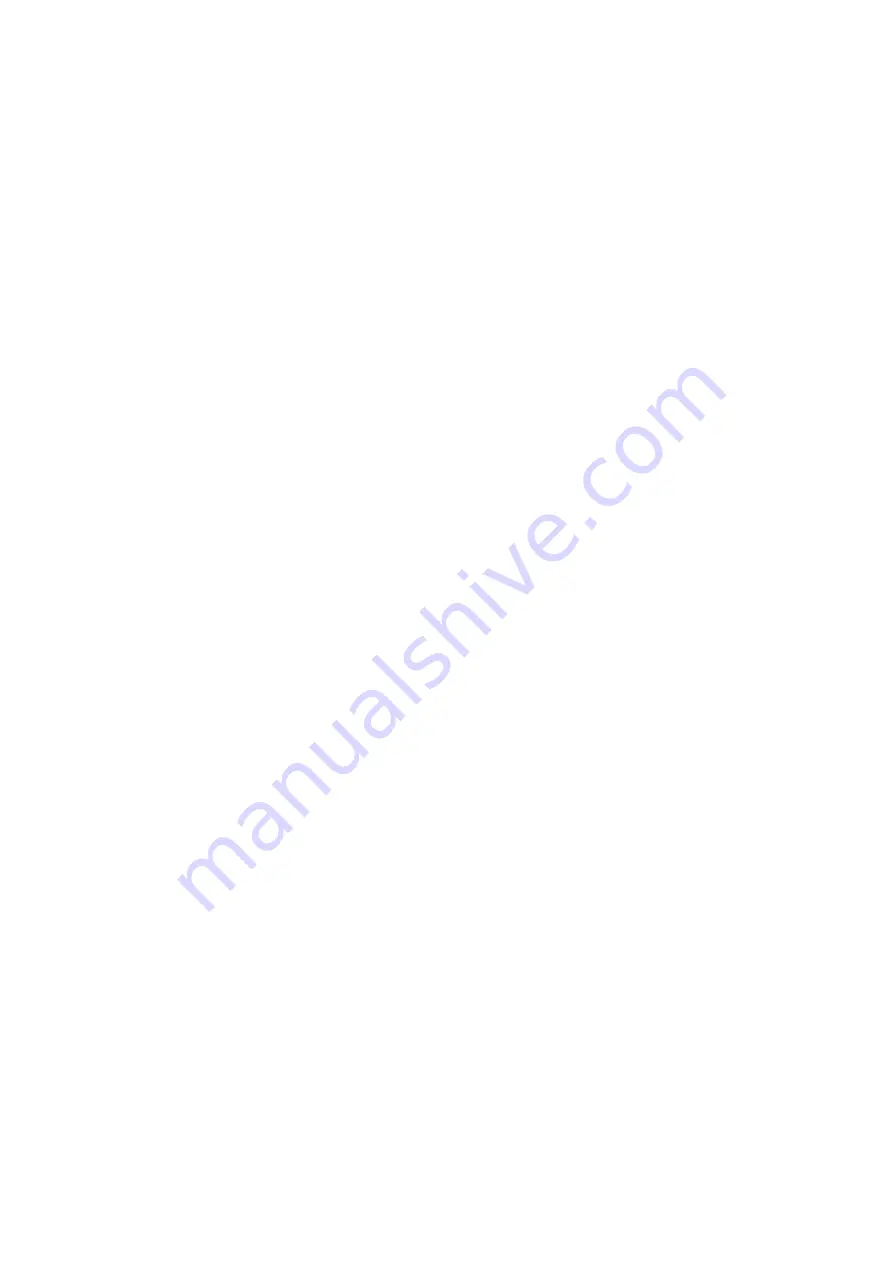
A1 Port
- To arm cylinder (Head side)
A2 Port
- To swing motor (A Port)
A3 Port
- To swivel joint (D Port)
A4 Port
- To swivel joint (C Port)
A5 Port
- To boom cylinder (Bottom side)
A6 Port
- To bucket cylinder (Bottom side)
A7 Port
- To swivel joint (F Port)
A8 Port
- To boom swing cylinder (Head side)
A9 Port
- To attachment
B1 Port
- To arm cylinder (Bottom side)
B2 Port
- To swing motor (B Port)
B3 Port
- To swivel joint (B Port)
B4 Port
- To swivel joint (A Port)
B5 Port
- To boom cylinder (Head side)
B6 Port
- To bucket cylinder (Head side)
B7 Port
- To swivel joint (E Port)
B8 Port
- To boom swing cylinder (Bottom side)
C Port
- To oil cooler
P Port
- From hydraulic pump (P Port)
Pa1 Port
- From L.H. PPC valve (4 Port)
Pa2 Port
- From L.H. PPC valve (1 Port)
Pa5 Port
- From R.H. PPC valve (2 Port)
Pa6 Port
- From R.H. PPC valve (1 Port)
Pa9 Port
- From attachment PPC valve
Pb1 Port
- From L.H. PPC valve (2 Port)
Pb2 Port
- From L.H. PPC valve (3 Port)
Pb5 Port
- From R.H. PPC valve (4 Port)
Pb6 Port
- From R.H. PPC valve (3 Port)
Pi1 Port
- From hydraulic pump (P3 Port)
Pi2 Port
- To ST1 solenoid valve (P Port)
P2 Port
- From hydraulic pump (P2 Port)
T Port
- To hydraulic tank
TS Port
- To hydraulic tank
10-35
PC12R-8 PC15R-8
Содержание PC12R-8 MISTRAL
Страница 1: ......
