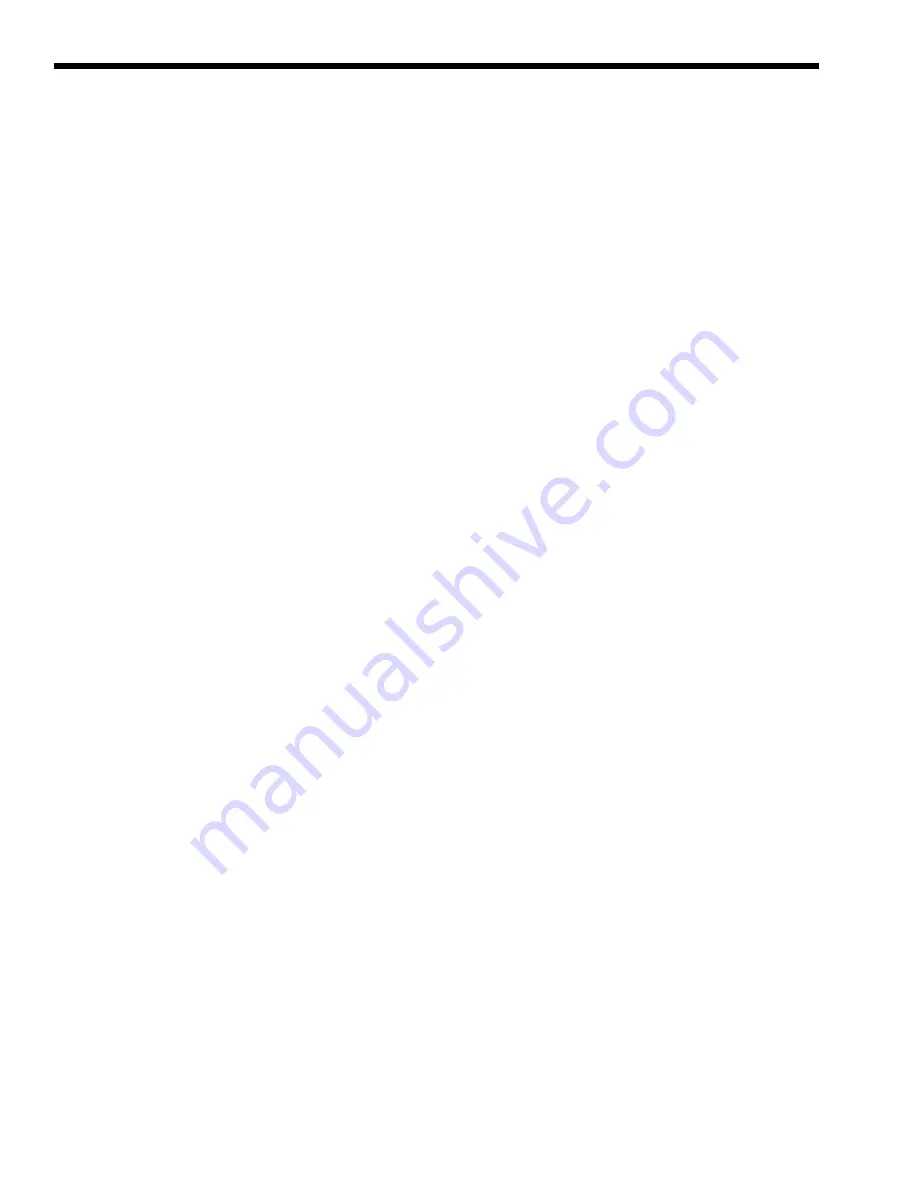
LAARS HEATING SYSTEMS
Page 10
3.2.5 Piping System Requirements
1.
Provide a boiler installed above radiation level
with a low water cutoff device either as part of
the boiler or at the time of boiler installation.
2.
Install manual and/or automatic bleeding devices
at high points in the system to eliminate air.
