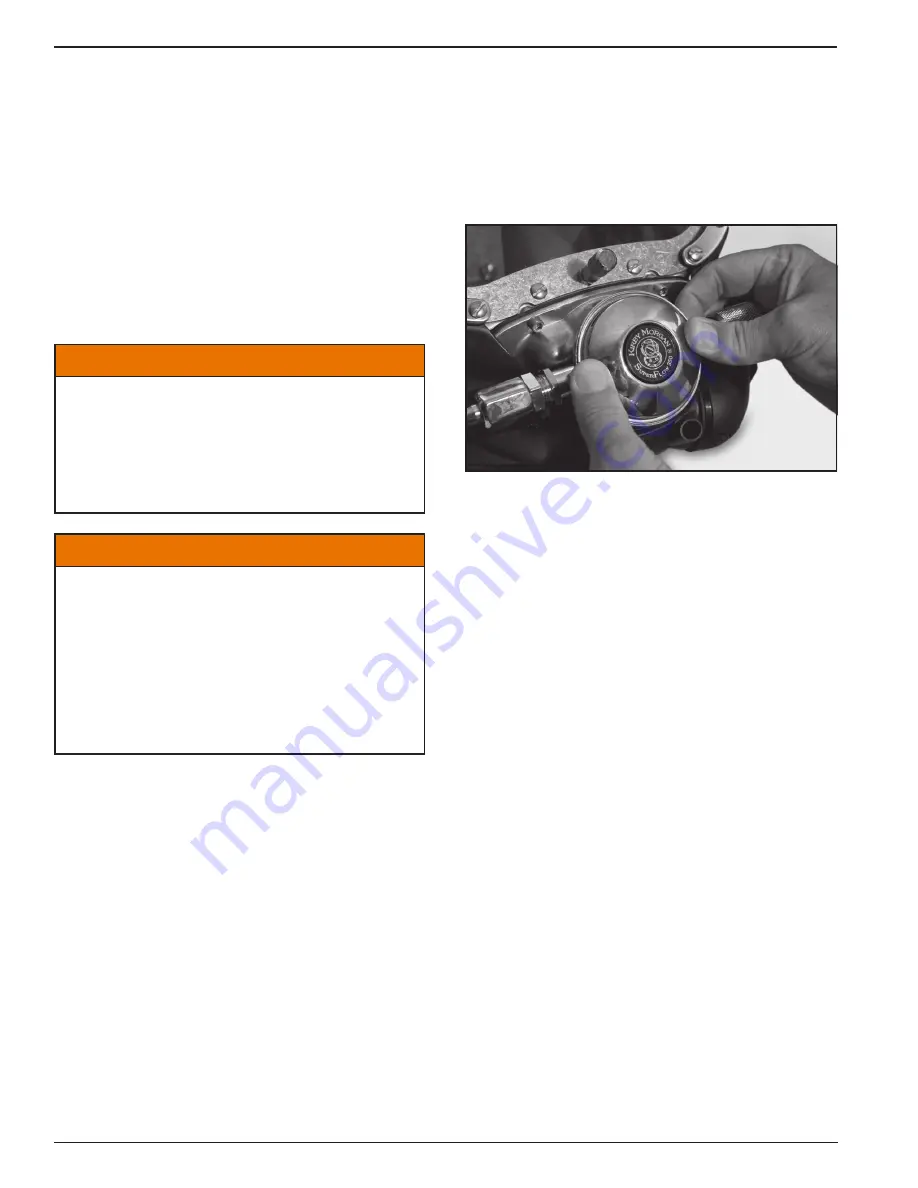
SF350-22
© MMXIX Kirby Morgan Dive Systems, Inc. All rights reserved. Document # 190625006
Reassembly of the SuperFlow® 350 Demand Regulator
SuperFlow® 350 Regulator
regulator and a second one has accidentally
been installed. If this is the case, the second
washer must be removed.
C) The regulator body has never been prop-
erly serviced and there is corrosion inside
the body, making proper inlet valve travel
impossible.
5) Check the free play at the lever. The lever
should have between
1/16
–
1/8
inch (1.5-3.0 mm)
play. If adjustment is necessary, adjust using the
alternate tools previously listed.
B
WARNING
The lock nut must not be loosened
more than
1/8
turn to lower the height
of the lever. If more adjustment is nec-
essary the lever should be bent down-
ward. If the lock nut is loosened more
than
1/8
turn the lever will not have
enough travel for proper flow rates.
B
WARNING
The lock nut must always be replaced
if removed from the inlet valve. The
plastic material that locks the nut is
not designed for multiple reuse. If the
nut comes loose during a dive the
regulator would free flow heavily. In
the situation where the diver is using
bottled breathing gas this would result
in a rapid consumption of breathing
gas.
Alternate method: If a KMDSI P/N 525-620
tool kit is not avail able, a small jeweler’s screw-
driver or metal scribe can be inserted in the slot
on the end of the inlet valve to keep it from rotat-
ing, and needle nose pliers may be used to rotate
the lock nut. While holding the slot of the inlet
valve to prevent rotation, carefully rotate the nut
“In” (clockwise to remove lever play and “Out”
(counterclockwise) to increase lever play.
Only turn the adjustment nut
1/8
turn at a time.
Depress the lever momentarily after each adjust-
ment and observe the lever play. It may be nec-
essary to complete this procedure several times,
as the procedure requires estimating the proper
position of the nut. If the regulator free flow does
not stop after this procedure, refer to regulator
disassembly and cleaning sections of this man-
ual.
6) When adjustment is complete, place the dia-
phragm and cover in place, and press tightly
down on the cover to simulate the action of the
clamp.
Press the cover over the diaphragm.
NOTE: (Reference, instructions following) Before
bending the lever, double check the adjustments.
The lever rarely requires bending. Usually levers
require bending only when improperly serviced,
or if damaged during disassembly.
7) With the cover pressed tight against the dia-
phragm, if the regulator starts to free flow, the
lever may need to be bent down slightly. If the
regulator does not free flow, slowly depress the
purge button until a slight free flow develops.
The purge button should depress no further than
1/8
inch (3.0 mm) before the regulator develops a
flow.
If the regulator does not develop a slight free flow
when the purge button is depressed in
1/8
inch (3.0
mm), then the lever will require slight upward
bending.
8) Install the clamp and clamp screw. Tighten
the screw to the correct torque (see appendix for
torque specifications).
9) Again, press on the purge button in the cover.
It must have
1/16
inch (1.5 mm) minimum and
1/8
inch (3.0 mm) maximum free travel before it con-
tacts the diaphragm. If there is more than
1/8
inch
(3.0 mm) travel, the lever must be bent upward,