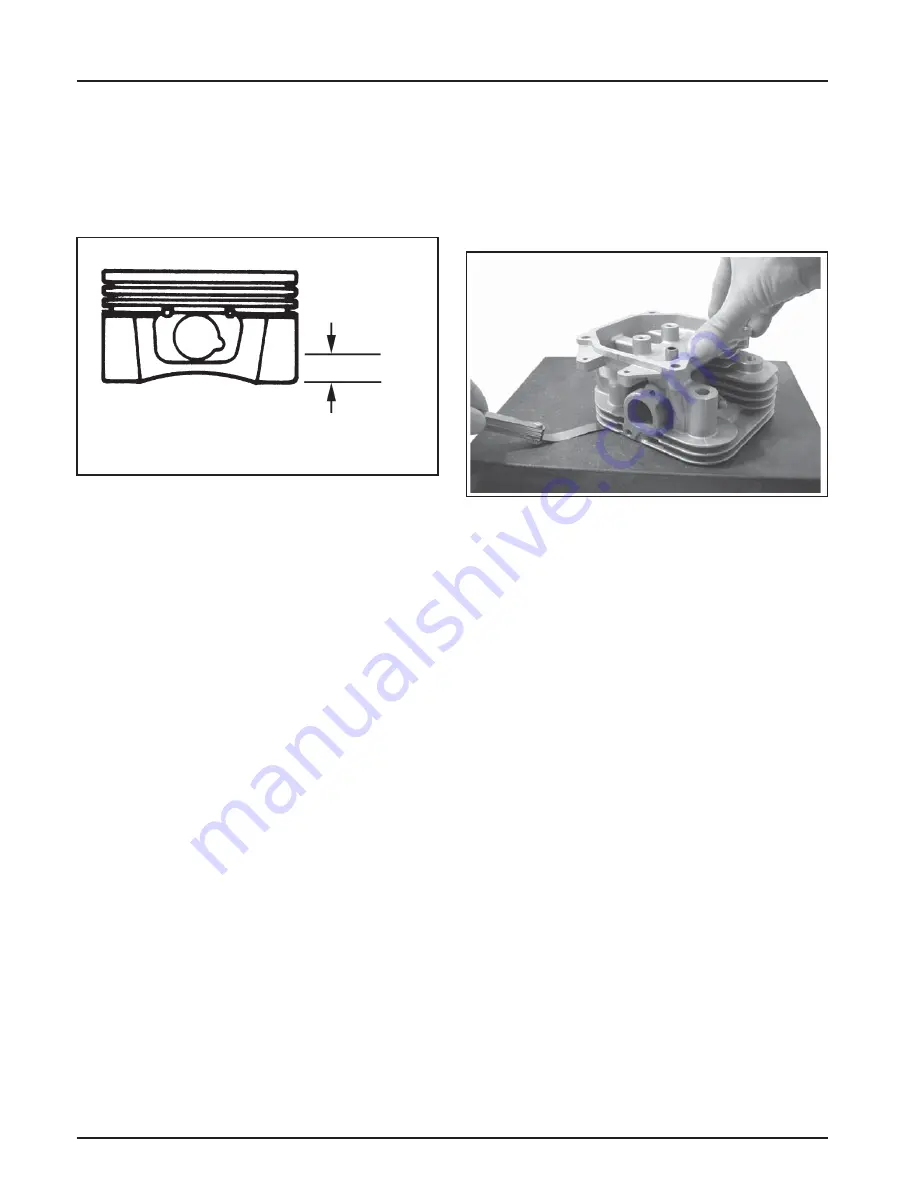
9.4
Section 9
Inspection and Reconditioning
6 mm (0.24 in.)
Measure 6 mm above the
Bottom of Piston Skirt at
Right Angles to Piston Pin
Use the following procedure to accurately measure
the piston-to-bore clearance:
1. Use a micrometer and measure the diameter of
the piston
6 mm (0.24 in.)
above the bo
tt
om of the
piston skirt and perpendicular to the piston pin.
See Figure 9-4.
Figure 9-4. Measuring Piston Diameter.
2. Use an inside micrometer, telescoping gauge, or
bore gauge and measure the cylinder bore. Take
the measurement approximately
63.5 mm
(2.5 in.)
below the top of the bore and
perpendicular to the piston pin.
3. Piston-to-bore clearance is the di
ff
erence between
the bore diameter and the piston diameter (Step 2
minus Step 1).
Flywheel
Inspection
Inspect the
fl
ywheel for cracks and the
fl
ywheel
keyway for damage. Replace the
fl
ywheel if it is
cracked. Replace the
fl
ywheel, the cranksha
ft
, and
the key if
fl
ywheel key is sheared or the keyway is
damaged.
Inspect the ring gear for cracks or damage. Kohler
does not provide the ring gear as a serviceable part.
Replace the
fl
ywheel if the ring gear is damaged.
Cylinder Head and Valves
Inspection and Service
A
ft
er cleaning, check the
fl
atness of the cylinder head
and the corresponding top surface of the crankcase,
using a surface plate or piece of glass and feeler gauge
as shown in Figure 9-5. The maximum allowable out
of
fl
atness is
0.076 mm (0.003 in.)
.
Figure 9-5. Checking Cylinder Head Flatness.
Carefully inspect the valve mechanism parts. Inspect
the valve springs and related hardware for excessive
wear or distortion. Check the valves and valve seat
area or inserts for evidence of deep pi
tt
ing, cracks,
or distortion. Check clearance of the valve stems
in the guides. See Figure 9-6 for valve details and
speci
fi
cations.
Содержание Command PRO CH749
Страница 1: ...SERVICE MANUAL ECH630 ECH749 HORIZONTAL CRANKSHAFT ...
Страница 2: ......
Страница 4: ......
Страница 76: ...6 6 Section 6 Lubrication System ...
Страница 94: ...7 18 Section 7 Electrical System and Components ...
Страница 112: ...8 18 Section 8 Disassembly ...
Страница 126: ...9 14 Section 9 Inspection and Reconditioning ...
Страница 153: ......