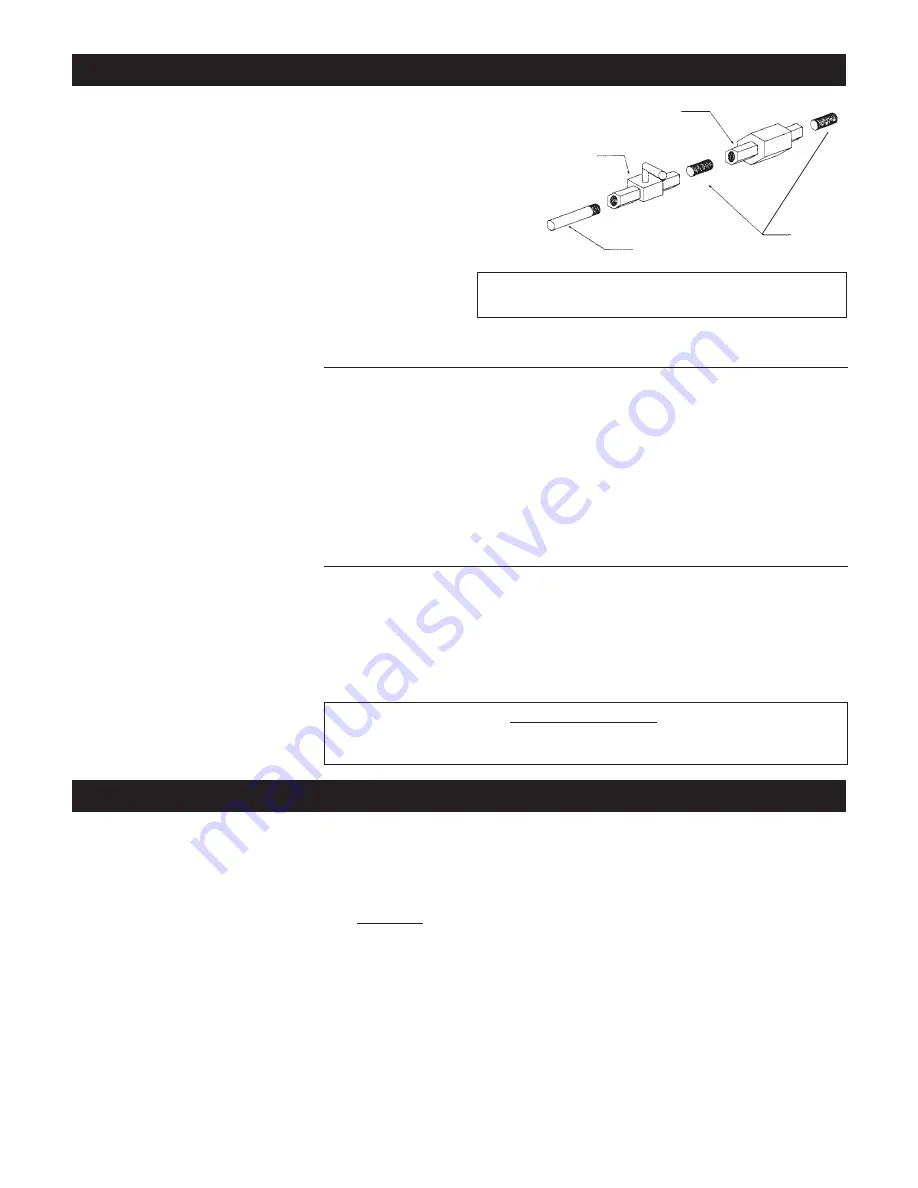
This gas appliance should be installed by a qualified installer in accordance with local
building codes and with current CAN/CGA - B149.1 or .2 installation codes for Gas
Burning appliances and equipment in Canada and the National Fuel Gas Code ANSI
Z223 in the U.S.A.
1. The gas pipeline can be brought in through either the right or the left side of the
appliance. A knockout is provided at either location to allow for the gas pipe
installation and testing of any gas connection.
2. The gas control inlet is 3/8” NPT. Typical installation layout for rigid pipe is
shown at right.
3. When using
copper
or
flex connector
, use only approved fittings. Always pro-
vide a union so that gas line can be easily disconnected for burner or fan servic-
ing. See gas specification for pressure details and ratings.
4. When a vertical section of gas pipe is required for
the installation, a condensation trap is needed. See
CAN/CGA-B149.1 or .2 for code details.
5. For natural gas, a minimum of 3/8” iron pipe with
gas minimum pressure of 4.5 w.c. must be used
for supply from the gas meter. Consult with the
local gas utility if any questions arise concern-
ing pipe sizes.
6. A 1/8” NPT plugged tappings are accessible for
test gauge connection both on the inlet and outlet
of the gas valve.
