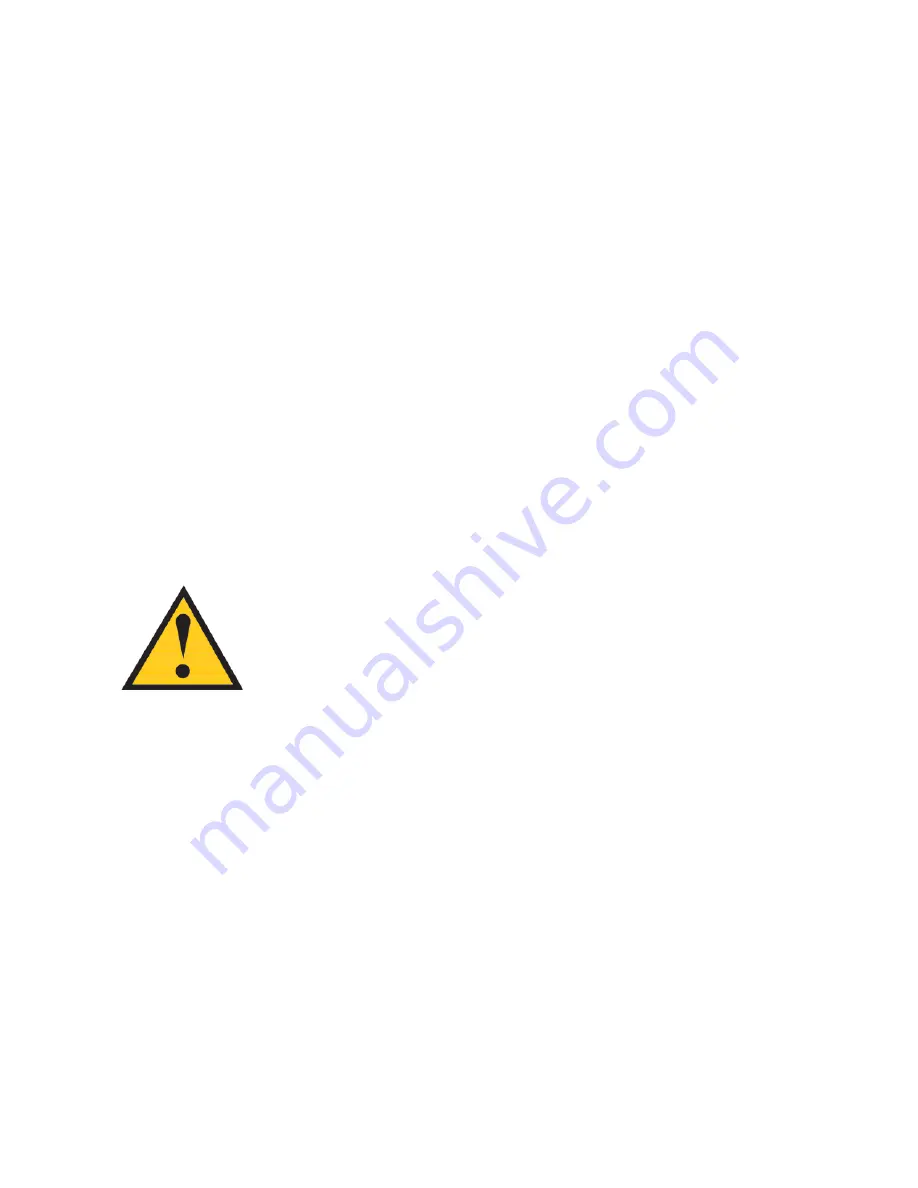
21
P.N. 28-0720/05
3.3
CLEANING AND SANITIZING BAG-IN-BOX (BIB) SYSTEMS
A. Disconnect syrup quick disconnect coupling from syrup packages and connect coupling to a bag
valve removed from an empty Bag-in-Box package.
B. Place end of syrup inlet line, with bag valve attached, in a clean container filled with clean,
potable, room-temperature water.
C. Place waste container under applicable dispensing valve. Activate valve until water is
dispensed. Flush and rinse line and fittings for a minimum of 60 seconds to remove all traces
of residual product.
NOTE:
Extended lengths of product lines may require additional time for flushing and rinsing lines.
D. Prepare cleaning solution as described in Section 3.2 above. Place end of syrup inlet line in
container filled with cleaning solution.
E. Place waste container under applicable dispensing valve. Activate valve and draw cleaning
solution through lines for a minimum of sixty seconds. This will ensure line is flushed and filled
with cleaning solution. Allow line to stand for at least thirty minutes.
F.
Place end of syrup inlet line in a clean container filled with clean, potable water at a
temperature of 90 to 110 degrees F.
G. Place waste container under applicable dispensing valve. Activate valve to flush and rinse line
and fittings for a minimum of sixty seconds to remove all traces of cleaning solution. Continue
rinsing until testing with phenolpthalein shows that the rinse water is free of residual detergent.
H. Prepare sanitizing solution as described in Section 3.2 above. Place end of syrup inlet line in
container filled with sanitizing solution which has been prepared.
I.
Activate valve and draw sanitizing solution through line for a minimum of sixty seconds. This
will ensure line is flushed and filled with sanitizing solution. Allow line to stand for at least
fifteen minutes.
J.
Remove bag valve from quick disconnect coupling and reconnect syrup inlet line to syrup
package. Ready unit for operation.
K. Draw drinks and refill lines with end product to flush sanitizing solution from the dispenser.
NOTE:
A fresh water rinse cannot follow sanitization of equipment. Purge only with the end use
product.
This is an NSF requirement.
L.
Test dispenser in the normal manner for proper operation. Taste dispensed product to ensure
there is no off-taste. If off-taste is found, flush syrup system again.
M. Repeat cleaning, rinsing, and sanitizing procedures for each valve circuit.
3.4
VALVES
A. Valves may be cleaned and sanitized (see preparation in Section 3.2) in the same manner.
1.
Remove cover and disconnect power so the valve will not be activated during the cleaning
procedure. Remove nozzle and diffuser. Wash these parts in cleaning solution, then
immerse them in a bath of sanitizing solution for 15 minutes.
2.
Visually inspect around nozzle area for syrup residue. This area may be cleaned with warm
water and cloth or with the nozzle brush supplied. Wipe off dispensing lever.
3.
Wearing sanitary gloves, remove, drain and air dry the nozzle and diffuser.
4.
Wearing sanitary gloves, replace diffuser, twist nozzle in place.
5
Connect power and replace cover. Valve is ready for operation.
WARNING!
Flush sanitizing solution completely from syrup systems. Residual sanitizing
solution creates a health hazard.