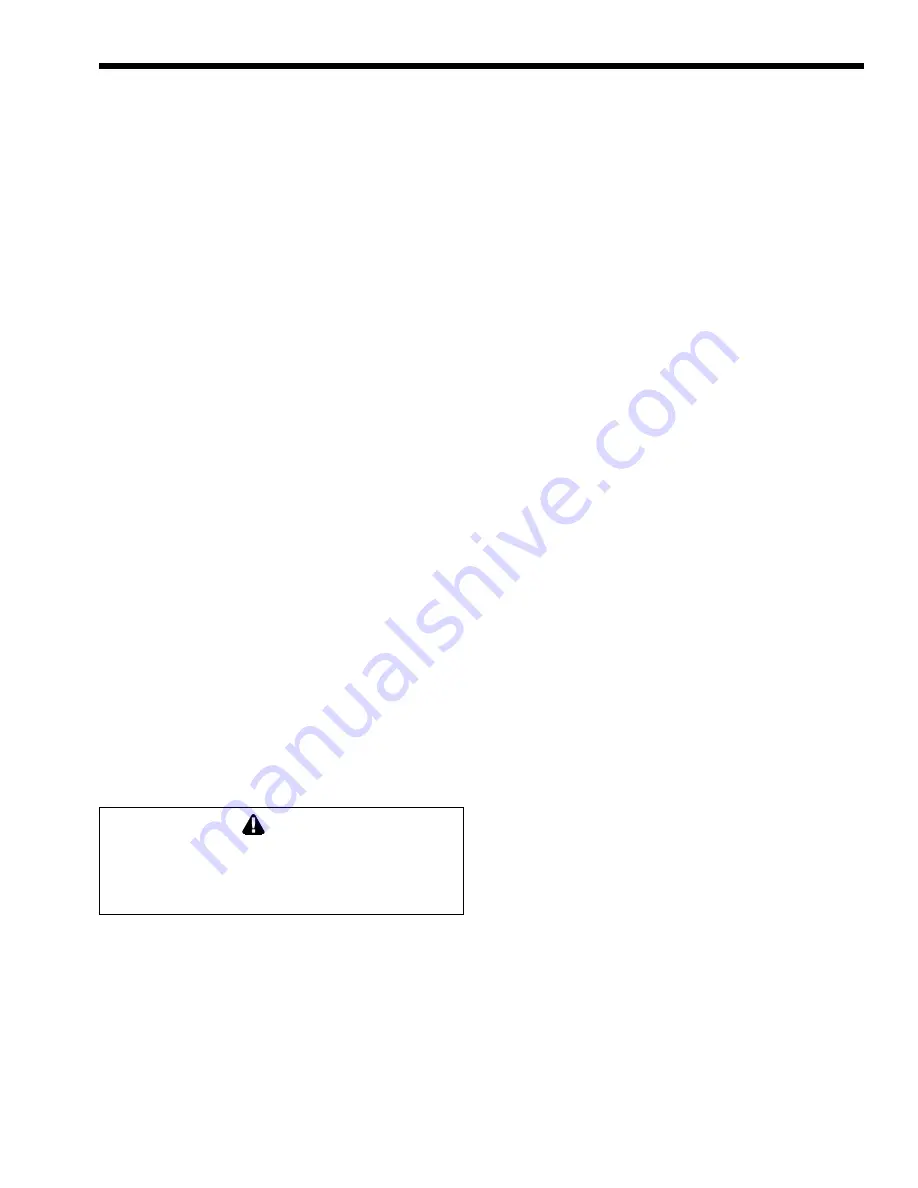
Trianco Newport
Page 3
SECTION 1.
General Information
These boilers have been designed and
constructed according to ASME codes using heavy
gauge steel tubes and boiler plate.
The reliable heat exchanger incorporates special
flue baffles to assure quiet and efficient operation and
a purpose designed ceraform combustion chamber
minimizes base loss and also provides a tight
enclosure with the heat exchanger.
The domestic hot water coil is located at the top
of the boiler in the hottest zone for an ample supply of
hot water and a unique feature of its attachment is the
raised coil flange which allows the use of clamping
bolts rather than studs, thereby eliminating water leaks
caused by broken studs.
The complete unit comes pre-assembled for easy
installation and is encased by a fully insulated baked
enamel jacket.
1A. Boiler Installation
For recommended installation practice reference
should be made to the National Fire Protection
Standard for Oil Burning Equipment (NFPA 31 -
Latest Edition).
1B. Freight Claims
Inspection should be made of boiler and its
components for damage upon arrival. Any claims for
damage should immediately be filed against the
carrier by the consignee.
1C. Boiler Location
The boiler should be positioned as near to the
chimney as possible and have a minimum smoke pipe
connector length of 18"(457mm).
Caution
Newport boilers must not be directly connected to a
heating system using oxygen permeable tubing (see
warranty). Use a water to water heat exchanger
between boiler and system to prevent corrosion.
1D. Boiler Clearances (to combustibles)
Top - 6" (152mm)
Front - 24" (610mm)
Rear - 6" (152mm) Sides - 6" (152mm)
1E. Floor
The boiler must be mounted on a
noncombustible masonry or cement floor with no
combustibles underneath.
1F. Combustion and Ventilation Air
To insure an adequate supply of fresh air for
combustion and ventilation an inlet and outlet opening
should be provided at floor and ceiling level. Each
opening must have a minimum of one square inch
(16.5 sq. cm) of free area for every 1,000 BTU/h
(293kW) of input or 140 square inches (903 sq. cm)
per one gallon (3.785L) of oil burned per hour. The
openings must not be in a position liable to blockage.
1G. Chimney and Draft Requirements
To assure the safe and proper operation of the oil
burner the boiler must be connected to a chimney
having sufficient draft at all times to evacuate the flue
gases to atmosphere. A draft regulator must be
installed in the smoke-pipe as near to the flue as
possible and adjusted to achieve an overfire draft of
0.01 ins. W.C.
1H. Jacket (normally fitted)
If not fitted, assemble panels in accordance with
instructions in Figure 4.
1I. Oil Burner (normally fitted)
If not fitted, insert burner tube into boiler so that
it is approximately ¼" (6mm) from inside wall of
ceraform chamber, then clamp mounting flange and
bolt up to front-plate (see Figure 3).
The burner should be wired and connected to the
oil line in accordance with the manufacturer’s
instructions.
1J. Boiler Controls (normally fitted)
If controls are supplied separately, fit them to the
boiler in the positions shown in Figure 3, with jacket
in place.
Circulator - 1¼" return tapping at front of boiler.
Tridicator - temp/press. gauge.
Relief Valve - Provide ¾" tee and auto vent as
shown on front page for air elimination.
Aquastat Relay - L8124A - ¾" tapping in coil
plate.
Fit a drain valve (not supplied) in a tee at
hydronic return connection and check all connections
are made water tight.
1K. Oil
USE ONLY No. 2 HEATING OIL. Do not use
gasoline, crankcase draining or any oil containing
gasoline.
1L. Oil Storage and Pipe Layout
Storage Tank:
Consult local fire and building
codes for acceptable fuel storage methods in your area.
Fuel Line:
A single pipe system of not less than
3/8" OD copper tubing is recommended when fuel