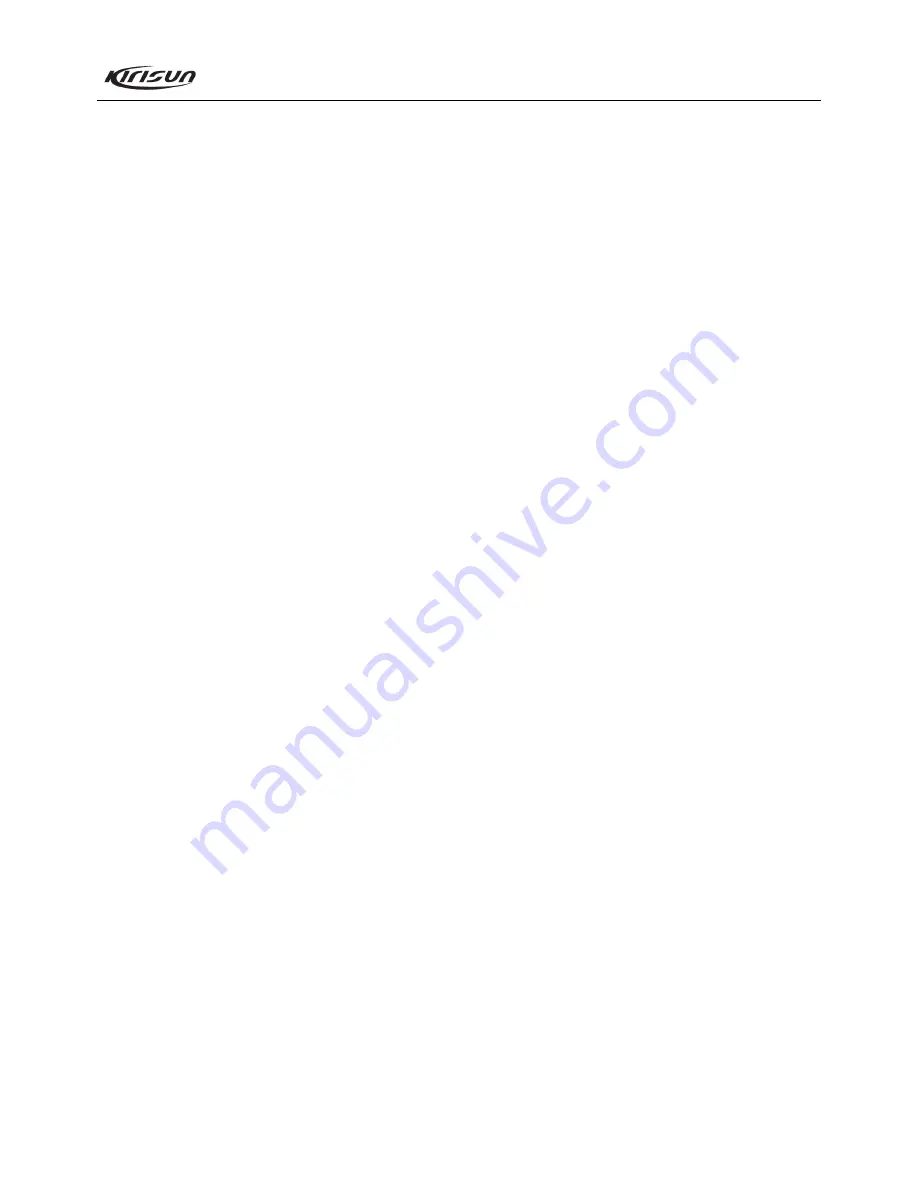
PT6800 Service Manual
5
signal, which is then sent to MCU for processing. The other
branch of the signal is routed to pin23 of IC6. After being
amplified and filtered, the signal is divided into two branches.
One branch (DTMF/2T/5T signals) is output from pin21 of IC6.
The DTMF/2T/5T signals passes through the high pass circuit
consists of Q30, Q31, and other components to remove the
subaudio signal. The DTMF signal goes to IC10 (HT9172
special DTMF decoding chip) to be decoded, and then is sent to
MCU for processing. The 2T/5T signal goes to IC1, where it is
filtered and reshaped, and then is routed to MCU for processing.
The other branch (voice signal) is scrambled, de-emphasized,
and companded, and is output from pin18 of IC6. Then the
resulting signal is input to pin19 of IC6. After being buffered
and amplified, it is then output from pin20 of IC6.
