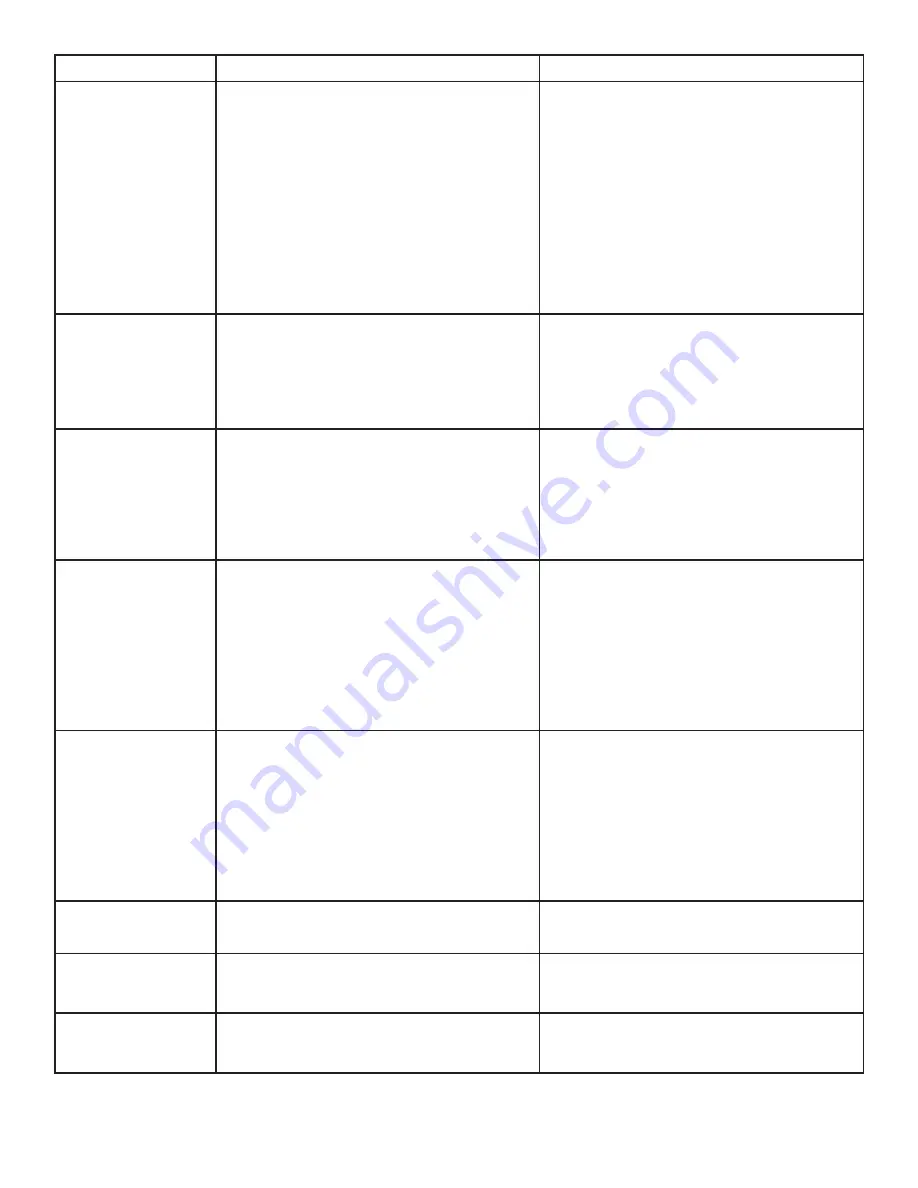
15
TROUBLE
CAUSE
REMEDY
Low or no carbonation.
1. Low or no CO
2
.
2. Low water pressure.
3. Worn or defective carbonator pump.
4. Backflow preventer not allowing water to flow.
5. Carbonator motor not running.
6. Carbonator motor running continuously.
1. Check CO
2
supply. Adjust CO
2
pressure to 90
PSI - 110 PSI (0.621 MPA - 0.758 MPA).
2. Need water booster kit.
3. Replace carbonator pump.
4. Replace backflow preventer noting the flow
direction arrow from pump to cold plate.
5. Check power supply. Ensure carbonator is
plugged in.
6. Check switch on carbonator. Check water in
check valve for blockage. Check carbonator
control. Check carbonator pump for efficiency.
Erratic ratio.
1. Incoming water and/or syrup supply not at
minimum flowing pressure.
2. Foreign debris in water and/or syrup flow
control.
3. CO
2
regulator malfunction.
1. Check pressure and adjust.
2. Remove flow control from suspected valve
and clean out any foreign material to ensure
smooth spool movement.
3. Repair or replace CO
2
regulator.
Insufficient soda flow
(carbonated drinks).
1. Insufficient CO
2
supply pressure.
2. Shutoff on mounting block is not fully open.
3. Foreign debris in soda flow control.
1. Verify incoming CO
2
pressure is between 90
PSI - 110 PSI (0.621 MPA - 0.758 MPA).
2. Open shutoff fully.
3. Remove soda flow control from valve and
clean out any foreign material to ensure
smooth spool movement.
Insufficient water flow
(plain water drinks).
1. Insufficient incoming supply pressure.
2. Shutoff on mounting block not fully open.
3. Foreign debris in water flow control.
4. Water filtration problem.
1. Verify incoming supply water pressure to plain
water inlet is a minimum of 40 PSI (0.276 MPA)
and a maximum of 80 PSI (0.552 MPA).
2. Open shutoff fully.
3. Remove water flow control from valve and
clean out any foreign material to ensure
smooth spool movement.
4. Service water system as required.
Insufficient syrup flow.
1. Insufficient CO
2
pressure to BIB pumps.
2. Shutoff on mounting block not fully open.
3. Foreign debris in syrup flow control.
4. Defective BIB pump.
1. Adjust CO
2
pressure to BIB pumps to 30 PSI
- 80 PSI (0.207 MPA - 0.552 MPA). Do not
exceed manufacturer’s recommendations.
2. Open shutoff fully.
3. Remove syrup flow control from valve and
clean out any foreign material to ensure
smooth spool movement.
4. Replace pump.
Water leakage around
nozzle.
1. Damaged O-ring on nozzle.
1. Replace nozzle.
Miscellaneous leakage.
1. Gap between parts.
2. Damaged or improperly installed O-rings.
1. Tighten appropriate retaining screws.
2. Replace or adjust appropriate O-rings.
Water continually leak-
ing at connections.
1. Loose water connections.
2. Flare seal washer leaks.
1. Tighten water connections.
2. Replace flare seal washer.