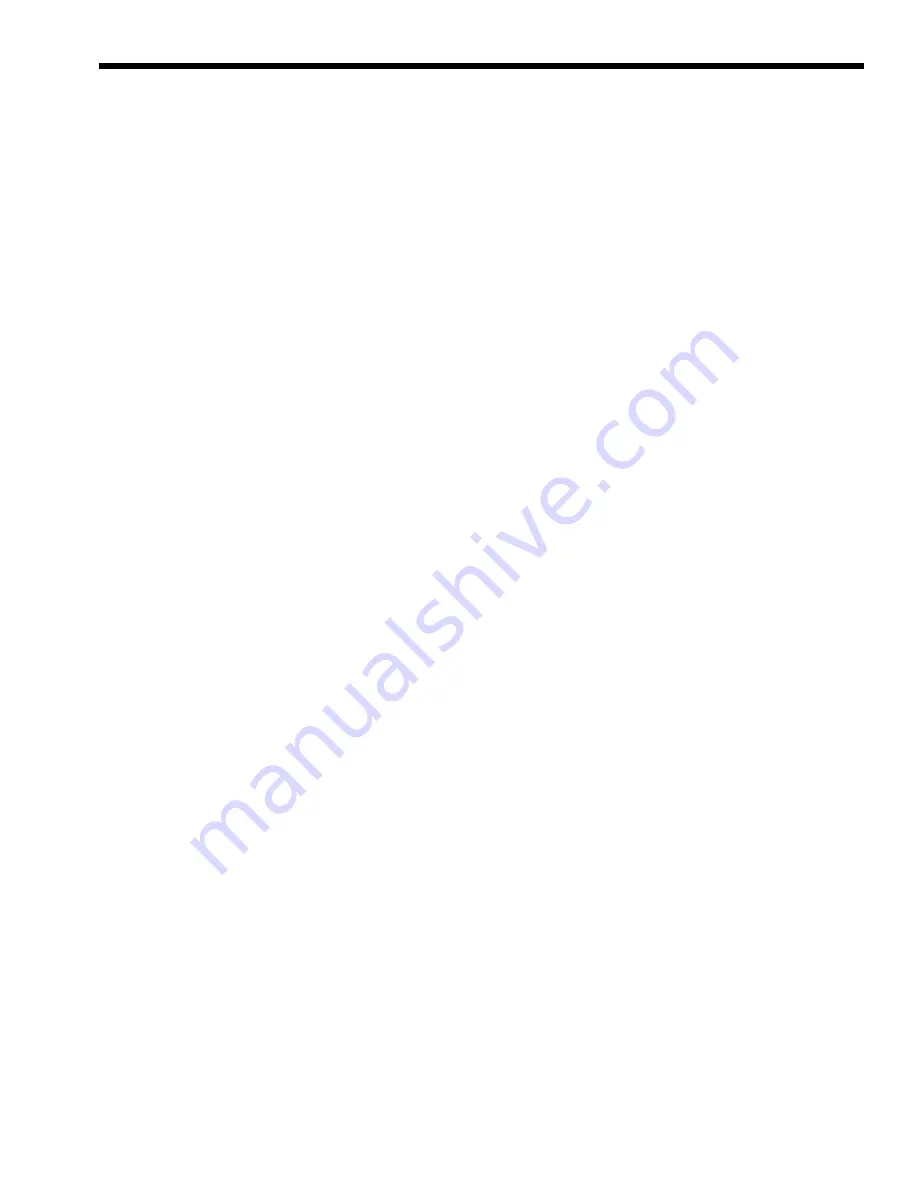
9600 CB & HWG Service Manual
Page 11
1H. Stack Switch
The Stack Switch is a normally open single pole
switch which is operated by the pressure difference
across the air orifice. It is set to close when a static
pressure difference of 1 in. W.C. is generated by the
combustion air blower. Its function is to prove airflow
and to inhibit burner operation in the event of flue
stoppage. The switch is wired directly to the boiler
control. It is located on the inside of the jacket back
panel.
