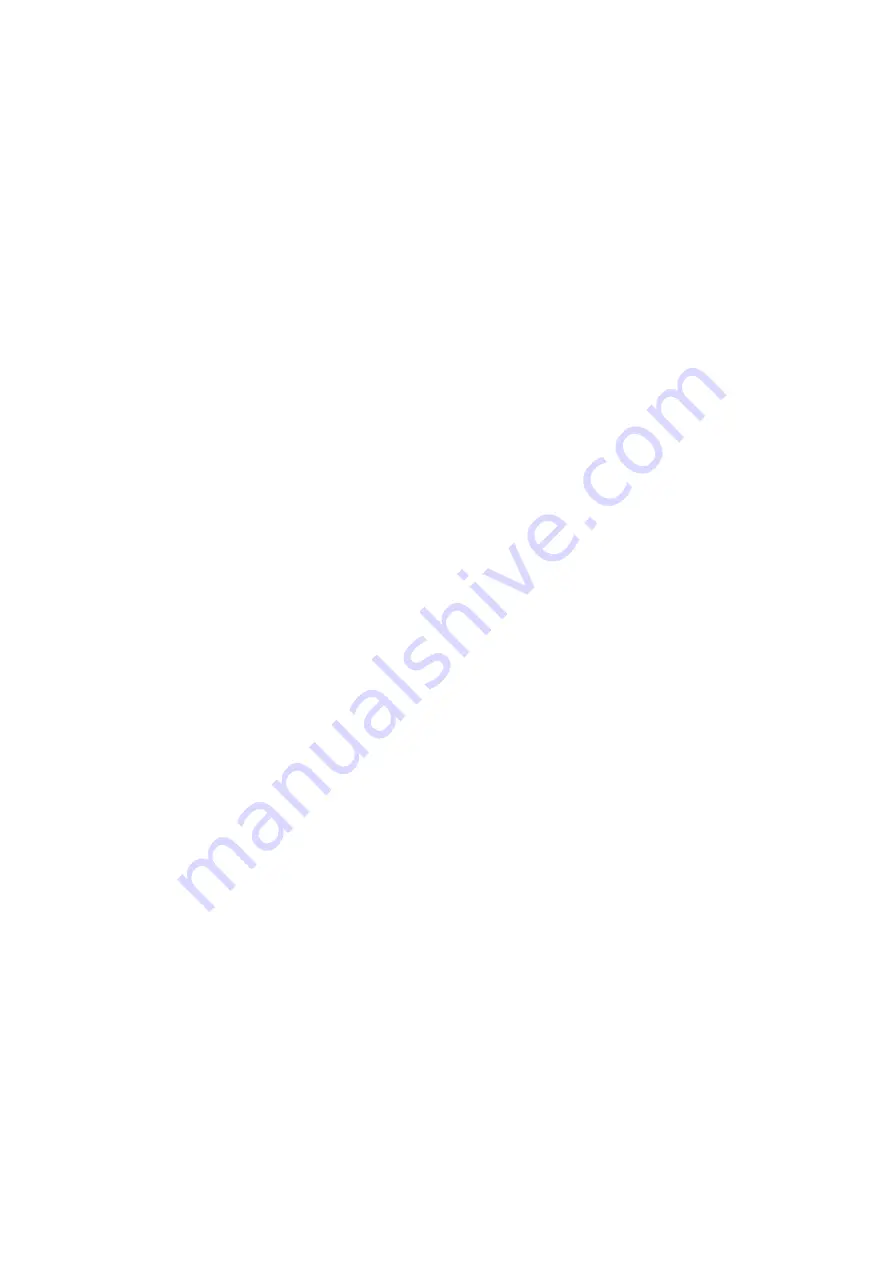
3.12
Once this has all hardened, the tail unit is taken off the building board and the supporting feet are re-
moved. They can be snapped off and subsequently ground flat.
3.13
The main spars G-05 and the two-layered padding H-12 are stuck in, then the underside is ground flat.
3.14
Starting from the screw board of the underside, drill through the upper panelling. The borehole in the
panelling must now be filed to the dimensions of the hole in the doubler H-09.
3.15
The panelling parts H-13 and H-14 are stuck together again – exactly as with the upper panelling H-
10/H-11 – and then stuck onto the framework. They are pressed on with a small force. A layer of waste
wood must be placed under the tailplane so that it does not twist.
3.16
The nose board is ground flush with the panelling, and then the leading edges H-15 are stuck on. Be
very careful when grinding into profile shape, as the panelling can be penetrated very quickly.
3.17
Now the ribs H-04 are ground flush with the panelling and the wing tips H-16 are stuck on and ground
so that they are round after hardening.
3.18
Finally, the nose is ground flat in the middle of the tailplane, as shown in the photo. The front edge of
the screw board is decisive here.
3.19
In addition, the trailing edge should be ground flush with the panelling and wing tips. Then the tailplane
is finished.
3.20
Now we come to the elevator:
No.
Designation
Quantity Material
Dimensions
Comments/plate
H-18
Leading edge, inside
1
Balsa
3 mm
Laser-cut part 22
H-19
Trailing edge
2
Balsa
3 mm
Laser-cut part 22
H-20
Inner part
2
Balsa
3 mm
Laser-cut part 21
H-21
Wing tip
2
Balsa
3 mm
Laser-cut part 22
H-22
Rib bars
2
Balsa
2 x 8 x 450 mm Square strip
H-23
Inner part padding
4
Balsa
3 mm
Laser-cut part 21/22
H-24
Wing tip padding
4
Balsa
3 mm
Laser-cut part 21/22
H-25
Rudder connection
1
Steel wire
3 x 40 mm
Finished part
H-26
Rudder horn
1
Plywood
1 mm
Laser-cut part 7
H-27
Hinge
6
Fleece
-
Cut to size
3.21
The blades of the elevator are constructed on the piece and only removed upon completion. After cov-
ering, the blades are connected with the steel wire H-24 – more on this later.
3.22
To prepare for constructing the elevator, the triangular inner parts from H-19 (middle layer) and H-22
are stuck together in three layers. The wing tips from H-20 (middle layer) and H-23 are also stuck to-
gether. Make sure that no glue clogs up the small recesses.
3.23
Parts H-17, inner parts H-19/H-22, wing tips H-20/H-23 and trailing edge H-18 are laid flat and stuck
together. We recommend first putting everything together when dry to check the alignment and fit.
3.24
The sides of the fuselage H-20 are sawn off the square strip and pressed in. There are corresponding
cut-outs in the trailing edge, which are used to locate the position on the leading edge. However, take
care when inserting the bars so that the leading edges and trailing edges do not buckle. These must
be glued using white glue again.
3.25
The elevator is now removed for the grinding process. The length and depth of the blades are ground
into a conical shape. The thickness of the trailing edge should still be at least 2 mm. The tapering in
the longitudinal direction is determined by the leading edge. The plane of the brown edge can be used
to check how much further you can grind.
3.26
The leading edge is also bevelled on both sides. The hinge slots are used for the orientation of the
centre line.
Содержание Klemm L25-D
Страница 24: ......
Страница 25: ......
Страница 53: ...TF 04 TF 04 10280 Klemm 25 Platte 18 H 11 H 14 10280 Klemm 25 Platte 19 H 10 H 13 10280 Klemm 25 Platte 20 ...