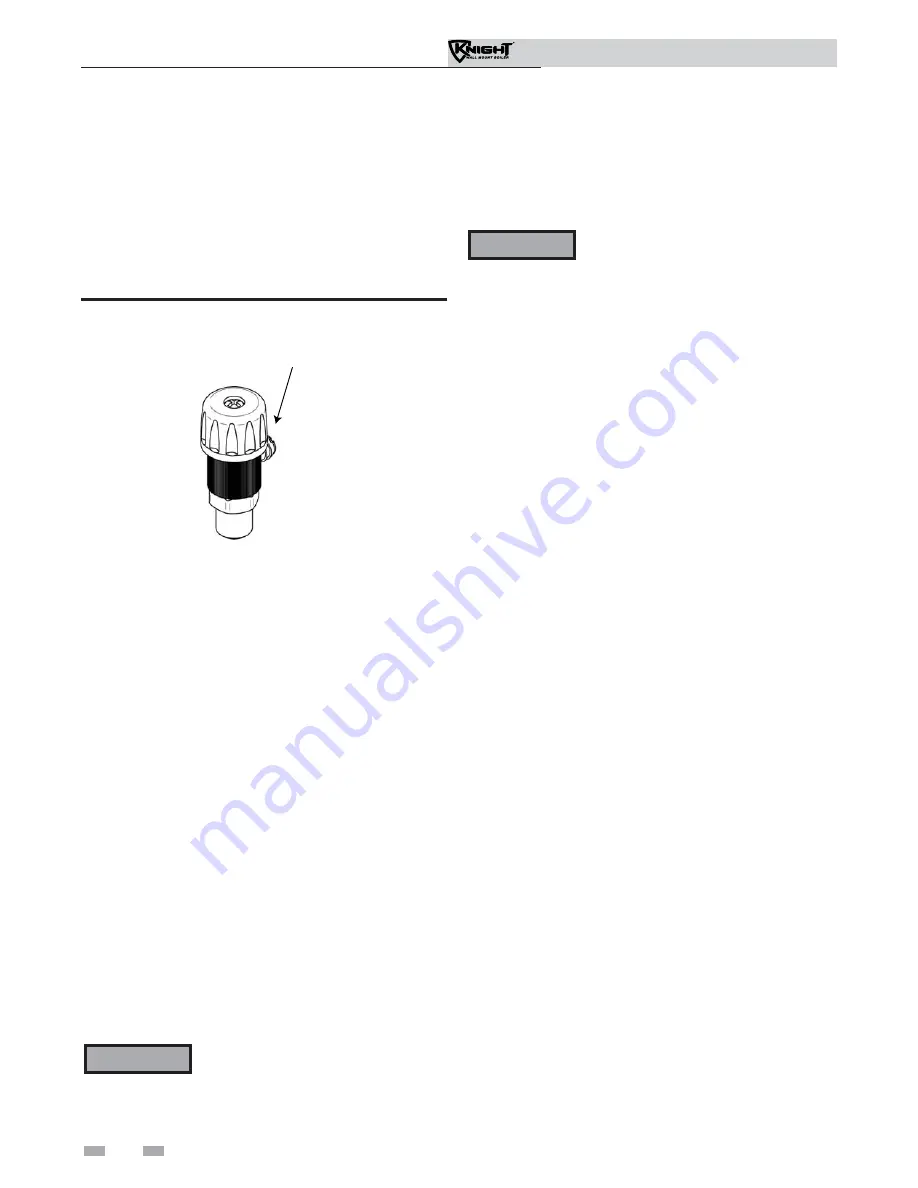
User’s Information Manual
2
Maintenance schedule
8
WARNING
Have leaks fixed at once by a qualified
service technician. Failure to comply could
result in severe personal injury, death, or
substantial property damage.
2. Read the boiler pressure/temperature gauge to make
sure the system is pressurized. Lift the relief valve
top lever slightly, allowing water to relieve through
the valve and discharge piping.
3. If water flows freely, release the lever and allow the valve
to seat. Watch the end of the relief valve discharge pipe
to ensure that the valve does not weep after the line has
had time to drain. If the valve weeps, lift the seat again to
attempt to clean the valve seat. If the valve continues to
weep afterwards, contact your qualified service
technician to inspect the valve and system.
4. If water does not flow from the valve when you lift the
lever completely, the valve or discharge line may be
blocked. Immediately shut down the boiler, following
the operating instructions on pages 9 and 10 of this
manual. Call your qualified service technician to inspect
the boiler and system.
Shut boiler down (unless boiler is used
for Domestic Water)
1. Follow “To Turn Off Gas to Appliance” on pages 9 and 10
of this manual.
2. Do not drain the system unless exposure to freezing
temperatures will occur.
3. Do not drain the system if it is filled with an antifreeze
solution.
4. DO NOT shut down boilers used for domestic water
heating, they must operate year-round.
3. Replace the front access door.
Test low water cutoff (if installed)
1.
If the system is equipped with a low water cutoff,
test the low water cutoff periodically during the heating
season, following the low water cutoff manufacturer’s
instructions.
Reset button (low water cutoff)
1. Testing the low water cutoff shuts the unit off. Press the
RESET button on the low water cutoff to turn the unit
back
on.
Check boiler piping (gas and water)
1. Remove the boiler front access door and perform a gas
leak inspection per steps 1 through 7 of the Operating
Instructions on pages 9 and 10. If gas odor or leak is
detected, immediately shut down the boiler following the
procedures on pages 9 and 10. Call a qualified service
technician.
2. Visually inspect for leaks around water piping.
Also inspect the circulators, relief valve, and fittings.
Immediately call a qualified service technician to repair
any
leaks.
Check air vents
1. Reference
FIG.
2-3
below.
2. Visually inspect vent to make sure that no leaks are
present.
3. If there is leaking, tighten the pin valve.
4. If the leak continues, replace the air vent.
Figure 2-3 Manual Air Vent
MANUAL
AIR VENT VALVE
Operate relief valve
1. Before proceeding, verify that the relief valve outlet has
been piped to a safe place of discharge, avoiding any
possibility of scalding from hot water.
WARNING
To avoid water damage or scalding due
to valve operation, a metal discharge
line must be connected to the relief
valve outlet and run to a safe place of
disposal. This discharge line must be
installed by a qualified heating installer or
service technician in accordance with the
instructions in the Knight Wall Mount
Installation and Operation Manual. The
discharge line must be terminated so as
to eliminate possibility of severe burns
or property damage should the valve
discharge.