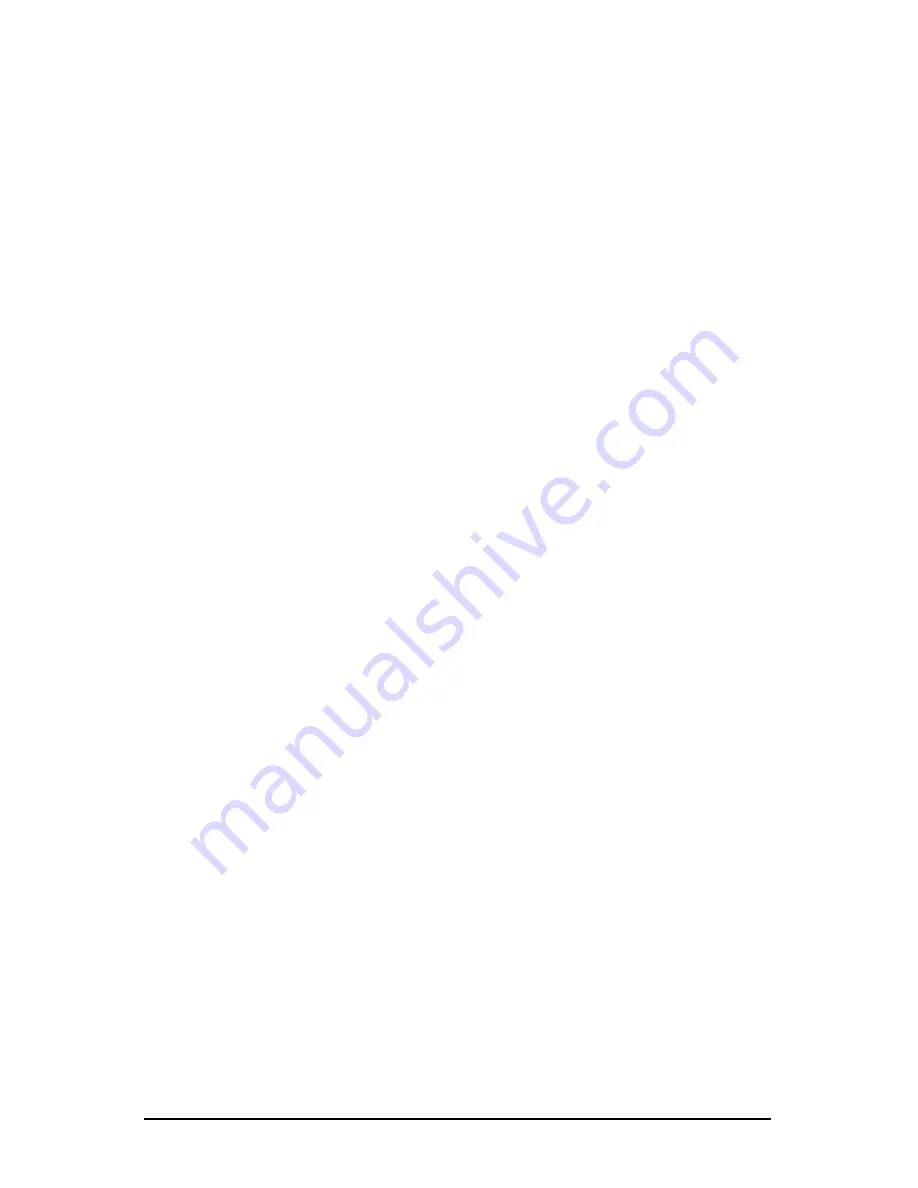
14
© ⅯⅯⅩⅡ Kirby Morgan Dive Systems, Inc. All rights reserved. Document # 120613008
Problems And Their Possible Causes
locating and correcting the problem. Visual inspections should include checking
all screws for tightness, all solder joints for correctness, broken parts, corrosion,
electrolysis, foreign material, check connectors for proper insertion and align-
ment. Check to see that unit is turned on, speaker on.
Check that battery condition is ok, (battery condition indicator). Operate from
line voltage or charge batteries, depending upon options.
Check to see that connections are proper, correct if necessary.
Check operating voltage, using a digital voltmeter or equivalent, measure the
voltage across the yellow push to talk jacks on the front panel. The voltage must
be greater than 9 volts D.C. for the unit to operate reliably.
Low Volume
Check volume control settings, adjust if desired. Check diver connections, cor-
rect if bad. Use diver radio field check procedure. Check for low batteries.
Garbled Voice to Diver
Tender volume to diver is set too high – reduce diver earphone volume. Divers
earphones corroded or defective, replace same. Tender’s microphone (speaker)
defective or full of moisture, empty water out of speaker or replace tender head-
set. Check diver communication cable and connections.
Garbled Voice to Tender
The diver volume to tender is set too high; reduce tender volume. Tender’s head-
set is marginal, speaker has water in it, or diver’s microphone is marginal, dam-
aged communication cable or connections. Substitute with known good units to
determine exact problem and correct.
Diver Cuts Out
Check for intermittent connection, substitute system components with known
good units to determine exact problem and correct fault.
Connections:
Most diver communications problems are caused by bad connections. The time
spent in making good connections will result in years of good communications.