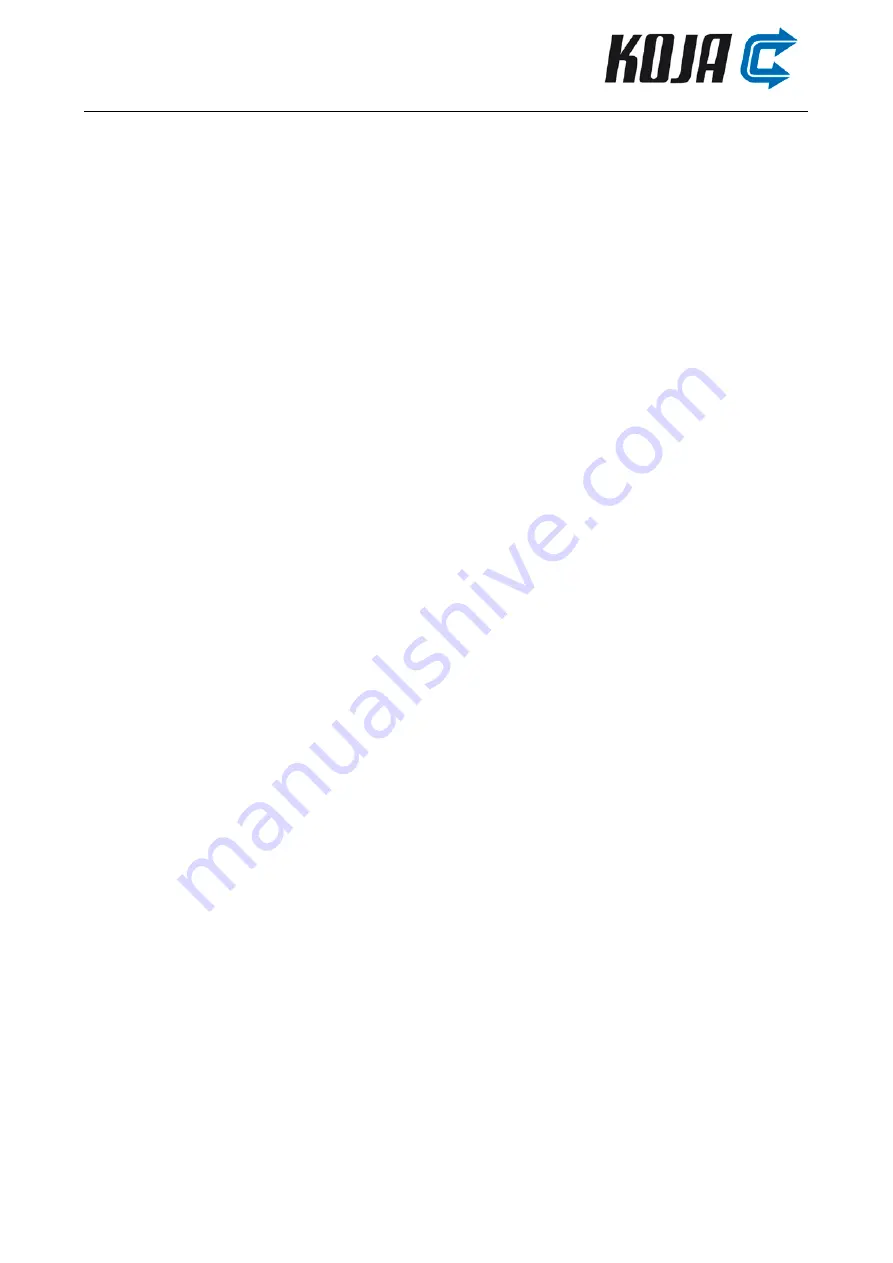
FUTURE® S AIR HANDLING UNIT
OPERATION AND MAINTENANCE
INSTRUCTIONS
15 December 2020
Ver 1.7 (We reserve the right to changes without prior notice)
32
8.3 Fans
Supply and exhaust fans are equipped with EC motors. The fans are controlled with a DI start signal and 0…10
V control signal. The fan also has a K1 relay that provides status or alarm data, depending on the relay
programming. In factory delivery, the power supply to the fans is ready-connected to the unit switchboard
and the control points are either ready-connected to the FxVent controller or to the unit switchboard’s
terminal blocks, depending on the delivery content. Electrical and automation connection diagrams are
presented in further detail in Koja’s connection diagrams and the fans’ K values are presented in the technical
printout.
8.4 Temperature sensors
In standard delivery, the unit includes 5 pcs NTC10 air temperature sensors and NTC10 anti-freeze sensor for
the heating coil. The temperature sensors are installed and wired at the factory.
The anti-freeze sensor of the post-heating coil is a fast time constant NTC10k rod sensor, measuring the
temperature of the liquid returning from the coil. The sensor has its own installation fitting near the coil
return water inlet. The FxVent controller monitors the measurement and reacts to the freezing risk by
opening the coil’s control valve as the first step and stopping the ventilation unit as the second step, thereby
creating a class A freezing hazard alarm. The freezing hazard alarm is always acknowledged by the user. The
limit value of the freezing hazard can be set as desired with the controller.
If the unit is delivered without the Koja controller, the control automation must always monitor the
measurement of the anti-freeze sensor and act in such a way that in the event of a freezing hazard, coil
freezing is prevented by taking the necessary measures.
8.5 Pressure transmitters
In standard delivery, the unit includes pressure difference transmitter for fresh and exhaust air filters and a
pressure difference transmitter for heat recovery exhaust air. Scalable pressure limits are set for the
measurement of pressure difference according to the operating level of the fans.
Fan air flow measurement and constant pressure controller are available as accessories. Air flow
measurement includes air volume transmitters for monitoring the supply and exhaust air flow. The constant
pressure controller includes pressure transmitters for monitoring the supply and exhaust duct pressure.
All pressure transmitters are installed, wired to the unit’s switchboard and hosed to the pressure measuring
points at the factory. Pressure transmitters require 24 Vac or 24 Vdc supply voltage to operate. When
commissioning transmitters, check the pressure measuring range:
- In pressure difference transmitters, ensure the pressure measuring range set for the transmitter with
jumpers, according to which the transmitter scales the output 0…10 V voltage signal.
The air volume transmitters of supply and extract fans must have the following settings:
- Manufacturer -> Common probe
- Formula unit m
3
/h
- K value (check the correct K value of the fan in the Koja technical printout)
- Flow output scaling to 0...10 V to match the automation settings. (Koja S500 and 900
0…1000 l/s and S1200 and S1800 0…2000 l/s)
The air volume transmitter sends either a pressure or air volume signal Vout or Pout according to automation
needs. As a Koja factory standard, Vout is set as flow signals and in l/s. In connection of commissioning, it
must be ensured that the flow unit and output scaling used by the transmitter correspond to the automation
settings.
Содержание Future S
Страница 2: ......