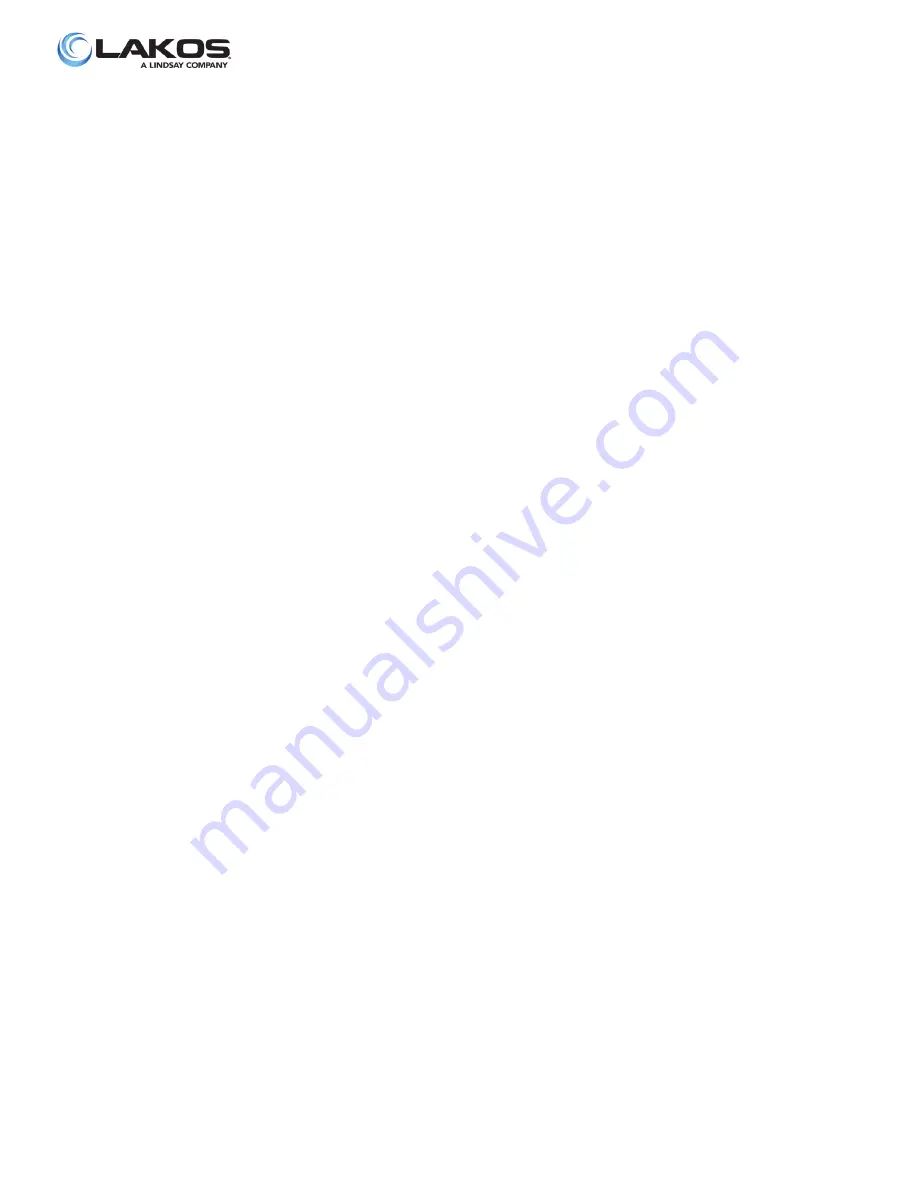
7
Installation Operations and Maintanence
Trouble-Shooting Guidelines For Separator Installation
1. Verify Actual Flow Rate:
Use pressure gauges to indicate differential pressure and flow meter to verify flow rate.
(Multiple pumps used to increase flow are installed in parallel (into common manifold);
multiple pumps to increase pressure are installed in series (one after another).
Flow meters should be installed prior to the separator. Flow meters installed after the
separator will indicate erroneous data.
2. Plumbing Two Separators:
Do not plumb two separators from two independent pumps into the same outlet header
without installing balancing valves on the discharge of each separator. The balancing
valves must be set to achieve a pressure loss across each separator that indicates a flow
rate (according to that model’s published flow chart) equal to the flow rate anticipated
through the pump that feeds each separator.
3. Verify Actual Inlet Pressure:
Actual inlet pressure must be at least 15 psi (1.03 Bar). A minimum back pressure of 5
psi (.34 Bar) must be created at the separator discharge. This may be accomplished via
process equipment, piping, or a valve. Unrestricted open discharge to a pit, sump,
etc., will result in unacceptable performance. Be sure that no source of vacuum/suction
exists in the piping arrangement. If vacuum/suction exist (i.e. downward piping after
the separator, pump suction installation, booster pump etc.), put a valve between the
separator and the suction source and pressure gauges on either side of the valve. Throttle
the flow until the pressure loss across the separator indicates the published flow rate
which most closely resembles the anticipated flow rate through the separator.
4. Vibration:
Check installation piping inlet & outlet configurations (see appropriate product sheets for
model of separator installed). Mild vibration is possible in some installations and should
be considered normal. Excessive vibration is typically due to entrained air (use air
vents), improper piping (follow the installation instructions) or system vibration
(amplified at the separator).