Install a correctly sized expansion or
compression tank with suitable air charger and
tank drainer, as appropriate.
3.
Support the weight of all water and gas piping by
suitable hangers or floor stands.
4.
Check piping diagrams with local applicable
plumbing, heating and building safety codes.
3.2.6 Filling The System
1.
Ensure the system is fully connected. Close all
bleeding devices and open make-up water valve.
Allow system to fill slowly.
2.
If make-up water pump is employed, adjust
pressure switch on pumping system to provide a
minimum of 12 psi (81.8 kPa) at the highest
point in the heating loop.
3.
If a water pressure regulator is provided on the
make-up water line, adjust the pressure regulator
to provide at least 12 psi (81.8 kPa) at the
highest point in the heating loop.
4.
Open bleeding devices on all radiation units at
the high points in the piping throughout the
system, unless automatic air bleeders are
provided at such points.
5.
Run system circulating pump and boiler pump
for a minimum of 30 minutes with the boiler gas
shut off.
6.
Open all strainers in the circulating system,
check flow switch operation, and check for
debris.
7.
Recheck all air bleeders as described in Step 4
above.
8.
Check liquid level in expansion tank. With the
system full of water and under normal operating
pressure, the level of water in the expansion tank
should not exceed 1/4 of the total, with the
balance filled with air.
9.
Start up boiler according to procedure described
in Section 4. Operate the entire system, including
the pump, boiler, and radiation units for one (1)
hour.
10.
Recheck the water level in the expansion tank. If
the water level exceeds 1/4 of the volume of the
expansion tank, open the tank drainer and drain
to that level.
11.
Shut down the entire system and vent all
radiation units and high points in the system
piping as described in Step 4 above.
12.
Close make-up water valve and check strainer in
pressure reducing valve for sediment or debris
from the make-up water line. Reopen make-up
water valve.
13.
Check gauge for correct water pressure and also
check water level in system. If the height
indicated above the boiler insures that water is at
the highest point in the circulating loop, then the
system is ready for operation.
14.
Within three (3) days of start-up, recheck all air
bleeders and expansion tank as described in
Steps 4 and 8 above.
3.3 Water Heater (PW Model)
3.3.1 Water Chemistry
Laars equipment is designed for use in a wide
variety of water conditions. The water velocity
maintained in the heat exchanger tubes is kept high
enough to prevent scaling from hard water and low
enough to avoid corrosion from soft water. Ninety-
five percent of the urban areas in the country have
water that is compatible with this equipment, but in
some areas a water supply will contain a large quantity
of scaling chemicals or the water may be extremely
soft and corrosive. In rare situations the water will
contain both scaling chemicals and corrosive
chemicals such as calcium or sodium chloride. These
conditions may be the result of a nearby well or
pumping station and the particular condition may not
be characteristic of the entire city water system.
If an installer observes damage from these
conditions to any water handling equipment in the
area, a factory representative should be contacted
immediately for assistance in minimizing maintenance
costs. If erosion is present, the pump impeller can be
replaced to reduce water velocity. If scaling conditions
are bad, tube cleaning maintenance schedules can be
established to prevent tube burn-out and cracking.
Neglecting the problem could mean serious damage to
the heater and water system.
Scaling can be recognized as a layer deposited
on the inner walls of the tube which reduces the inner
diameter of the tube. Scale can be any color or texture;
smooth or rough, granular or amorphous. Signs of
erosion are generally pitting, cavitation, ridges and
“islands” on the inner walls of the tubes. Since this
condition results from extremely soft water sources, or
as a result of a water softening program, the internal
copper surfaces will be extremely shiny. Other
chemicals, such as chlorine or chlorides in the water,
will cause dark surfaces of erosion.
In areas where the water supply is extremely
corrosive, it is advisable to order the heater with
cupro-nickel tubes in the exchanger.
Damage From Scaling, Corrosion, or Erosion
is Not Covered by the Warranty.