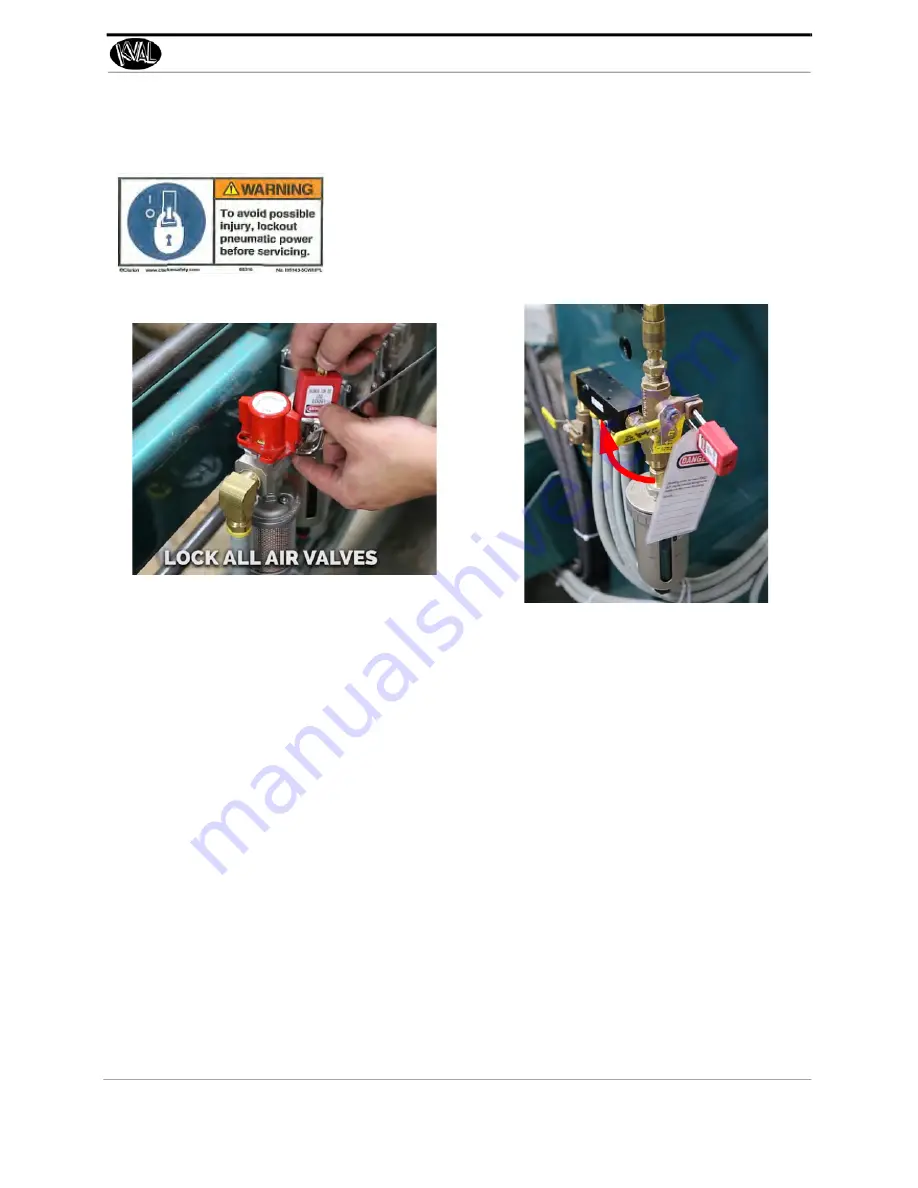
Lockout Tagout Procedure
1-9
RT-2 Operation and Service Manual
Lockout Tagout Air Supply
Start Maintenance
7.
Once the locks and tags are in place and all personnel are clear, attempt to operate
the machine to ensure equipment will not operate.
8.
Maintenance or repairs may started.
Post Maintenance Steps
9.
After maintenance is completed, the person performing the work must ensure all
tools, spare parts, test equipment, etc., are completely removed and that all guards
and safety devices are installed.
10.
Before removing the locks and tags, the person who attached them shall inspect the
equipment to ensure that the machine will not be put in an unsafe condition when
re-energized.
11.
The lock and tag can now be removed (only by the person(s) who placed them),
and the machine can be re-energized.
12.
The tags must be destroyed and the locks and keys returned to the lockout center.
6.
Turn all air valves to the OFF position and place a pad
-
lock through the hole (see illustration below).
NOTE:
Place your tag on the padlock, as per the
tagout guidelines.