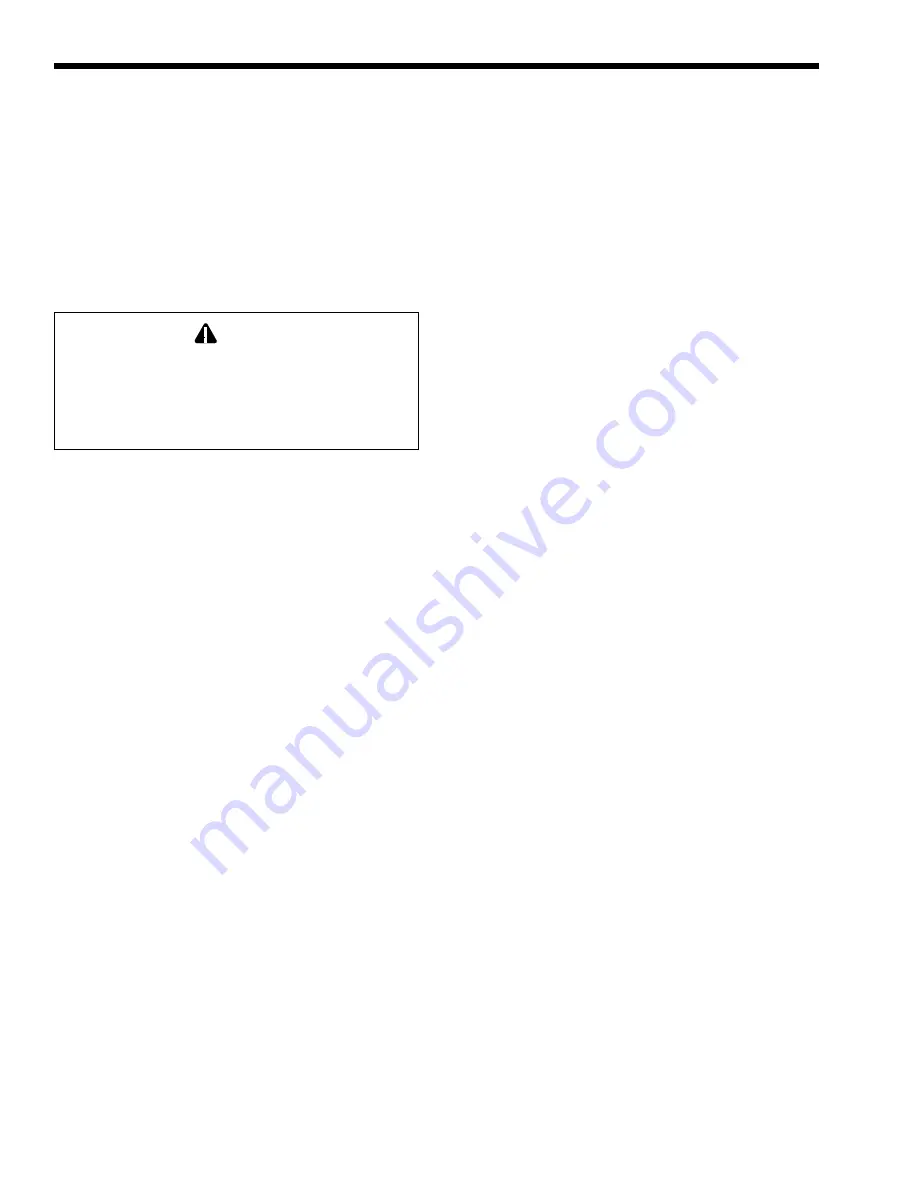
LAARS HEATING SYSTEMS
Page 20
6.
Disconnect the flange and the adapter tee from
the heat exchanger inlet and outlet.
7.
Remove temperature-sensing probes from inlet
and outlet header.
8.
Remove the heat exchanger from the heater. The
heat exchangers are heavy and require
minimum two people to remove to avoid
personal injury
9.
Remove the tube’s baffles from the heat
exchanger.
Caution
Black carbon soot buildup on a dirty heat
exchanger can be ignited by a random spark or
flame. To prevent this from happening, dampen
the soot deposits with a wet brush or fine water
spray before servicing the heat exchanger.
10.
Clean the heat exchanger: A light accumulation
of soot or corrosion on the outside of the heat
exchanger can be easily removed after the heat
baffles are removed. Use a wire brush to remove
loose soot and scale from the heat exchanger. Do
not use water or compressed air for cleaning.
NOTE: While the heat exchanger is out of the
heater, inspect the firewall refractory blocks for
cracks, wear and breakage. Replace if necessary.
11.
Reassemble in reverse order and be sure the heat
exchanger baffles are replaced.
5.3.2 Internal Cleaning of Heat Exchanger
1.
To remove the heat exchanger, follow the
procedure detailed in 5.3.2 (1 through 8).
2.
Remove the inlet/outlet header of the heat exchanger.
3.
Remove the return cover of the heat exchanger.
4.
Clean the internal surface. (Laars offers a tube
cleaning kit part no. R00100000.)
5.
Reassemble in the reverse order.
5.4 Gas and Electric Controls
The gas and electric controls on the heaters are
designed for both dependable operation and long life.
Safe operation of the heater depends on their proper
functioning. A professional service technician should
check the following basic items every year, and
replace when necessary.
NOTE: the warranty does not cover damage
caused by lack of required maintenance or improper
operating practices.
1.
Water temperature controls.
2.
Ignition control system.
3.
Air pressure proving switch(es).
4.
Automatic electric and manual gas valve(s).
5.
Water flow sensing safety device.
6.
Low water cutoffs (every six months).
5.5 Burner Removal and Cleaning
1.
Disconnect electrical supply to the heater.
2.
Turn off main manual gas valve on the heater.
3.
Remove the cover of air mixture plenum.
4.
Disconnect air tube(s) from air mixture plenum
barb(s), and remove wires from igniter and flame
sensor.
5.
Disconnect gas valve train from the gas manifold.
6.
Remove screws from manifold mounting
brackets. Pull manifold/orifice assembly away
from the burner panel.
7.
Remove screws attaching air mixture plenum to
the side air duct(s) and to the burner panel, and
then slide away the mixture plenum.
8.
Remove burner panel off the front lower jacket.
9.
Disconnect burners from panel by removing
mounting screws from each burner. Use caution
to prevent damage to burner gaskets, insulation
blanket, hot surface igniter or flame sensor.
10.
Clean soot and any debris from burners with a
stiff bristle brush. Damaged burners or burner
gaskets must be replaced.
SECTION 6.
Troubleshooting
6.1 Sequence of Operation
To troubleshoot the heater properly you must first
understand the sequence of operation of the heater:
1.
Upon a call for heat a 24 VAC signal is sent
through fusible links and high limit(s) to the
ignition control “H” terminal.
2.
The “IND” terminal of the ignition control is
energized with 115 VAC for a (15) second pre-
ignition purge period during which the combus-
tion blower purges the combustion chamber.
3.
After the purge period, terminal “S1” is
energized with 115 VAC for (20 to 35) second
igniter heat up period. The glow of the igniter
can be seen through the heater view port.
4.
Then there is a seven second trial for ignition.
During this time the gas valves are energized
with 24 VAC, and the main burner ignites. The
gas valves will remain energized throughout the
call for heat as long as the ignition control flame
sensor senses a stable flame.