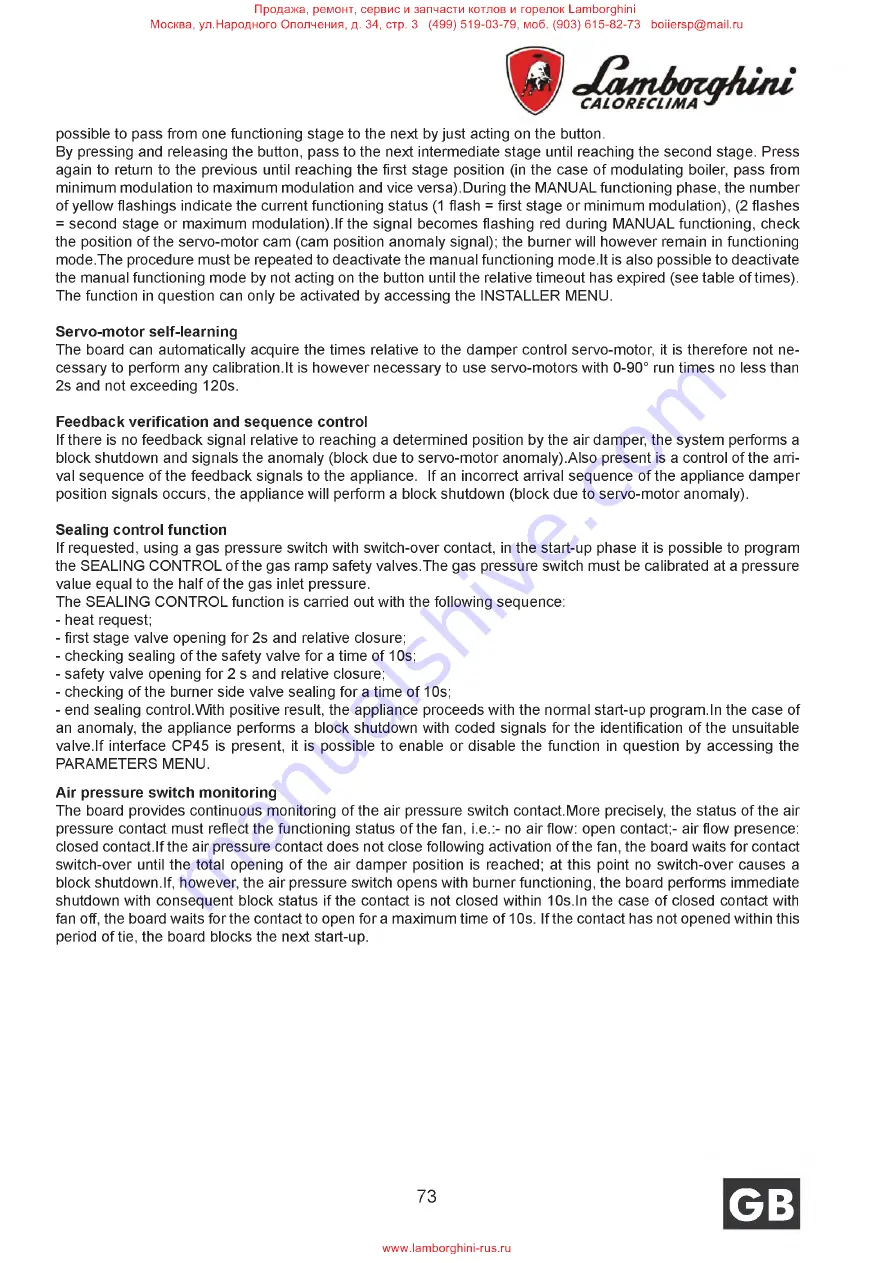
Продажа, ремонт, сервис и запчасти котлов и горелок Lamborghini
Москва,ул.НародногоОполчения,д. 34,стр. 3 (499) 519-03-79, моб. (903) 615-82-73 [email protected]
possible to pass from one functioning stage to the next by just acting on the button.
By pressing and releasing the button, pass to the next intermediate stage until reaching the second stage. Press
again to return to the previous until reaching the first stage position (in the case of modulating boiler, pass from
minimum modulation to maximum modulation and vice versa).During the MANUAL functioning phase, the number
of yellow flashings indicate the current functioning status (1 flash = first stage or minimum modulation), (2 flashes
= second stage or maximum modulation).If the signal becomes flashing red during MANUAL functioning, check
the position of the servo-motor cam (cam position anomaly signal); the burner will however remain in functioning
mode.The procedure must be repeated to deactivate the manual functioning mode.It is also possible to deactivate
the manual functioning mode by not acting on the button until the relative timeout has expired (see table of times).
The function in question can only be activated by accessing the INSTALLER MENU.
Servo-motor self-learning
The board can automatically acquire the times relative to the damper control servo-motor, it is therefore not ne
cessary to perform any calibration.lt is however necessary to use servo-motors with 0-90° run times no less than
2s and not exceeding 120s.
Feedback verification and sequence control
If there is no feedback signal relative to reaching a determined position by the air damper, the system performs a
block shutdown and signals the anomaly (block due to servo-motor anomaly).Also present is a control of the arri
val sequence of the feedback signals to the appliance. If an incorrect arrival sequence of the appliance damper
position signals occurs, the appliance will perform a block shutdown (block due to servo-motor anomaly).
Sealing control function
If requested, using a gas pressure switch with switch-over contact, in the start-up phase it is possible to program
the SEALING CONTROL of the gas ramp safety valves.The gas pressure switch must be calibrated at a pressure
value equal to the half of the gas inlet pressure.
The SEALING CONTROL function is carried out with the following sequence:
- heat request;
- first stage valve opening for 2s and relative closure;
- checking sealing of the safety valve for a time of 10s;
- safety valve opening for 2 s and relative closure;
- checking of the burner side valve sealing for a time of 10s;
- end sealing control.With positive result, the appliance proceeds with the normal start-up program.In the case of
an anomaly, the appliance performs a block shutdown with coded signals for the identification of the unsuitable
valve.If interface CP45 is present, it is possible to enable or disable the function in question by accessing the
PARAM ETERS MENU.
Air pressure switch monitoring
The board provides continuous monitoring of the air pressure switch contact.More precisely, the status of the air
pressure contact must reflect the functioning status of the fan, i.e.:- no air flow: open contact;- air flow presence:
closed contact.If the air pressure contact does not close following activation of the fan, the board waits for contact
switch-over until the total opening of the air damper position is reached; at this point no switch-over causes a
block shutdown.If, however, the air pressure switch opens with burner functioning, the board performs immediate
shutdown with consequent block status if the contact is not closed within 10s.In the case of closed contact with
fan off, the board waits for the contact to open for a maximum time of 10s. If the contact has not opened within this
period of tie, the board blocks the next start-up.
73
GB