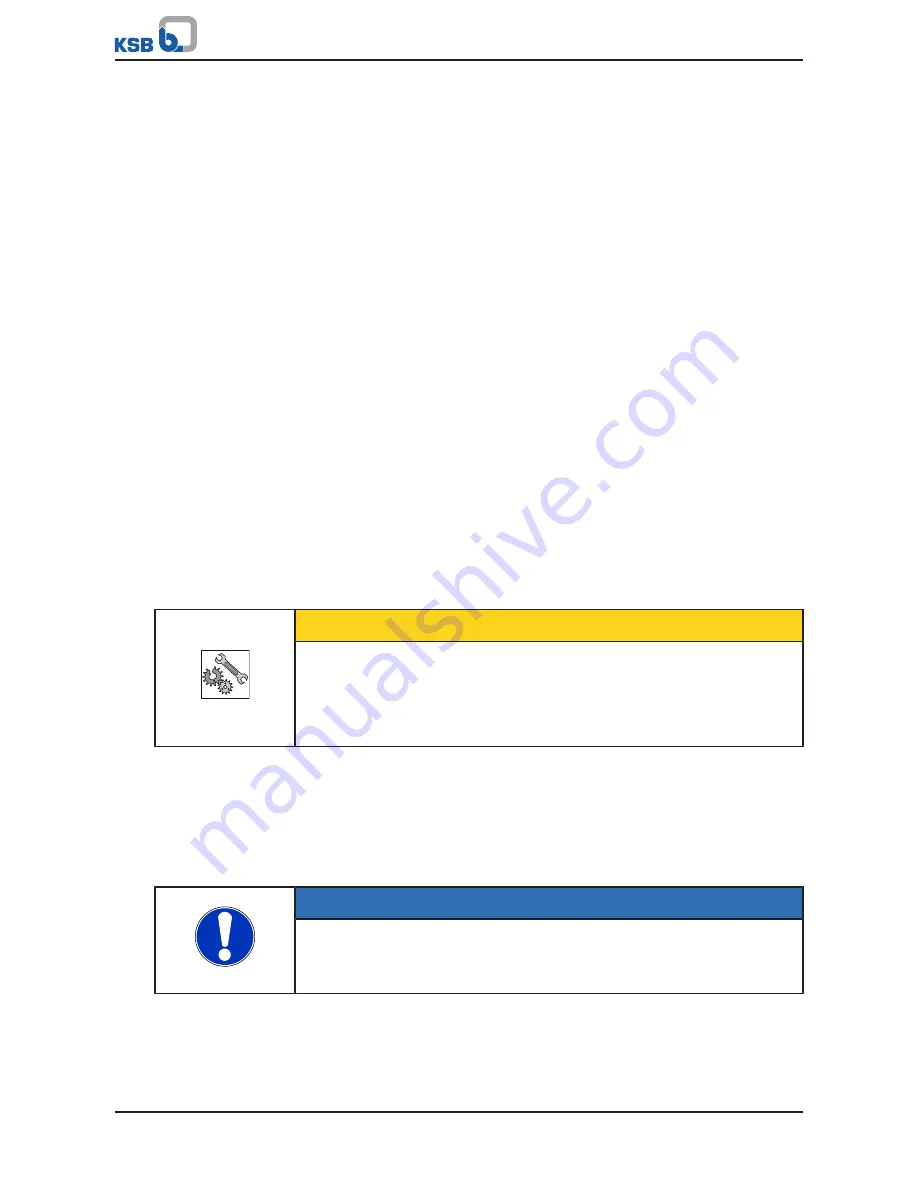
6 Commissioning/Start-up/Shutdown
26 of 52
Etaline-R
6 Commissioning/Start-up/Shutdown
6.1 Commissioning/Start-up
6.1.1 Prerequisites for commissioning/start-up
Before commissioning/starting up the pump set, make sure that the following
conditions are met:
▪
The pump set has been mechanically connected as specified.
▪
The pump set has been properly connected to the power supply and is equipped
with all protection devices.
▪
The pump has been primed with the fluid to be handled. The pump has been
vented.
▪
The direction of rotation has been checked.
▪
All auxiliary connections required are connected and operational.
▪
The lubricants have been checked.
(
ð
Section 6.1.2, Page 26)
▪
After prolonged shutdown of the pump (set), the activities required for returning
the equipment to service have been carried out.
(
ð
Section 6.4, Page 30)
6.1.2 Filling in lubricants
Grease-lubricated bearings have been packed with grease at the factory.
6.1.3 Checking the shaft seal
Mechanical seal
The mechanical seal only leaks slightly or invisibly (as vapour) during operation.
Mechanical seals are maintenance-free.
6.1.4 Priming and venting the pump
CAUTION
Increased wear due to dry running
Damage to the pump set!
▷
Never operate the pump set without liquid fill.
▷
Never close the shut-off element in the suction line and/or supply line during
pump operation.
1.
Vent the pump and suction line and prime both with the fluid to be handled.
Connections 5B and 6D can be used for venting (see drawing of auxiliary
connections).
2.
Fully open the shut-off element in the suction line.
3.
Fully open all auxiliary feed lines (barrier fluid, flushing liquid, etc), if applicable.
4.
Open the shut-off element, if any, in the vacuum balance line and close the
vacuum-tight shut-off element, if any.
(
ð
Section 5.4.3, Page 22)
NOTE
For design-inherent reasons some unfilled volume in the hydraulic system cannot be
excluded after the pump has been primed for commissioning/start-up. However,
once the motor is started up the pumping effect will immediately fill this volume
with the fluid handled.