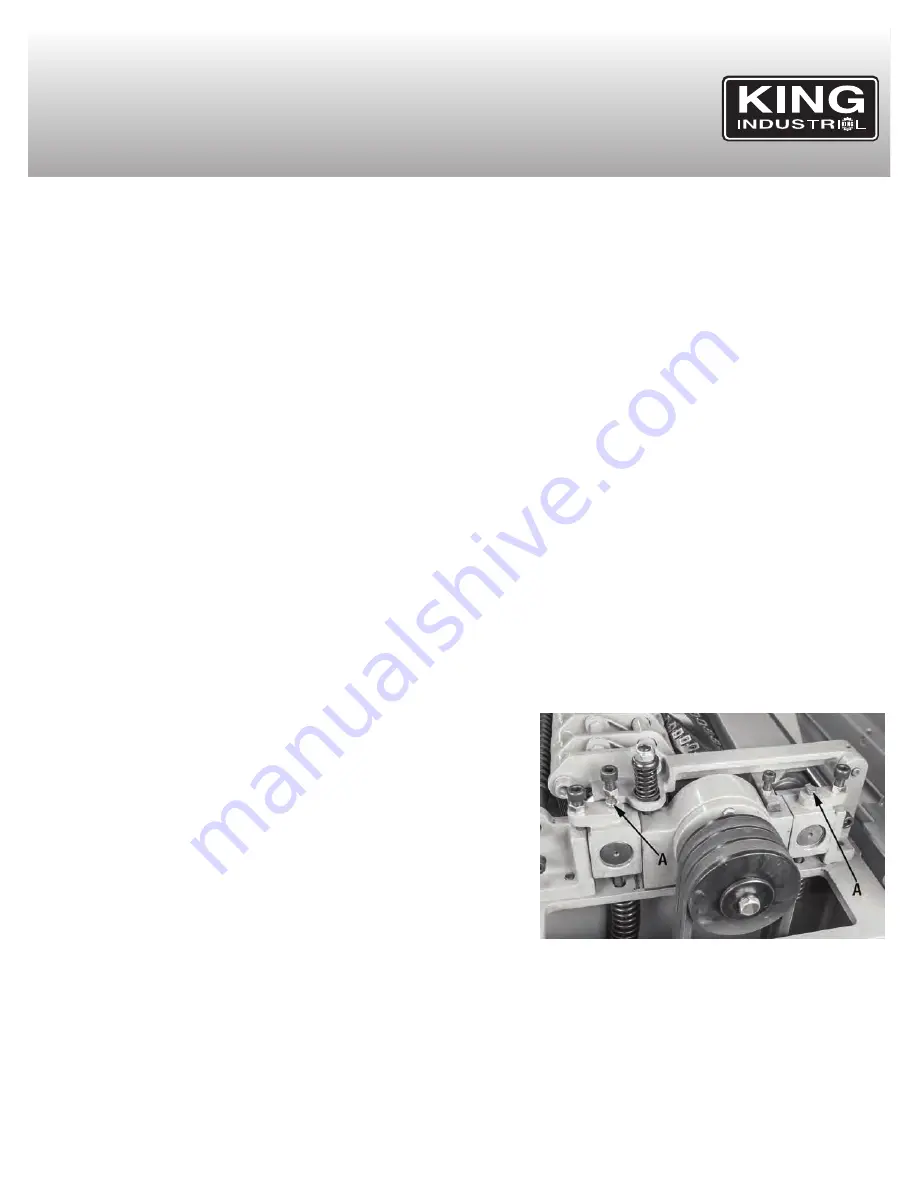
MAINTENANCE
MAINTENANCE
WARNING!
TO REDUCE THE POTENTIAL FOR PERSONAL INJURY MAKE SURE THE MACHINE IS TURNED OFF BEFORE PERFORMING
ANY MAINTENANCE OPERATIONS.
REGULAR MAINTENANCE CHECkLIST
1. Make sure that everything has been installed properly. Check to make sure that all parts are secured properly before using the machine.
2. Keep the machine clean, and regularly clear the machine of sawdust and debris.
3. Make sure you are wearing proper attire for operating machinery. This includes safety glasses, and hearing protection. Avoid loose-fitting
clothing, jewelry such as watches or bracelets, or anything that could be caught by moving parts (either the machine itself or the workpiece).
4. Make sure the cutter inserts are secured properly to the cutterhead.
5. Make sure the feed rollers, table rollers, pressure bar, and chipbreakers are set properly.
6. Make sure the workpiece material is suitable for planing.
PERIODIC MAINTENANCE CHECkLIST
1. Occasionally coating the table surface with paste wax can help protect the table surface, and make it easier for the workpiece to slide along
it.
2. The motor and cutterhead bearings are sealed. They do NOT require additional lubrication. However, the drive gears, chain, and elevation
screws should be cleaned once every 10-15 hours of use. Remove the old grease, and apply a generous coating of common automotive
bearing grease.
3. Regularly inspect planed or moulded workpieces for signs of wear or damage to the cutter inserts. Rotate or replace worn or damaged cutter
inserts immediately.
4. Avoid the use of silicon based products on the machine, as these could interfere with wood finishing products.
LUbRICATION
The feed rollers (infeed and outfeed) should be lubricated every 50-100 hours of
use or as needed. To lubricate the feed rollers:
1. Remove the caps (A) Fig.28 covering the oil cups, and add a few drops of 10W
machine oil.
2. Repeat the same step on the other side of the machine.
FIGURE 28