Страница 2: ...40 28 PC15R 8 ...
Страница 4: ...00 2 PC12R 8 PC15R 8 ...
Страница 17: ...GROUP 10 ...
Страница 18: ...40 28 PC15R 8 ...
Страница 30: ...10 12 PC12R 8 PC15R 8 PAGE INTENTIONALLY LEFT BLANK ...
Страница 32: ...10 14 PC12R 8 PC15R 8 PAGE INTENTIONALLY LEFT BLANK ...
Страница 34: ...10 16 PC12R 8 PC15R 8 PAGE INTENTIONALLY LEFT BLANK ...
Страница 36: ...10 18 PC12R 8 PC15R 8 PAGE INTENTIONALLY LEFT BLANK ...
Страница 38: ...10 20 PC12R 8 PC15R 8 PAGE INTENTIONALLY LEFT BLANK ...
Страница 40: ...10 22 PC12R 8 PC15R 8 PAGE INTENTIONALLY LEFT BLANK ...
Страница 42: ...10 24 PC12R 8 PC15R 8 PAGE INTENTIONALLY LEFT BLANK ...
Страница 44: ...10 26 PC12R 8 PC15R 8 PAGE INTENTIONALLY LEFT BLANK ...
Страница 79: ...10 61 PC12R 8 PC15R 8 PAGE INTENTIONALLY LEFT BLANK ...
Страница 130: ...10 112 PC12R 8 PC15R 8 PAGE INTENTIONALLY LEFT BLANK ...
Страница 132: ......
Страница 133: ...GROUP 20 ...
Страница 134: ...40 28 PC15R 8 ...
Страница 149: ...PC15R 8 Standard value Permissible value Max 20 Max 30 2 Max 5 2 Max 5 2 Max 5 FOR THE MACHINE 20 15 PC12R 8 PC15R 8 ...
Страница 158: ...20 24 PC12R 8 PC15R 8 PAGE INTENTIONALLY LEFT BLANK ...
Страница 198: ......
Страница 199: ...GROUP 30 ...
Страница 200: ...40 28 PC15R 8 ...
Страница 283: ...GROUP 40 ...
Страница 284: ...40 28 PC15R 8 ...
Страница 295: ...HYDRAULIC PUMP PC12R 8 40 11 PC12R 8 PC15R 8 RKP00910 Z Vista Z 68 6 Nm 7 kgm 48 Nm 4 9 kgm View Z ...
Страница 298: ...40 14 PC12R 8 PC15R 8 RKP00131 Sezione A A 44 1w4 9 Nm 4 5w0 5 kgm 44 1w4 9 Nm 4 5w0 5 kgm Section A A ...
Страница 304: ...40 20 PC12R 8 PC15R 8 RKP00201 Sezione A A 44 1w4 9 Nm 4 5w0 5 kgm 44 1w4 9 Nm 4 5w0 5 kgm Section A A ...
Страница 317: ...40 33 PC12R 8 PC15R 8 PAGE INTENTIONALLY LEFT BLANK ...
Страница 324: ......