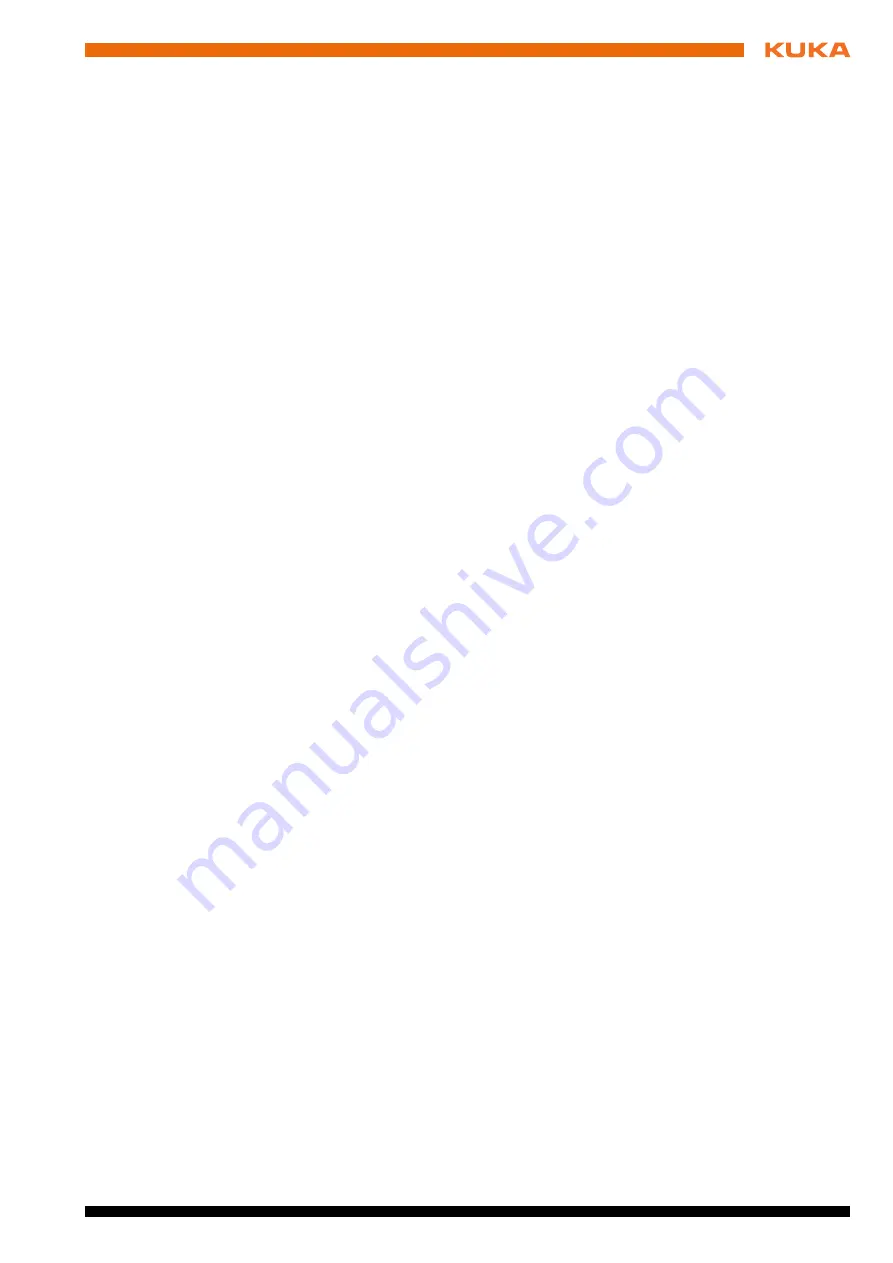
Issued: 22.04.2016 Version: Spez KR 20-3 V2
6 Planning
6.4
Connecting cables and interfaces
Connecting
cables
The connecting cables comprise all the cables for transferring energy and sig-
nals between the robot and the robot controller. They are connected to the ro-
bot junction boxes with connectors. The set of connecting cables comprises:
Motor cable, X20 - X30
Data cable X21 - X31
Ground conductor (optional)
Depending on the specification of the robot, various connecting cables are
used. Cable lengths of 7 m, 15 m, 25 m, 35 m and 50 m are available. The
maximum length of the connecting cables must not exceed 50 m. Thus if the
robot is operated on a linear unit which has its own energy supply chain these
cables must also be taken into account.
For the connecting cables, an additional ground conductor is always required
to provide a low-resistance connection between the robot and the control cab-
inet in accordance with DIN EN 60204. The ground conductors are connected
via ring cable lugs. The threaded bolt for connecting the ground conductor is
located on the base frame of the robot.
The following points must be observed when planning and routing the con-
necting cables:
The bending radius for fixed routing must not be less than 150 mm for mo-
tor cables and 60 mm for control cables.
Protect cables against exposure to mechanical stress.
Route the cables without mechanical stress – no tensile forces on the con-
nectors
Cables are only to be installed indoors.
Observe permissible temperature range (fixed installation) of 263 K (-
10 °C) to 343 K (+70 °C).
Route the motor cables and the data cables separately in metal ducts; if
necessary, additional measures must be taken to ensure electromagnetic
compatibility (EMC).
Interface for
energy supply
systems
The robot can be equipped with an energy supply system between axis 1 and
axis 3 and a second energy supply system between axis 3 and axis 6. The A1
interface required for this is located on the rear of the base frame, the A3 in-
terface is located on the side of the arm and the interface for axis 6 is located
on the robot tool. Depending on the application, the interfaces differ in design
and scope. They can be equipped e.g. with connections for cables and hoses.
Detailed information on the connector pin allocation, threaded unions, etc. is
given in separate documentation.
1
Locating pin
2
Hexagon bolt
3
Mounting surface, machined
Содержание KR 20-3
Страница 6: ...6 81 Issued 22 04 2016 Version Spez KR 20 3 V2 KR 20 3...
Страница 8: ...8 81 Issued 22 04 2016 Version Spez KR 20 3 V2 KR 20 3...
Страница 12: ...12 81 Issued 22 04 2016 Version Spez KR 20 3 V2 KR 20 3...
Страница 33: ...33 81 Issued 22 04 2016 Version Spez KR 20 3 V2 4 Technical data Fig 4 20 Stopping times for STOP 1 axis 1...
Страница 35: ...35 81 Issued 22 04 2016 Version Spez KR 20 3 V2 4 Technical data Fig 4 22 Stopping times for STOP 1 axis 2...
Страница 38: ...38 81 Issued 22 04 2016 Version Spez KR 20 3 V2 KR 20 3 Fig 4 26 Stopping times for STOP 1 axis 1...
Страница 40: ...40 81 Issued 22 04 2016 Version Spez KR 20 3 V2 KR 20 3 Fig 4 28 Stopping times for STOP 1 axis 2...
Страница 42: ...42 81 Issued 22 04 2016 Version Spez KR 20 3 V2 KR 20 3...
Страница 62: ...62 81 Issued 22 04 2016 Version Spez KR 20 3 V2 KR 20 3...
Страница 68: ...68 81 Issued 22 04 2016 Version Spez KR 20 3 V2 KR 20 3...
Страница 70: ...70 81 Issued 22 04 2016 Version Spez KR 20 3 V2 KR 20 3...
Страница 78: ...78 81 Issued 22 04 2016 Version Spez KR 20 3 V2 KR 20 3...
Страница 81: ...81 81 Issued 22 04 2016 Version Spez KR 20 3 V2 KR 20 3...