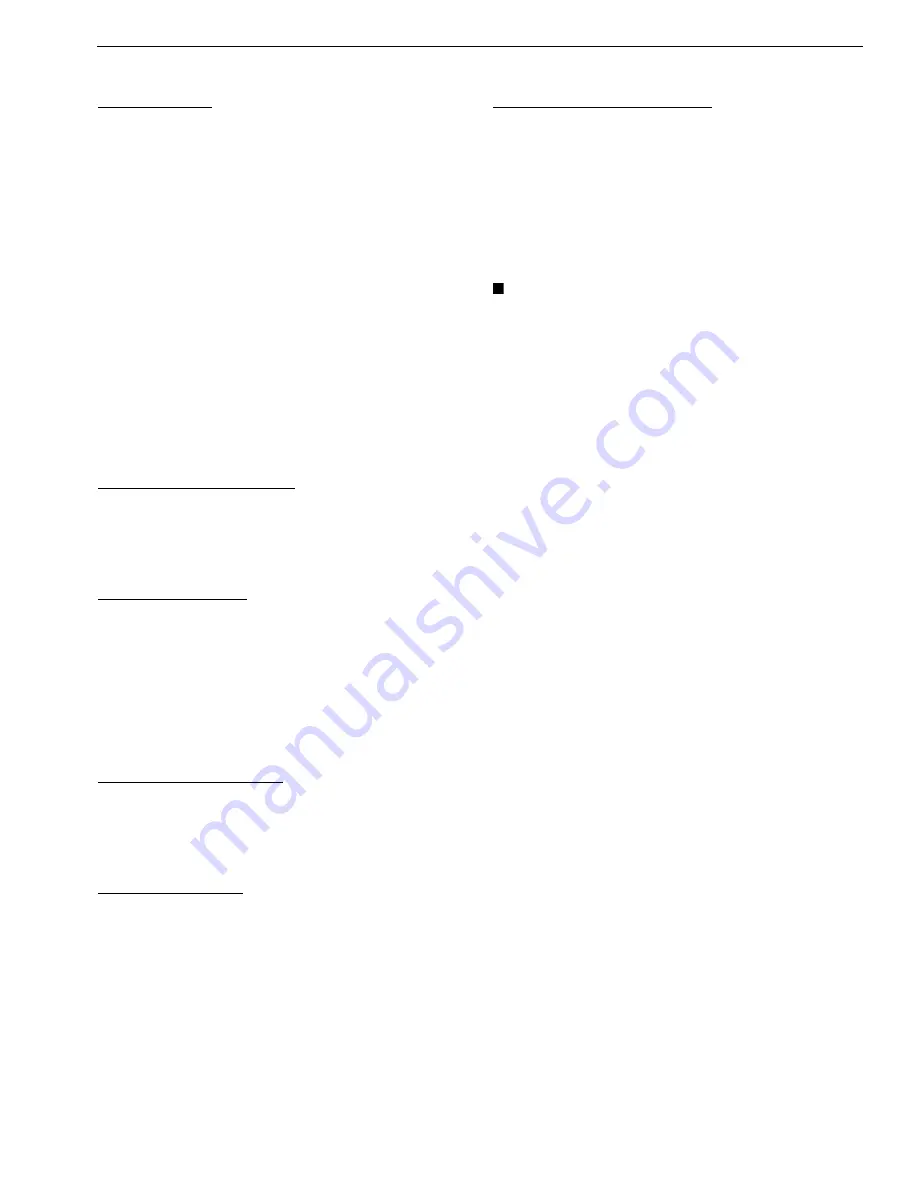
ECM SYSTEM
WG1605-G-E3,WG1605-L-E3,WG1605-GL-E3, DM
1-59
[2] Electrical System
INTRODUCTION
This section of the Kubota's manual has been
designed to allow the technician to be able to select the
section of the electrical system which is applicable to the
fuel system being used. EControls systems are
designed such that variation in fuel, engine size and
auxiliary control feature are controlled by only several
variations of Engine Control Modules (ECM). During the
design of each of Kubota fuel systems Kubota defines
the components that will interface with the EControls
ECM and what options and auxiliary system are to be
controlled by the ECM. Kubota fuel system wire harness
varies slightly not only in circuits but in length and
connector end. However each of the EControls ECM has
identical 90 pin connectors. Variations in each ECM will
dictate what the individual pin function is however there
are many of the pins which have the same function
regardless of fuel system or engine size. Some pins may
not be used in certain Kubota fuel system and are
blanked in the connector.
