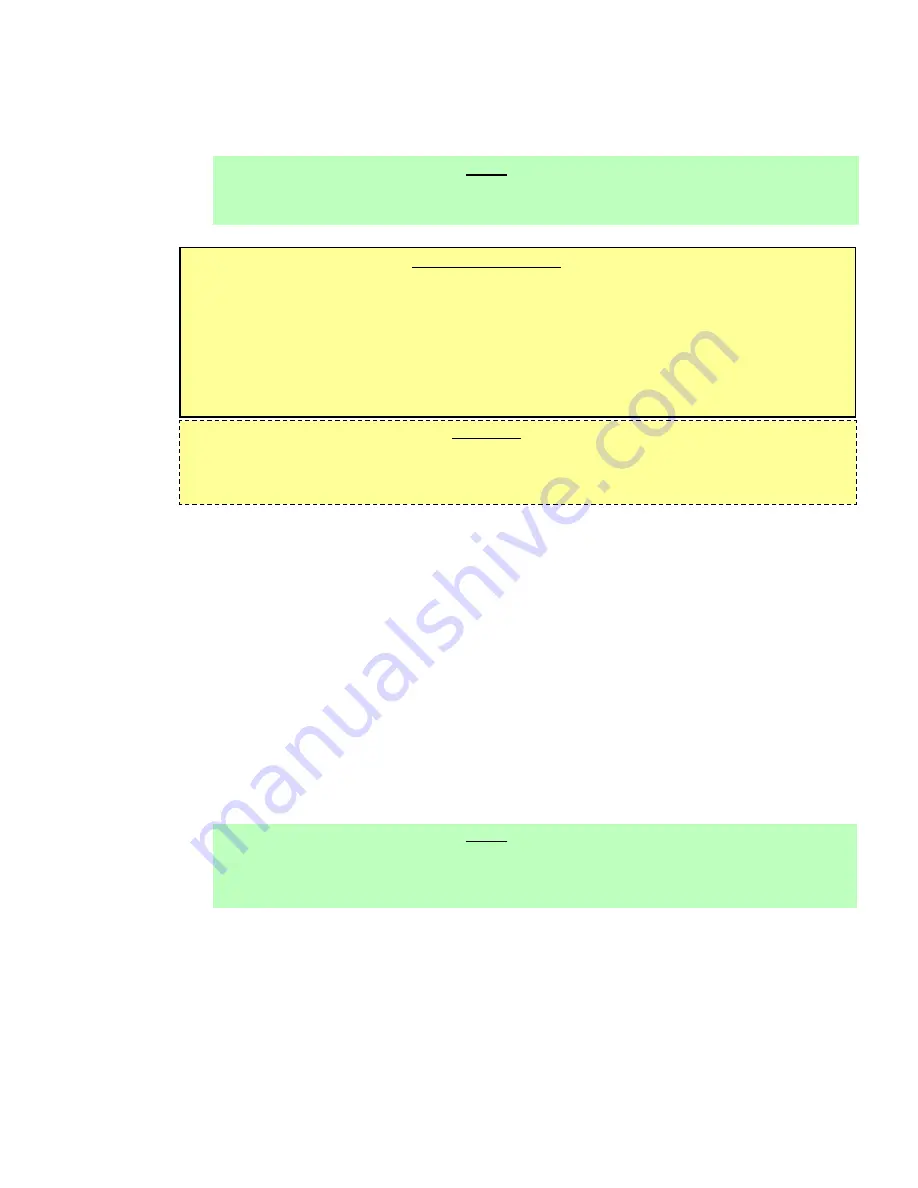
4
N. Clean and sanitize dispenser (see Section 2).
O. Fill unit approximately half full with ice. Push Chute and check for ice delivery.
P.
Fill unit with ice.
Q. Install Top Cover.
NOTE
Lancer does not recommend the use of shaved, flake, nugget, or pellet ice in dispensers not
properly equipped to do so
(see Section 6.2, this manual)
.
R. Set brix ratio for beverage dispensing valves according to manufacturer's instructions.
IMPORTANT NOTICE
WHEN INSTALLING AN ICEMAKER ON AN IBD UNIT, A BIN THERMOSTAT OR OTHER MEANS
OF CONTROLLING THE ICE LEVEL MUST BE INSTALLED. FAILURE TO DO SO COULD
RESULT IN DAMAGE TO THE DISPENSING MECHANISM AND VOID THE WARRANTY.
DURING THE AUTOMATIC AGITATION CYCLE AND/OR WHILE DISPENSING ICE, THERE
MUST BE ADEQUATE ROOM BETWEEN THE TOP OF THE ICE LEVEL AND THE BOTTOM OF
THE ICEMAKER SO THAT THE ICE CAN MOVE WITHOUT OBSTRUCTION.
CONTACT YOUR ICEMAKER SUPPLIER FOR INFORMATION ON PROPER BIN THERMOSTAT.
CAUTION
BEFORE REMOVING ANY PARTS IN THE BIN, ENSURE THE UNIT IS DISCONNECTED FROM
THE POWER SOURCE. AUTOMATIC AGITATION MAY GO OFF AT ANY TIME, AND THE
AGITATOR MAY CAUSE INJURY.
1.5
OPTIONAL INSTALLATION OF SOLD-OUT DEVICE
A. An optional Sold-Out Device can be used to automatically shut off the Syrup Pump when the
Package(s) is empty. This stops the operation of the Pump and the exhaust of gas until a new
syrup package is connected to the Pump.
B. The Lancer Sold-Out device measures syrup vacuum in the Pump Inlet Line. When the Syrup
Package is empty, the Pump increases vacuum causing the device to shut off the gas pressure
to stop the Pump. The Lancer Sold-Out automatically resets, after new Syrup Packages are
connected.
2.
CLEANING AND SANITIZING INSTRUCTIONS
2.1
GENERAL INFORMATION
A. Lancer equipment (new or reconditioned) is shipped from the factory cleaned and sanitized in
accordance with NSF guidelines. This equipment must be cleaned and sanitized after
installation is complete, and the operator of the equipment must provide continuous
maintenance as required by this manual and/or state and local health department guidelines to
ensure proper operation and sanitation requirements are maintained.
NOTE
The cleaning and sanitizing procedures provided herein pertain to the Lancer equipment
identified by this manual. If other equipment is being cleaned, follow the guidelines established
for that equipment.
B. Cleaning and sanitizing should be accomplished only by trained personnel. Sanitary gloves are
to be used during cleaning and sanitizing operations. Applicable safety precautions must be
observed. Instruction warnings on the product being used must be followed.
C. Water lines are not to be disconnected during the cleaning and sanitizing of syrup lines to avoid
contamination.
D. Do NOT use strong bleaches or detergents. They tend to discolor and/or corrode various
materials.
E. Do NOT use metal scrapers, sharp objects, steel wool, scouring pads, abrasives, solvents, etc.,
on the dispenser.
F.
Do NOT use hot water above 140°F (60°C). This may damage certain materials.