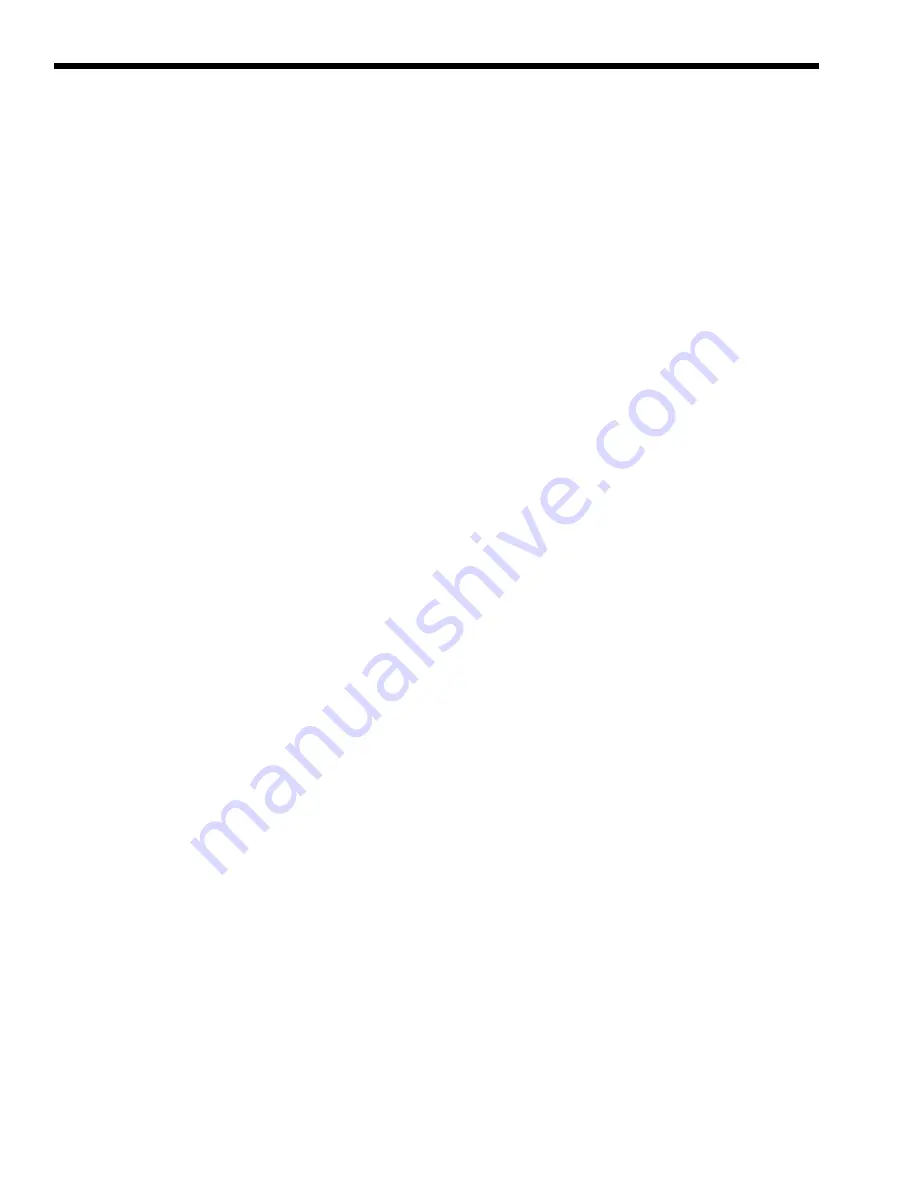
Page 12
LAARS Heating Systems
gallon of water from it. Turn off electrical power and
disconnect wires from operating control. Remove
operating control from diverting valve body and
replace with new control. Connect wires to control and
open isolation valves. Bleed air from the diverting
valve petcock, turn on electrical power and restart
boiler. The strap on type may be changed without
draining.
1P. Vent TCO
The vent TCO is a normally closed temperature
switch which functions to shutdown the burner if flue
gas temperatures exceed 180 - 200ºF (82-93°C). It is
mounted on the 3" (76mm) exhaust pipe inside the unit
between the top of the lower panel and the top. Switch
off electrical power when changing this safety.
