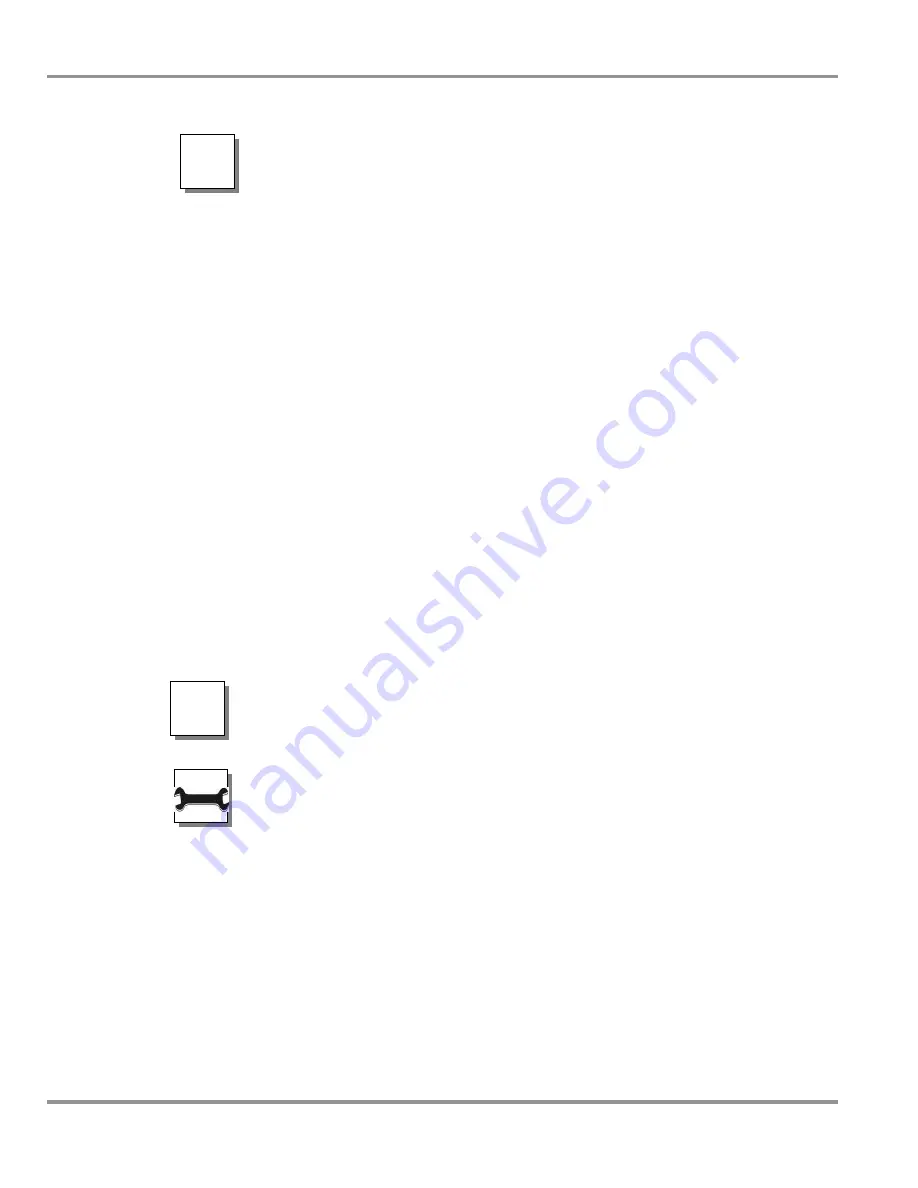
Chapter 3: Getting Started
Product Service 1-800-522-7658
8
IF ENCLOSURE WAS DAMAGED IN TRANSIT, YOU
MUST FILE A CLAIM DIRECTLY WITH THE FREIGHT
CARRIER. LABCONCO CORPORATION AND ITS
DEALERS ARE NOT RESPONSIBLE FOR SHIPPING
DAMAGES.
Do not discard the packing material until you have checked all of the
components and tested the glove box.
Installing the Glove Box on a Supporting
Structure and Work Surface
Exercise caution when lifting or moving the glove box.
When installing the glove box onto a work surface or benchtop, ensure that
the structure can safely support the combined weight of the glove box and
any related equipment. The work surface should be as wide as the entire
glove box to properly support it. The front of the glove box should be
aligned with the front of the work surface for optimal comfort. A height of
35"-40" (889mm-1016mm) is appropriate for standing operation. Labconco
base stands from Chapter 7 may be adjusted in height from 33"-40" (838mm-
1016mm).
Connecting the Exhaust to the Pressure Relief
Valve (If Applicable)
WARNING: The weight of the pressure relief exhaust
ductwork system must be supported independently of the
glove box superstructure or damage may occur.
The exhaust system should be installed by a qualified
HVAC contractor.
As stated in Chapter 2, the main chamber pressure relief valve is exhausted
back into the room unless an optional vent kit is installed. Figure B-1 in
Appendix B shows the location of the pressure relief valve without any
optional vent kits. Labconco provides pressure relief exhaust kits, which
exhaust to the outside. HEPA and/or carbon filtered exhaust kits are also
available. The HEPA and/or carbon filtered pressure relief exhaust kits also
provide thimble duct connections for exhausting the pressure relief valve to
the outside.
!