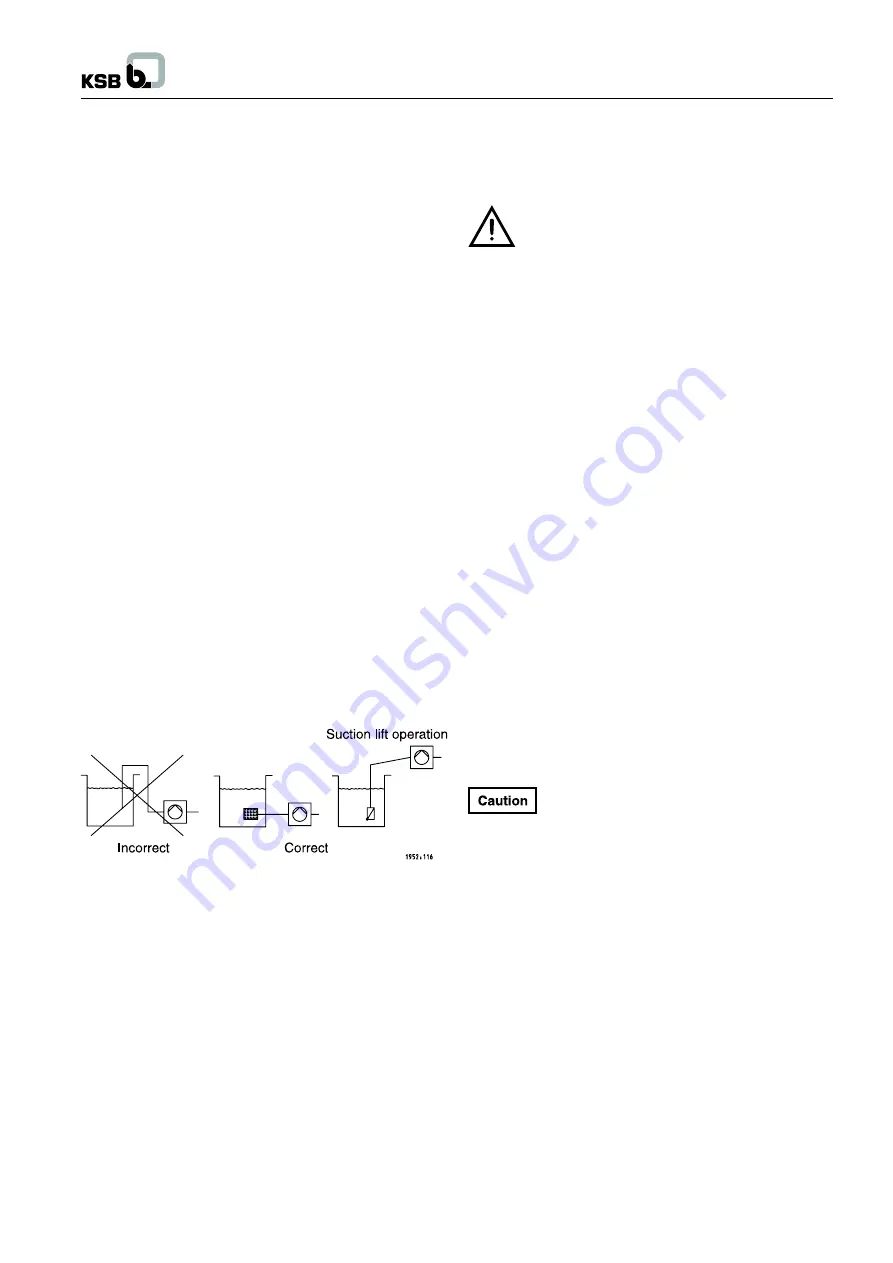
moviBOOST VP
5
Installation at site
5.1
Readiness for operation
The owner or the owner’s representative must report the unit’s
readiness for operation to the responsible authorities (normally
either the water company or the Trade Inspection Office). Prior
to commissioning, the installation contractor must demonstrate
conclusively that the installation requirements have been
complied with.
