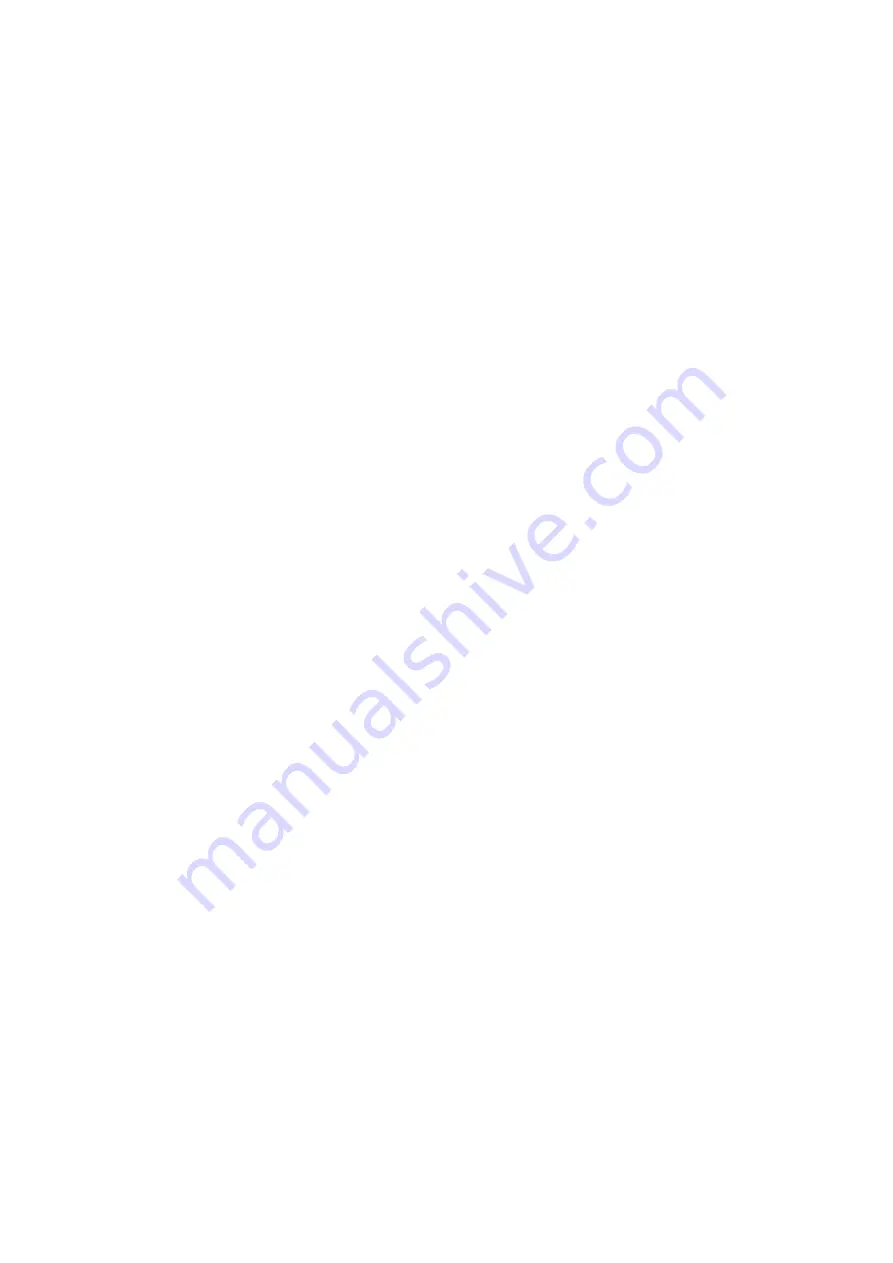
LUBRICANTS, COOLANT AND FILTERS
162
4.2.1.6 OIL AND FUEL STORAGE
• Keep indoors to prevent any water, dirt, or other impurities from getting in.
• When keeping drum cans for a long period, put the drum on its side so that the filler port of the drums is at the
side to prevent moisture from being sucked in.
If drums have to be stored outside, cover them with a waterproof sheet or take other measures to protect them.
• To prevent any change in quality during long-term storage, be sure to use in the order of first in - first out (use the
oldest oil or fuel first).
4.2.1.7 FILTERS
• Filters are extremely important safety parts. They prevent impurities in the fuel and air circuits from entering im-
portant equipment and causing problems.
Replace all filters periodically. For details, see the Operation and Maintenance Manual.
However, when working in severe conditions, replace the filters at shorter intervals according to the oil and fuel
(sulfur content) being used.
• Never try to clean the filters (cartridge type) and use them again. Always replace with new filters.
• When replacing oil filters, check if any metal particles are affixed to the old filter. If any metal particles are found,
contact your Komatsu Dealer.
• Do not open packs of spare filters until just before they are to be used.
• Always use Komatsu genuine filters.
Содержание 15001
Страница 2: ......
Страница 18: ...16 PAGE INTENTIONALLY LEFT BLANK ...
Страница 19: ...SAFETY AND ACCIDENT PREVENTION 17 ...
Страница 54: ...52 PAGE INTENTIONALLY LEFT BLANK ...
Страница 55: ...THE MACHINE AND ITS OPERATIONS 53 ...
Страница 156: ...154 PAGE INTENTIONALLY LEFT BLANK ...
Страница 157: ...MAINTENANCE 155 ...
Страница 207: ...TECHNICAL SPECIFICATIONS 205 ...
Страница 216: ...LIFTING CAPACITIES 214 PAGE INTENTIONALLY LEFT BLANK ...
Страница 217: ...AUTHORISED OPTIONAL EQUIPMENT 215 ...
Страница 232: ...230 PAGE INTENTIONALLY LEFT BLANK ...
Страница 233: ......
Страница 234: ... 2005 KOMATSU UTILITY EUROPE S p A All Rights Reserved Printed in Europe ...