1Q. Intake TCO
The intake TCO is a temperature switch with
normally closed contacts which open on a temperature
rise at 180°F (82°C). It is identical to the vent TCO
and functions to interrupt power to the gas valve if the
mixer tube temperature exceeds 180°F (82°C). It is
mounted on the mixer tube about 3" (76mm) above
burner flange. Switch off electrical power when
changing this safety also.
1R. Thermal Cut-Out (TCO)
The thermal cut-out is a probe type temperature
switch with normally closed contacts which open on a
temperature rise at 450°F (232°C). It is located on the
right side of the upper head with the probe extending
down into the exhaust passage between the boiler coil
and the economizer coil. It functions to interrupt power
to the gas valve if the flue gas temperatures exceed
450°F (232°C) for any reason. Switch off electrical
power when replacing.
1S. Delayed Ignition
Possible Causes - Time of occurrence
1.
High lockups on LP - occurs on start up.
2.
Gas valve regulation problem - occurs on start up.
3.
Defective burner (flameholder) - occurs primarily
on burner shutdown
4.
Natural gas orifice in LP unit - occurs on startup
High lock up pressures on LP fuel systems are
the most common cause of delayed ignitions on
Heatmaker boilers. The high LP supply pressure
results from improper second stage regulator selection
or a faulty regulator.
It can be detected by measuring the gas supply
pressure to the unit at the inlet pressure tap on the gas
valve. Use a water manometer or pressure gage with a
scale reading of at least 25 in. W.C. or 1 oz/in 2.
Install the pressure tap in the 1/8 NPTF plugged port
located above the gas inlet port on the gas valve. The
gas supply to the boiler must be shut off before making
this connection. The Heatmaker boiler is designed to
operate with supply pressures of 4-14 in. W.C. (8.1 oz/
in2) with the boiler not operating it is likely that this is
the cause of the delayed ignition. Lock up pressures
must be measured when the boiler is not operating and
preferably immediately after boiler shutdown.
Gas valve regulation problems can also cause
delayed ignitions. To detect gas valve regulation
problems it is necessary to have an inclined manometer
or a Magnehelic pressure gage. The normal gas valve
regulator setting is -0.2 IN. W.C. This should happen
smoothly without allowing pressure spikes positive
when the solenoid opens then the gas valve regulator is
faulty and may be the cause of the delayed ignition.
A defective burner (flameholder) can cause a
delayed ignition however not often. If the gas supply
pressure and the gas valve are functioning properly and
the air and gas orifices are correct the burner should be
inspected. To inspect, remove the mixer tube and the
burner will lift out of the top of the chamber. There
should be no perforations other than the punched holes.
Replace in the reverse order with new gaskets.
1T. High Gas Consumption
Improper burner operation caused by incorrect
air/fuel ratio (CO2 or high O2 out of the specified
range) will cause high gas consumption. It is most
noticeable on LP fired units with low CO2 or high O2,
however, units operating on LP or natural gas with
incorrect air/fuel ratios will not provide their best
efficiency. If no combustion analyzing equipment
(CO2 or O2) is available, an indication of the air/fuel
ration can be gotten by briefly sniffing the flue gases.
When running properly the Heatmaker’s flue gases
should have no smell. If they have a strong piercing
smell, the gas orifice is probably too small. Do not
attempt to do re-orificing without an O2 or CO2 kit.
1U. Noisy Operation
There are two principal sources of excessive
noise.
1.
Combustion
2.
Boiling (kettling or knocking)
Combustion noise can occur when the burner is
operating with a very rich or a very lean mixture. A
rich mixture (high CO2 or low O2 - gas orifice too
large) will cause a high pitched noise that is loudest at
the vent terminal. A lean mixture (low CO2 or high O2
- gas orifice too small) will cause a very uneven
rumbly noise and may sometimes be associated with a
nuisance lockout situation and a strong piercing odor
at the vent terminal. Both noises may be eliminated by
proper burner adjustment (see Burner Adjustment).