IC13 is a voice memory chip, which is stored with voices of
channel indication etc. Once the rotary encoder is switched, the
speaker will announce the current channel number. User can
press the preprogrammed “Voice Alert” key to repeat the
current channel number.
After the RX audio signal, voice alert signal, 2T/5T/DTMF
signal, alert tone signal, and emergency alarm signal join
together, they are amplified by audio power amplification IC9,
and then drive the speaker.
Impedance of the speaker: 16
Ω
Note:
* None of the terminals of the speaker should be grounded.
* The emergency alarm sound has no volume limit.
4.7 Power Supply
The radio adopts 7.2V battery as power supply. The Tx
power amplification circuit (Q1 and Q3) and the Rx audio
power amplifier (IC9) directly adopts the battery as power
supply. Power of other circuits is supplied by the regulated
voltage (5V).
Q40 and Q45: 5V low dropout, micro-power regulator.
Q43: 5T switch, controlled by MCU.
5T: Supplies power for front end of Tx.
Q39: 5R switch, controlled by MCU.
5R: Supplies power for RF amplifier, mixer, IF processing
unit, and audio signal processing unit etc. of Rx.
Q44: 5C switch, controlled by MCU.
5C: 5V power supply under SAVE control. Supplies power
for frequency synthesizer.
4.8 MCU Unit
MCU unit controls the operation of each unit of the radio so
that all functions can be realized.
Communicate with external PC.
Access the status data of the radio.
Control the PLL to generate Rx and Tx local oscillator
frequencies.
Obtain status parameters of current channel.
Control status of LED indicator.
Control power supply for each unit.
Check the actions of each functional key.
Generate CTCSS signal.
Generate DCS signal.
Generate power control signal.
Perform CTCSS decoding.
Perform DCS decoding.
Test and control the squelch.
Control content of voice alert.
Memory
(E
2
PROM, AT24C256):
The memory is stored with channel data, CTCSS/DCS data,
other data for function setting, and parameter adjusting data of
the radio.
CTCSS/DCS Signal Encoding and Decoding
The CTCSS/DCS signal (output from pin24 and pin28,
PWM wave) generated by MCU is routed to VCO and TCXO
respectively for modulation.
The CTCSS/DCS signal from the receiver is decoded by
MCU. MCU checks if the CTCSS/DCS signal in the receiving
signal matches the preset CTCSS/DCS of the radio, and
determines whether to open the speaker or not.
CTCSS Signal
CTCSS (Continuous Tone Control Squelch System) is a
squelch control system which is modulated on carrier and is
guided by a continuous subaudio signal. If CTCSS is set, the
communication between the transmitting and receiving radios
can be realized only when the two radios has set the same
CTCSS. In doing this, disturbance from other signals can be
avoided.
PT6800 has 39 groups of standard CTCSS frequencies for
your selection. See table 4.1.
CTCSS signal is generated by MCU (PWM waveform), and
is passed through low pass filter consists of RC to remove high
frequency component (above 300Hz). Then the resulting signal
is routed to VCO for modulation.
Table 4.1 CTCSS Frequencies
Содержание PT6800
Страница 28: ...PT6800 Service Manual 27 Figure 3 PT6800 Main Board Top Layer Position Mark Diagram ...
Страница 29: ...PT6800 Service Manual 28 Figure 4 PT6800 Main Board Bottom Layer Position Mark Diagram ...
Страница 30: ...PT6800 Service Manual 29 Figure 5 PT6800 Main Board Top Layer Position Value Diagram ...
Страница 31: ...PT6800 Service Manual 30 Figure 6 PT6800 Main Board Bottom Layer Position Value Diagram ...
Страница 33: ...PT6800 Service Manual 32 Figure 8 PT6800 Key Board Top Layer Position Mark Diagram ...
Страница 34: ...PT6800 Service Manual 33 Figure 9 PT6800 Key Board Bottom Layer Position Mark Diagram ...
Страница 35: ...PT6800 Service Manual 34 Figure 10 PT6800 Key Board Top Layer Position Value Diagram ...
Страница 36: ...PT6800 Service Manual 35 Figure 11 PT6800 Key Board Bottom Layer Position Value Diagram ...
Страница 40: ...PT6800 Service Manual 39 Figure 16 KBC 60Q Schematic Circuit Diagram ...
Страница 41: ...PT6800 Service Manual 40 Figure 17 PCB Layout 1 ...
Страница 42: ...PT6800 Service Manual 41 Figure 18 PCB Layout 2 ...