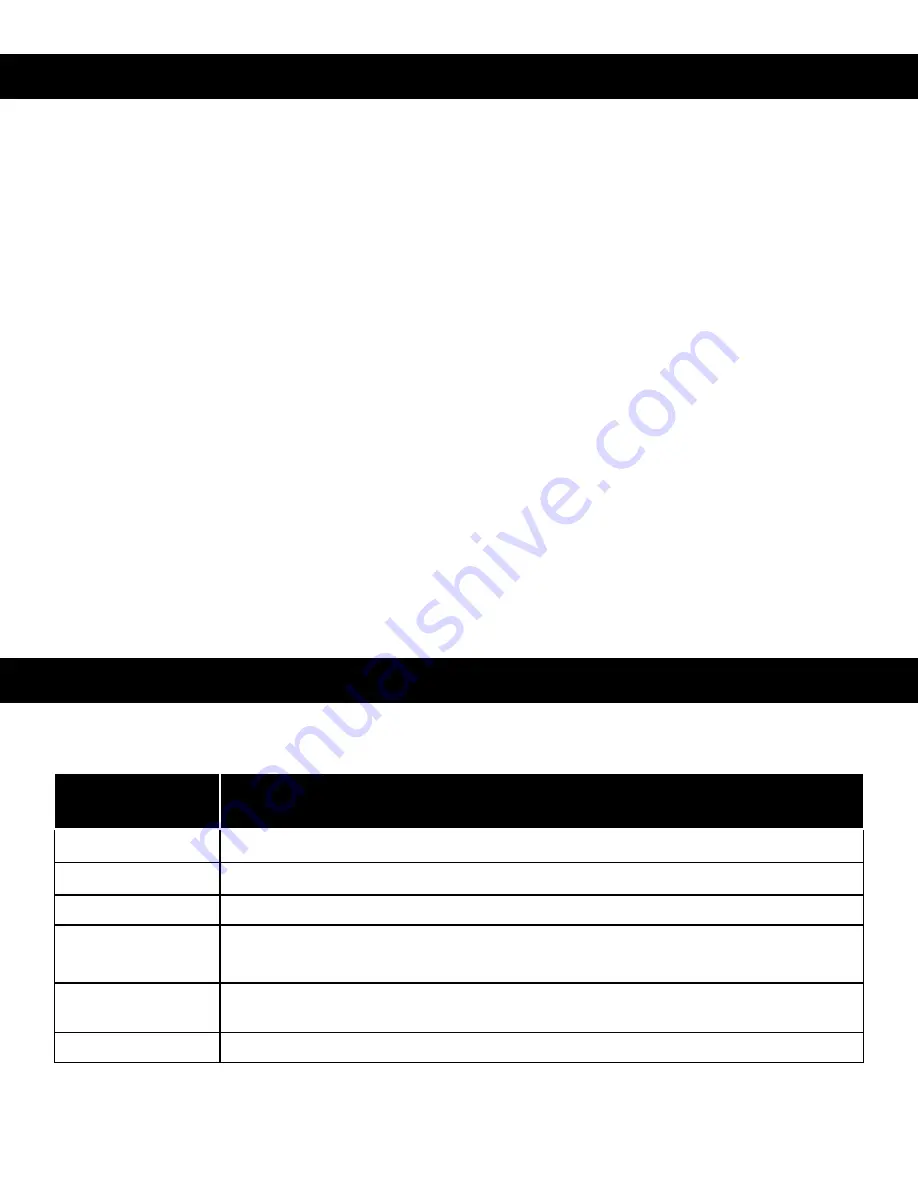
Use a streak free stainless steal cleaner/polish to clean the outside of the NOMAD to keep it looking shiny and new.
Only use approved cleaners to clean and sanitize your product lines.
APPROVED CLEANERS:
•
Sodium Percarbonate (CL09) / Oxyclean
•
PBW (CL25)
•
Saniclean (CL27)
•
Star San (CL26)
Line Cleaning
Always clean between every keg use. Cleaning your system will ensure your taps, lines, and faucets are clean, resulting
in a better-tasting beer.
REQUIRED:
•
Cleaning Pump
•
Faucet Wrench
•
Beer Line Cleaner
•
Tap & Faucet Brush
•
Water
•
Bucket
•
Large Bowl
1.
Disconnect your ball lock QDs or keg couplers from your kegs. Disconnect the EVABarrier tubing from your
fittings and run your beer lines from the Duotight bulkheads on the NOMAD into a bucket.
2.
Remove the beer faucets from the front of the NOMAD. Fully disassemble the faucets to the point that the
internal shuttle can slide out. Place these parts in a bowl with 2 cups of warm water and a 1/4 teaspoon of Beer Line
Cleaner.
3.
Attach your cleaning pump to the faucet draft shank. Pump cleaning solution through the line. For best results,
allow the solution to sit in the lines for 10-15 minutes, then pump through. Repeat this step for the other line.
4.
Use a faucet brush to scrub the faucet body and all parts, then rinse with clean water. Reassemble the faucet, hand
tighten the parts but leave them loose enough so that they move freely. Attach the faucets back onto the shanks
using a draft wrench but do not over tighten.
5.
Hook up a fresh keg and enjoy!
CLEANING AND MAINTENANCE
The power button is a multi-purpose button both turning on the main power to the compressor but also the illumination
on the button will flash to indicate fault codes if an error has been triggered.
NUMBER OF FLASHES
FAULT TYPE
1
Voltage Fault (The input voltage is beyond the setting range)
2
Fan Fault Current (The fan’s output current is more than 1A peak)
3
Compressor Start Fault (The rotor is blocked or the system pressure is too high (above 6 bar)
4
Minimum Motor Speed Fault (If the compressor is too highly loaded and cannot maintain minimum rotor
speed this will be triggered, also if the controller cannot sense rotor speed this will also trigger this fault code)
5
Thermal Fault of Electronic Unit (If the load on the compressor is too high or if the ambient temperature is
too high the controller will not run until it cools down)
6
Controller Hardware Fault (Controller detects abnormal parameters)
FAULT CODES
7