1I.
Igniter
The Igniter is a “glow bar” type silicone carbide
unit. It is energized whenever there is a call for heat
and the red “IGNITER” light on the boiler control is
lit. After the igniter is switched off and boiler continues
to run, the igniter functions as a flame sensor for the
boiler control.
If the igniter fails and must be replaced, always
install a new igniter gasket with the replacement
igniter.
1J. Transformer
The control transformer accepts 120 VAC power
and provides 40 VA of 24 VAC power for the boiler
control only. It is not capable of supplying control
power for external devices such as zone valves. They
must have their own separate power supply.
1K. Unit Pump
The unit pump is a wetted rotor type pump which
operates whenever there is a call for heat or hot
water.
If a pump change is required for any reason,
valve off the boiler and drain approximately 1 or 2
gallons of water (3.79 to 7.58L) from the unit through
the drain under the chamber. Drain is accessed by
removing lower front panel. Turn off the main
disconnect switch and unplug the pump wires, remove
the pump motor. The pump housing need not be
removed. The replacement pump motor should be
installed in the reverse order from which the old pump
motor was removed. After filling the system, be sure to
bleed air from the diverting valve petcock.
1L. Blower
The combustion air blower is a high head
centrifugal blower,. It is designed to provide about 4"
W.C. of suction at 43 CFM. This performance is
necessary to operate the gas valve reliably, to
overcome induction system friction losses and to
eliminate any sensitivity to wind striking the vent
terminal. It is powered by a 120 volt motor which
draws about 1.65 amps at rated load. It is controlled
by the boiler control. Whenever there is a call for heat
and 30 seconds after, the blower should be energized.
If a blower change is required, turn off the 120 volt
power and unplug the power wires from the blower
motor. Disconnect intake exhaust vents and remove top
jacket. Remove the six bolts and nuts from the blower
discharge flange and the four nuts from the blower
inlet flange. The blower may now be deflected enough
to permit its removal. Replace the new blower using
new gaskets, in the reverse order from which the old
blower was removed. The four Inlet flange nuts,
however, should only be finger tight initially and then
tightened with a wrench after all other operations have
been completed. The combustion should be checked for
correct air-fueled ration whenever the blower is
replaced (see Burner Adjustment.)
1M. Gas Valve
The gas valve is a solenoid operated, negative
pressure regulated valve. The outlet pressure is
regulated at minus .2 inches W.C. It is designed to
operate with supply pressures of 4-14 inches W.C.
Within that range of supply pressures, the regulated
discharge pressure may vary from minus .05 to minus
.35 inches W.C. The regulator is not adjustable and the
effect of this variation in discharge pressure is not
significant. Because of the fixed regulator setting, gas
flow must only be adjusted by changing the gas orifice.
To remove the gas valve, shut off the 120 volt
power and the master gas cock in gas line, loosen the
nut on the gas orifice union and remove the orifice
union plus piping to the gas valve. Disconnect the
wires from the gas valve. the valve may now be
unscrewed from the inlet piping. It may be necessary
to deflect the inlet piping somewhat in order to clear
the boiler jacket. After the valve has been removed,
replace with a new valve in the reverse order in which
the old valve was removed. Do not overtighten the
fittings into the valve body as this may cause damage
to the valve.
1N. Time Delay Relay(TDR)
The time Delay Relay controls the unit pump and
keeps it operating for approximately one minute after
the blower post purge stops. This function dries out the
moisture in the chamber to prevent corrosion. Control
voltage on the TDR is 24 volts from the limit circuit.
The contacts to supply pump power are 120 VAC.
They open one minute after the 24 volt control voltage
is interrupted. Turn off disconnect switch before
changing TDR.
1O. Operating Control
The operating control functions as a high limit to
prevent boiler outlet temperatures from exceeding
210°F (99°C) on CBs and 185°F (85°C) on HWGs
during periods of low load or high return water
temperatures. It will reset automatically when the
boiler temperature drops to 170°F (77°C). To replace
immersion type, valve off boiler and drain about a