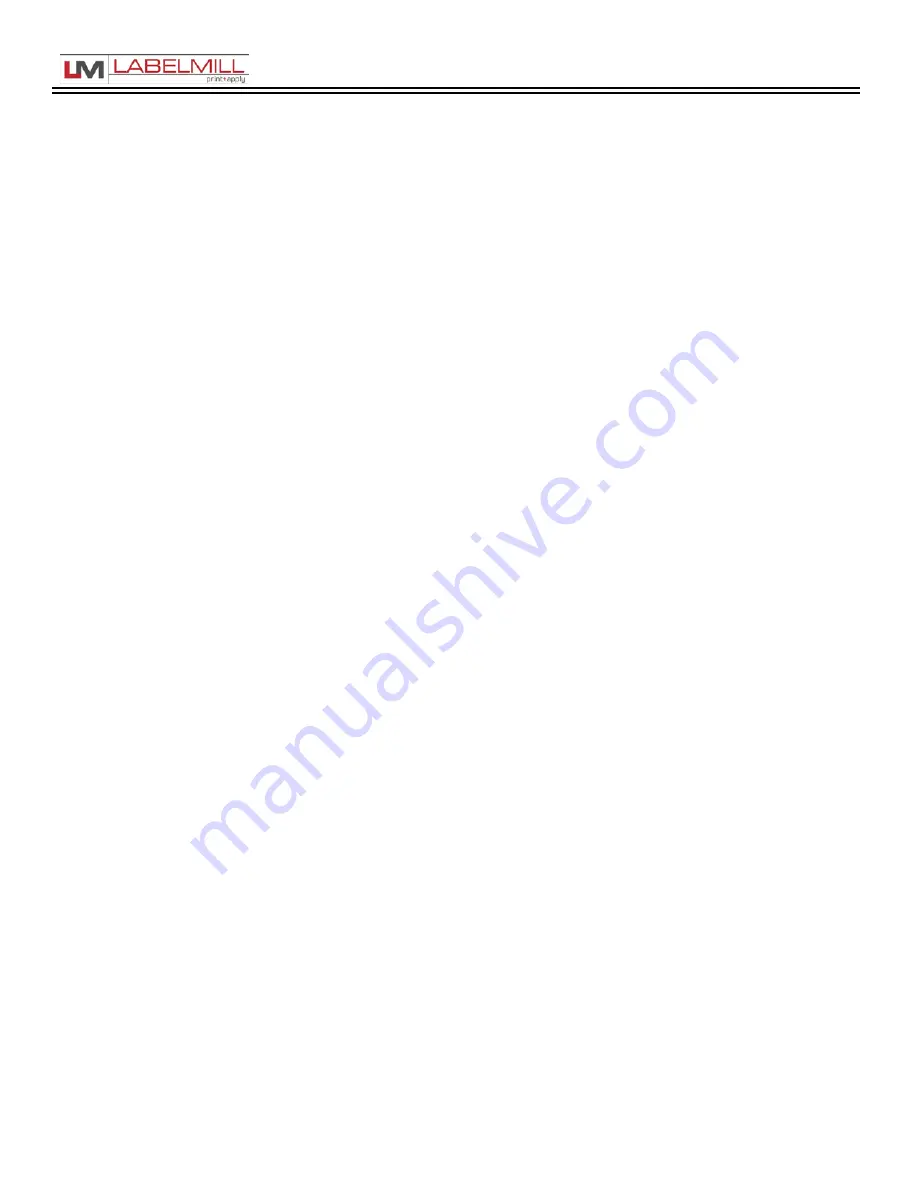
LM3606 PRINT & APPLY SYSTEM
USER’S MANUAL
Page 41
Made in the U.S.A.
© 2021 LabelMill
06/01/2021 Model LM3606
KEY DEFINITIONS
•
ASYNCHRONOUS OPERATION – The term “ASYNCHRONOUS OPERATION” is used because the speed of the
printer applicator motor (label speed) does not necessarily match the speed of the product conveyor. In other words
their speed is set independently of one another and has NO interrelation. The 3606 can only be configured in
asynchronous operation.
•
SYNCHRONOUS OPERATION - The term “SYNCHRONOUS OPERATION” is used because the speed of the
applicator motor (label speed) is matched to the speed of the product conveyor. In order to accomplish this, an
encoder is used to monitor the speed and distance the product conveyor travels. In order for this feature to function
the “CONVEYOR LOCK” mode must be turned on. In synchronous operation, the applicator motor is
ELECTRONICALLY GEARED to the product conveyor.
The 3606 CANNOT be configured in synchronous
operation.
•
START COMPENSATION – Start compensation compensates for the reaction time of the Label Mill control and start
signal from the product switch. The purpose of start compensation is to maintain label placement on a product that is
traveling at different speeds. An example of this is a conveyor that accelerates on start up and decelerates to a stop.
At high speeds an uncompensated system would apply a label too late and the label would be placed too far back on
the product. Linear interpolation is used to correct this problem. The start compensation corrects this error by adding
an offset distance at LOW speeds, since it is not possible to apply any correction at high speed.
Note: Start
compensation ONLY effects label placement on product.
•
ELECTRONIC GEARING – Electronic gearing is a function of the product encoder and the LabelMill control. This is
used to match the speed of the applicator to the product conveyor. Electronic gearing is similar to mechanical gearing
in that there is a gear ratio and the change of speed of one affects the speed of the other. This feature is part of the
Synchronous feed mode. In order for this to operate properly, the correct number of lines per inch of product travel
must be entered into the ENC LINES/INCH in encoder setup menu.
•
ENCODER – AN ENCODER is a device that is used to monitor the speed of an external device like a product
conveyor. The reason this speed is monitored is to match the speed of the label applicator to the product speed. An
encoder uses “LINES or COUNTS” per revolution in order to track speed and distance. Note that lines per revolution
are also referred to as counts per revolution. These counts are feed into the LABEL MILL control to be processed for
the different features that require this feedback.
•
ENCODER OVERRIDE – This feature is used in conjunction with ELECTRONIC GEARING. This feature is used to
fine-tune the ratio of the applicator to the product conveyor.
•
TRIGGER DIST – TRIGGER DISTANCE is used in conjunction with the encoder feature. Trigger distance is similar to
product delay in that it is used to electronically move the placement of the label on the product. When the encoder
feature is used, the product delay feature is rendered inactive. Trigger distance will move the label placement in
inches (00.00).
•
PRODUCT DELAY is NOT used in conjunction with the encoder feature. Product delay is similar to trigger distance in
that it is used to electronically move the placement of the label on the product. Product delay will move the label
placement in time (00.000) seconds. Because the product delay feature utilizes time, the speed of the product MUST
remain constant. A product traveling at a higher velocity will travel further in a given time, thus effecting the placement
of the label.
3-13