The power supply line must be installed / connected by a duly
authorised company.
5.2
Installation and location
The moviBOOST must be located either in the technical
equipment room or in a well-ventilated, frost-free, lockable
room used for no other purpose. No harmful gases are allowed
to enter the place of installation. An adequately sized drain
connection (leading to a sewer or equivalent) must be provided.
The unit is designed for a maximum ambient temperature of
0
0
C to +40
0
C at a relative humidity of 50%.
moviBOOST units should not be installed next to sleeping or
living quarters.
Thanks to the anti-vibration mounts, the moviBOOST VP unit
is adequately insulated to prevent transmission of solid-borne
noise.
5.3
Piping
All piping must be installed without transmitting any stresses
or strains. The use of length-limited expansion joints is
advisable (see Accessories).
The formation of air pockets must be avoided. For suction lift
operation, the suction side piping must be laid with a
continuously rising slope.
5.4
Foundation
The package unit is designed for installation on a level
concrete floor. Its anti-vibration pads provide adequate
insulation against solid-borne noise.
5.5
Location
Prior to installing the unit, remove the packaging.
Connect the unit’s inlet and discharge pressure lines with the
corresponding distribution lines.
In order to avoid transmission of piping forces onto the system
and transmission of solid-borne noise, we recommend
installing length-limited expansion joints.
The unit must be accessible to allow maintenance and repair
work.
5.6
Installing a pressure reducer
A length of approximately 600 mm must be provided on the
inlet pressure side to accommodate a pressure reducer, if
necessary.
A pressure reducer must be installed if the inlet
pressure fluctuation is so high that the PBU must be
stopped or if the total system pressure (inlet pressure
plus shut-off head) exceeds the design pressure.
The maximum pump discharge pressure at zero flow point is
reached in manual mode.
For the pressure reducer to function properly, there must be a
minimum pressure gradient of 5 m. The pressure downstream
of the pressure reducer (downstream pressure) is the basic
parameter for defining the pump head.
Example :
The inlet pressure fluctuates between 4 and 8 bar. A pressure
reducer is needed upstream of the unit on the inlet pressure
side.
Min. inlet pressure (H
vor
) = 4 bar
Minimum pressure gradient = 0.5 bar
Downstream pressure = 3.5 bar
5.7
Location and installation of unpressurised
inlet tanks
5.7.1 Location
Inlet tanks may be installed in the same location as the
pressure boosting unit. Installation and location are governed
by the rules applicable to the pressure boosting unit (see 5.2).
5.7.2 Installation
The closed PE inlet tank (under atmospheric pressure)
available as an accessory must be installed as described in
the installation instructions supplied with the tank.
Mechanical and electrical installation of the tank must be
completed prior to commissioning of the unit.
Clean the tank before filling it.
5.8
Valves and fittings
All other valves and fittings in the service pipes, e.g. gate
valves, water meters and non-return valves must be sized in
accordance with the data provided by the responsible water
company.
5.9
Noise characteristics
moviBOOST VP units are available with different pump models
in variable numbers.
Therefore, the total sound pressure level in dB(A) needs to be
calculated.
For the noise level of the individual pumps refer to the pumps
Operating Instructions.
5
Содержание moviBOOST VP
Страница 1: ......
Страница 12: ...moviBOOST VP 7 5 2 Menu structure Main menu KSB logo actual value display 10 ...
Страница 14: ...moviBOOST VP 7 7 Parameter list 12 ...
Страница 15: ...moviBOOST VP 13 ...
Страница 16: ...moviBOOST VP 14 ...
Страница 17: ...moviBOOST VP 15 ...
Страница 18: ...moviBOOST VP 16 ...
Страница 19: ...moviBOOST VP 17 ...
Страница 23: ...moviBOOST VP 21 15 Electrical performance data ...
Страница 24: ...moviBOOST VP 16 Shutoff head 22 ...
Страница 29: ...moviBOOST VP NOTES ...
Страница 30: ......