7. Turn the gas supply ON and check for leaks. DO
NOT USE OPEN FLAME FOR THIS PURPOSE.
Use an approved leak testing solution.
8. The appliance and its individual shutoff valve
must be disconnected from the gas supply piping
system during any pressure testing of that system
at test pressures in excess of 1/2 PSIG (3.5 KPa).
9. The appliance must be isolated from the gas sup-
ply piping system by closing its individual shutoff
valve during any pressure testing of the gas sup-
ply piping system at test pressures equal to or less
than 1/2 PSIG (3.5 KPa).
Note: The gas line connection may be made of 1/2”
rigid pipe, 1/2” copper pipe or an approved flex
connector. Since some municipalities have addi-
tional local codes, it is always best to consult your
local authorities and the current CAN/CGA -
B149.1 or .2 installation code in Canada or the
National Fuel Gas code ANSI Z223.1 in the U.S.A.
9
General Glass Information
Glass Cleaning
It will be necessary to clean the glass periodically. During start-up,
condensation, which is normal, forms on the inside of the glass and
causes dust, lint etc. to cling to the glass surface. Also, initial paint
curing can deposit a slight film on the glass. It is therefore recommended
that initially the glass be cleaned two or three times with non-abrasive
common household glass cleansers and warm water. After that, the
glass should be cleaned two or three times a season depending on the
circumstances.
Cautions and Warnings
• Do not clean when the glass is hot.
• The use of substitute glass will void all product warranties.
• Care must be taken to avoid breakage of the glass.
• Do not operate this fireplace without the glass front or with a broken
glass front.
• Do not strike or abuse glass.
Glass Replacement
REPLACEMENT GLASS FOR BOTH DIRECT VENT UNITS
Model ZDV4224N and ZDV4224LP can use either tempered glass or
Robax ceramic or coated Neaoceram glass. Must be 5mm thick.
Only Robax ceramic or coated Neaoceram glass may be used for replace-
ment for Model ZDV4228N, ZDV4228LP, ZDV4232N and
ZDV4232LP. Must be minimum 5mm thick.
Removal of the Glass Door
1. Remove the two screws located behind upper grill or unfasten latch-
es if so equipped.
2. To remove, pull frame forward and lift from bottom door retainer.
3. To replace glass, clean all materials from door frame. Using a high
heat silicone temperature-resistant to 500°F (260°C) apply a bead of
approximately 1/32” to all four sides of frame and insert glass with
new gasket. Frame should be on flat surface, with a small amount of
weight pressing glass into silicone. Let dry approximately 15 to 20
minutes. The door can be re-installed by reversing Steps 1 & 2.
Gas Line Installation
Gas Specifications
Models
ZDV4224N
ZDV4224LP
ZDV4228N
ZDV4228LP
ZDV4232N
ZDV4232LP
Fuel
Natural
Propane
Natural
Propane
Natural
Propane
Gas Control
Millivolt adjustable
Millivolt adjustable
Millivolt adjustable
Millivolt adjustable
Millivolt adjustable
Millivolt adjustable
Maximum
24,000 BTU High
22,000 BTU High
28,000 BTU High
26,000 BTU High
30,500 BTU High
29,200 BTU High
Input
14,000 BTU Low
15,000 BTU Low
20,000 BTU Low
19,000 BTU Low
20,600 BTU Low
22,200 BTU Low
Maximum
n/a
n/a
21,000 BTU High
19,500 BTU High
22,900 BTU High
21,900 BTU High
Output
Orifice Size
#42
#53
#37
#52
#36
#51
(0 - 4500 ft)
Air Shutter
1/8” Open
Fully Open
.218” Open
Fully Open
.187
.312
.25”
.625” Open/
Gas Inlet Size
S.I.T. 820 Nova, 3/8” NPT
Gas Supply Pressure
Minimum
Normal
Maximum
Natural Gas
5.5”
7”
9”
Liquid Propane
11”
11”
12”
Manifold Pressure
Natural Gas
Liquid Propane
Manifold Pressure High
3.5 IN. W.C./.87 KPa
10 IN. W.C./2.61 KPa
Manifold Pressure Low
1.6 IN. W.C./.40 KPa
6.3 IN. W.C./1.57 KPa
3/8” UNION
3/8” NIPPLE
1/2” x 3/8” SHUTOFF VALVE
1/2” GAS SUPPLY
For the state of Massachusetts a
T-handle gas shut-off valve
must be used on a gas appliance.
This T-handle gas shut-off valve must be listed and approved by the state of Massachusetts.
This is in reference to the state of Massachusetts state code CMR238.
Important:
Always check for gas leaks with a soap and water solution. Do not use
open flame for leak testing.