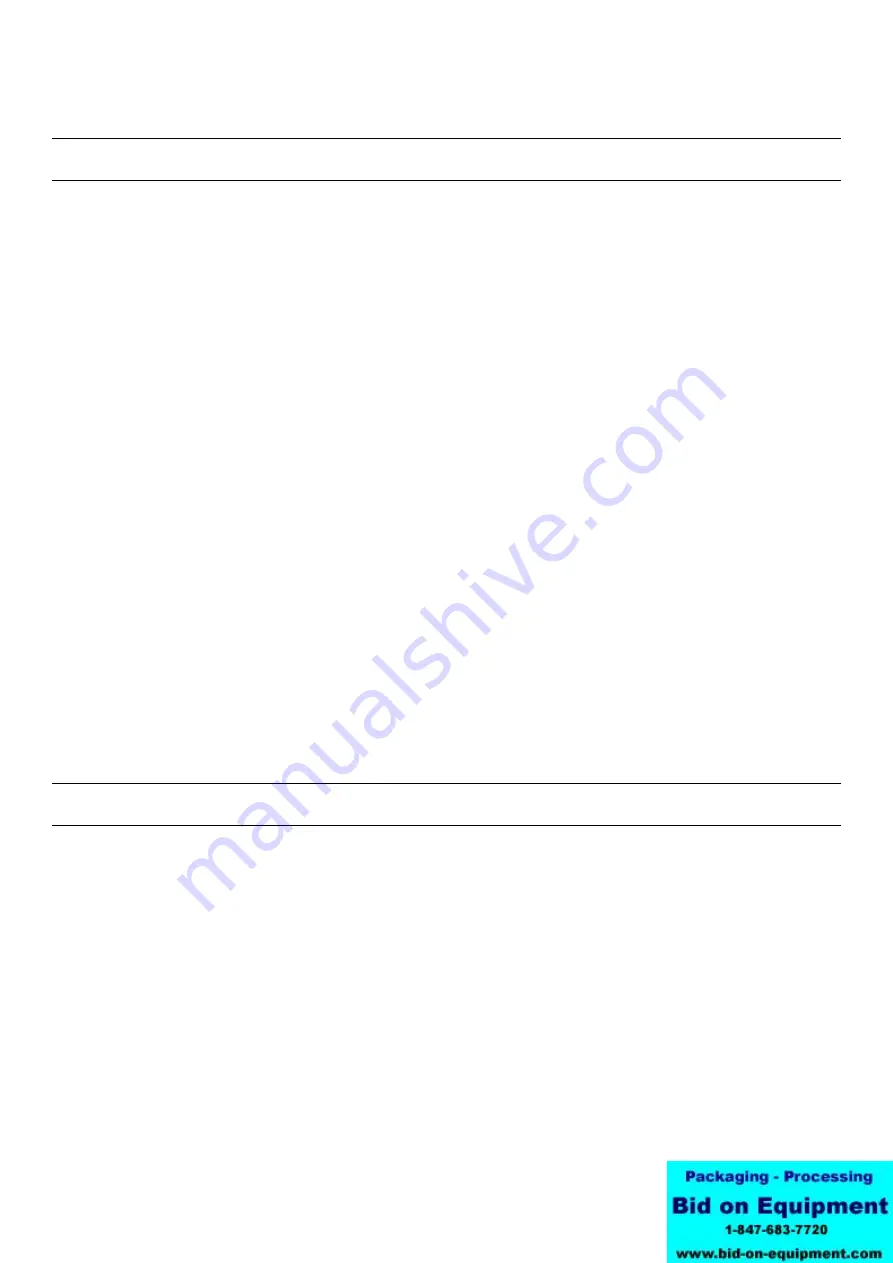
threading rollers. Screw (clockwise) or unscrew (anti-clockwise) this bush by introducing a long pin in the cavities
G
.
Once the adjustments are completed firmly lock the safety grub screw
F
.
WARNING
Make sure that before putting back safety grub screw
F
it is dipped in medium density “loctite” yellow paste.
Lift the machine so that the load on the capping inner spring is now released.
By operating intermittently the machine, turn the capping head intermittently and turning by hand the bottle bring the
second thread rollers in line with the reference mark on the bottle.
Lower the machine thus bringing the arms in the closed position and repeat the above described operations.
5
HEIGHT ADJUSTMENT OF THE TUCK-UNDER ROLLERS(Fig.3)
With the capping head mounted on the machine, insert the bottle with on top the part of the cap
A
previously cut and
bring the center
C
of the tuck-under roller in line with the the reference mark on the bottle
(Fig.3)
Lower the machine so that the roller arms close. In this position the cam follower
D
must be 2[mm] upward on the
cylindrical profile of the cam. At this point the capping inner spring is completely loaded and its load should not allow the
bottle to rotate or even be removed.
Also at this point, verify that the tuck-under roller is 0.2÷0.3 [mm] below the neck of the bottle finish
H
(tuck-under line).
Actually, this gap is the thickness of the skirt of the cap and therefore can vary according to the type of the cap to be
applied.
In the case of caps with a shaped skirt or with particular metal thickness, it is in any case necessary to check this
dimension by trial and error (capping a few bottles and observing the final tuck-under results).
To carry out any adjustments it will be necessary to loosen the safety grub screw I thus freeing the bush of the tuck-
under rollers. Screw (clockwise) or unscrew (anti-clockwise) by introducing a long pin in the cavities
L
.
Once the adjustments are completed firmly lock the safety grub screw
l
.
WARNING
Make sure that before putting back safety grub acrew
I
it is dipped in medium density “loctite” yellow paste.
6
ADJUSTMENT OF ARMS RADIAL LOAD
Normally the radial loads of the arms are set according to the technical datas supplied by the manufacturers of the caps.
However, if there should be anomalies in the formation of the thread on the cap on application, it is possible to carry out
further adjustments.
First of all it is necessary to check that the load on the spring of each arm is the same.
To measure this load it is necessary to hook the dynamometer to the arm at
M (fig.3)
and putting one hand on the
fulcrum
N
of the lever to detect any small movement of the arm itselself.
Pull hard on the dynamometer thus moving the arm towards yourself and read on the dynamometer the load of the
spring the moment you feel any movement of the arm.
To adjust the radial load act on the screw
O
. Pay particular attention when screwing or unscrewing this screw because
any little variation means a big load variation of the spring.