SYSTEM WIRING DIAGRAM
This section has shown the detail specific wire
harness diagram for Kubota fuel system and electrical
circuit. It is shown a connection to the vehicle side and
engine side each for each specification.
CONNECTOR VIEWS
For those circuits which are not likely to vary, the
individual circuits are documented in the harness section
of this manual. Also included are the standard connector
mating views which define the pin location in each
connection. The view display is from mating connector
perspective. Each connector in the overall wire harness
has a connector number which begins with the prefix
CO
- followed by a three (3) digit number.
CIRCUIT IDENTIFICATION
Circuit numbers are not identified and wire colors
may vary slightly as Kubota request specific wire colors
for certain circuits. Standard circuit descriptions are used
to identify each circuit. (example: Injector #1+)
WIRE DESCRIPTION
Each of the individual circuit diagrams contains the
wiring information necessary for the technician to make
repairs to that circuit without causing future damage to
any electrical component or the wiring harness itself. All
components use a crimped connector unless otherwise
defined.
REPAIR OF WIRING HARNESS
EControls recognizes that through normal wear or
improper handling of the main wire harness damage can
occur over time. Wires, connector ends, and pins may
become damaged and require replacement or repair.
EControls has provided in this manual a section which
described the proper repair procedures when making
repairs to any wire harness. Use this section and the
proper tools when making splices or repairs to the
harness.
NOTE
• BEFORE DIAGNOSING ANY ELECTRICAL
PROBLEM CHECK THE MAIN ECM CONNECTOR
TO IDENTIFY WHAT PINS ARE BLANKED.
• BEFORE MAKING HARNESS REPAIRS BE SURE
TO USE THE CORRECT WIRE HARNESS REPAIR
TOOLS SUCH AS CRIMPING TOOLS, WIRE
STRIPPING TOOLS, AND ELECTRICAL
DIAGNOSTIC TOOLS
• BEFORE ADDING ANY OPTIONAL ELECTRICAL
EQUIPMENT TO THE VEHICLE FITTED WITH AN
ECONTROLS SYSTEM CONSULT WITH KUBOTA
OF THE EQUIPMENT TO VERIFY THAT THE
ELECTRICAL SYSTEM CAN SUSTAIN THE NEW
ELECTRICAL LOADS AND WHERE TO
CONNECT THE ADDITIONAL LOAD.
• WHEN ADDING OPTIONAL ELECTRICAL
EQUIPMENT BE SURE TO USE A IN-LINE FUSE
OF THE PROPER ELECTRICAL LOAD TO
PROTECT THE VEHICLE ELECTRICAL SYSTEM.
KiSC issued 12, 2016 A
Содержание WG1605-E3
Страница 1: ...WG1605 E3 DIAGNOSIS MANUAL ECM SYSTEM KiSC issued 12 2016 A...
Страница 3: ...I INFORMATION KiSC issued 12 2016 A...
Страница 4: ...CONTENTS 1 SAFETY FIRST I 1 INFORMATION KiSC issued 12 2016 A...
Страница 8: ...1 ECM SYSTEM KiSC issued 12 2016 A...
Страница 10: ...23 Spark Coil Primary DTC 2300 2301 2303 2304 2306 2307 2309 2310 1 228 KiSC issued 12 2016 A...