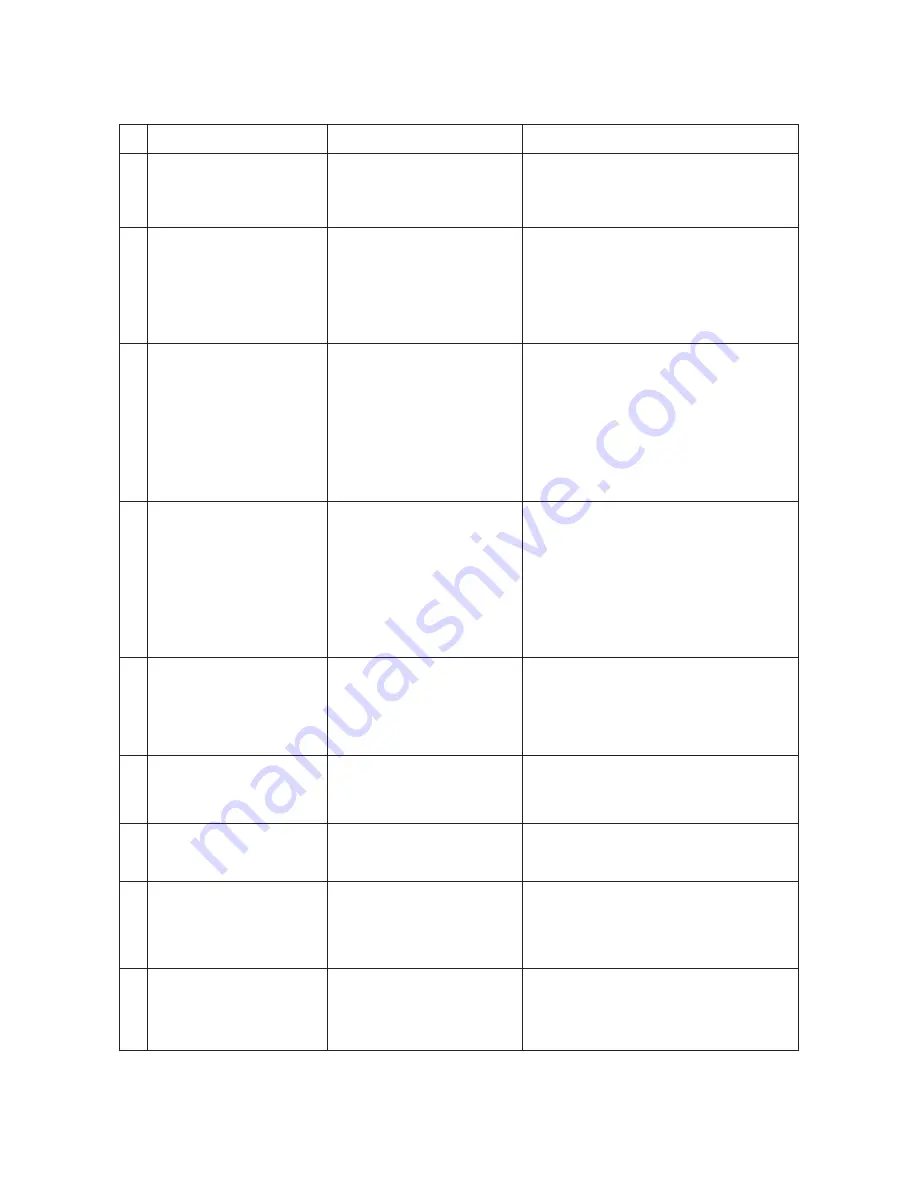
33
11. Problem solving
PROBLEM
CAUSE
SOLUTION
1. The boiler is full of water and
the water flows out of the
safety valve.
• One of the outfl ow lines from the
boiler or from a circuit of the unit
has a leak.
• Check the autolevel circuit, the manual charging
button, and the boiler heat exchangers.
• Replace worn or damaged parts to eliminate
the leak.
2. The safety valve trips in
and vents the steam.
• Malfunction of electrical system
(the electrical heating element
is always connected).
• Pressure increase in the boiler
(the safety valve trips in at 1.9-
2.5 bar).
• Check the wiring that feeds the heat-ing ele-
ment and the pressure switch.
• In the machines with electronic tem perature
control, check the proper operation of the elec-
tronic control unit, the triac, the level probe, and
the elettrical wiring.
3. The machine was started prop-
erly but the water in the boiler
does not warm up.
• The electric heating element is
defective or is not connected.
• Check if the heating element is con-nected to
the power supply.
• Check if the heating element safety thermostat
has tripped in and check its proper operation.
• In the machines with electronic tem perature
control, check the proper operation of the elec-
tronic control unit, the triac, the level probe, and
the elettrical wiring
4. There is no water fl owing from
a serving unit.
• Coffee ground too fine or ex-
cessive quantity for type of fi lter
used.
• Clogged water circuit.
• Defective solenoid.
• Adjust the grinding coarseness and/or the quan-
tity of ground coffee.
• Check that the injector, the upper cir culation
tube, the spray nozzle and the solenoid of the
unit are not clogged.
• In the machines with electronic metering, check
the displacement meter and its valves.
• Check the solenoid of the unit, its wiring and
the fuse in the electronic control unit.
5. The programmed servings of
espresso coffee are not con-
stant or vary on the dif- ferent
units.
• Abnormal operation of the elec-
tronic control unit or of the dis-
placement counters.
• Leak from serving unit solenoid
valve.
• Program the serving quantities sepa rately on
each serving unit. If the problem persists, re-
place the dis placement meter of the serving
unit affected.
• Replace the solenoid valve of the serving
unit.
6. It is not possible to pro- gram
the serving quantities on unit 1
and to copy them on the other
units.
• Abnormal operation or defective
displacement meter of unit 1.
• Check the control unit-displacement meters
electrical wiring.
• Replace the displacement meter.
7. Displacement meters alarm.
• Displacement meters jammed
or defective.
• Defective wiring.
• Replace the displacement meter.
• Check the wiring and its connections, the con-
trol unit and the fuses.
8. Autolevel alarm.
• Lack of water in the autolevel
circuit.
• M a i n w a t e r s u p p l y v a l v e
closed.
• Faulty autolevel solenoid.
• Check the hydraulic circuit of the autolevel.
• Check if the on-off valve on the water supply
is open.
• Replace the autolevel solenoid.
9. The machine is switched on
(the main switch is in position
1 or 2 and the signal light is lit)
but the electronic control is out
of order.
• The electric wiring of the elec-
tronic control unit is defective.
• The electronic control unit is
defective.
• Check the electrical wiring, the elec tronic con-
trol unit and its components.
• Replace the electronic control unit.