be in firm soil and cut the residue.
Generally, the harder the soil, the less pressure
should be used on the coulters. Adjust the single
coulters by loosening the coulter mount U-bolts,
sliding the coulter up or down as needed. Re-tighten
the coulter mount making sure the coulter standard
tube is square with the ripper frame.
Wheel Bearing Maintenance
1.
Check wheel bearings and coulter bearings
occasionally for excessive end play. To correctly
replace the wheel bearings:
2.
Place the frame on blocks or stands sufficient to lift
the tire clear of the ground.
3.
Remove the hub cap, cotter pin, slotted nut, and
washer.
4.
Remove the hub. Clean and inspect the bearings and
hub cavity. Replace any worn or defective parts.
5.
Repack the bearings using a high-quality wheel
bearing grease.
6.
Replace the hub with a new seal and inner bearing in
place.
7.
Install the outer bearing cone, washer, and slotted
nut.
8.
Tighten the slotted nut while rotating the hub until
there is a slight resistance to wheel rotation. Back the
slotted nut off one notch until the wheel rotates freely
without end play.
9.
Install a new cotter pin and the hub cap.
10.
Wheel bearing maintenance should be performed at
the beginning of every season of use.
Coulter Spring Adjustment
No spring adjustment is necessary on the coulters. All
adjustments were made before shipping at the factory.
Initial operating force to move coulter upwards is 540
pounds. The preload has proved to be more than
adequate for most conditions.
CAUTION
Lubrication
IMPORTANT
Items with grease zerks are listed in the illustrated
parts book.
1.
Grease coulter hub and swivel mount casting after
twenty hours of use.
Storage
1.
The service life of the In-Row Ripper will be extended
by proper off-season storage practices. Before
storing, complete the following procedures:
2.
Completely clean the unit.
3.
Inspect the machine for worn or defective parts.
Replace parts as needed to avoid delays the
following season.
4.
Repaint all areas where the original paint film is worn
off.
5.
Grease all exposed metal surfaces of shanks, points,
and coulters.
6.
Lubricate as suggested in
7.
Store the unit in a shed or under a tarpaulin to protect
it from the weather. The ground tools and tires
should rest on a board or other device to keep them
out of the soil.
Any attempt to make coulter force greater than
factory setting may contribute to premature
failure of parts and warranty shall be null and
void.
Содержание 2512 Series
Страница 4: ...ii F 1040 0320 TABLE OF CONTENTS...
Страница 18: ...2 10 F 1040 0320 STANDARD SPECIFICATIONS TABLE OF CONTENTS 8 Shank Spacing...
Страница 29: ...ASSEMBLY INSTRUCTIONS 3 11 TABLE OF CONTENTS Figure 3 8 LED Light and SMV Bracket Installation...
Страница 32: ...3 14 F 1040 0320 ASSEMBLY INSTRUCTIONS TABLE OF CONTENTS...
Страница 38: ...4 6 F 1040 0320 OPERATION AND MAINTENANCE TABLE OF CONTENTS...
Страница 40: ...5 2 F 1040 0320 TROUBLESHOOTING GUIDE TABLE OF CONTENTS...